A new paper in the journal Materials has explored how the recovery of iron from waste streams can improve the aims of the circular economy for industry. Scientists from two universities in Romania have collaborated on the research.
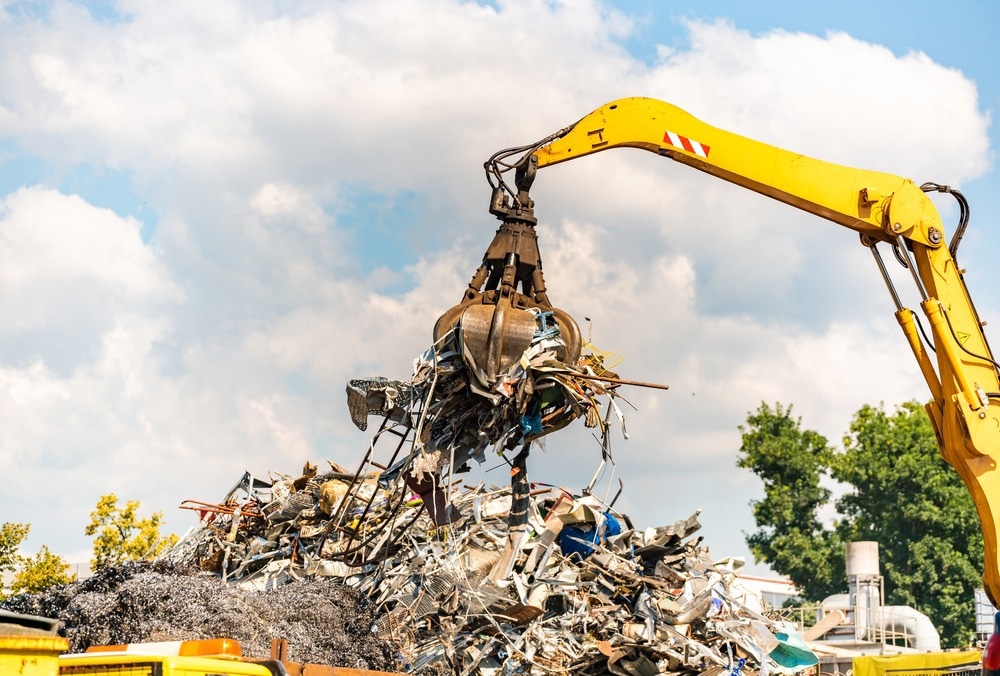
Study: Recovery of Waste with a High Iron Content in the Context of the Circular Economy. Image Credit: Przemek Iciak/Shutterstock.com
The Circular Economy
Critical issues with waste and pollution have demonstrated the need to move rapidly from a linear economy, where resources are extracted, utilized, and then wasted at the end of their useful life, to a circular model. In a circular economy model, valuable resources are recovered from critical waste streams and reused to produce value-added products.
Currently, vast levels of waste are produced worldwide per year, with the extraction of valuable minerals driving climate change and threatening vulnerable ecosystems and communities across all parts of the globe. Moving from our currently wasteful practices will require several innovative and interconnected approaches, including government regulations, new manufacturing practices, and the implementation of global infrastructure for purposes such as recycling.

By-products made from waste with high iron content. Image Credit: Ardelean, E et al., Materials
Ferrous Alloys and the Circular Economy
Ferrous alloys are used in multiple industries, including construction, the automobile industry, aerospace, military, civil engineering, and the consumer market. These industries produce vast amounts of waste materials, both from manufacturing processes and end-of-life products.
Improving the circularity of ferrous alloy waste is crucial for these industries to enhance their sustainability and meet net zero targets by 2050. Aside from problems with waste (which is commonly sent to landfills) manufacturing processes drive climate change due to the harmful emissions produced worldwide.
All stages of the manufacturing process and lifecycle of products must be considered to improve the circularity of ferrous materials. This includes the extraction of raw minerals, transportation, conversion of resources into useful products, management of waste, and recycling. Additionally, suitable processes are needed to valorize the materials recovered from waste streams.
The utilization of co-products produced during manufacturing has the potential to improve the steelmaking industry’s sustainability. These co-products include slag, slurries, dust, and products from milling. A current issue that the iron and steelmaking industry faces is the storage of waste products such as powdery waste as these materials can have a negative environmental impact if not stored and disposed of properly.
Another key issue that currently hinders the efficient recovery and reuse of waste materials such as slag and powder is the presence of contaminants such as zinc, selenium, copper, and nickel that are used in various manufacturing processes. Repeated processing can potentially increase the levels of these contaminants, which can have serious effects on the quality of products produced from waste.
Recovery of useful raw materials from waste is crucial both in terms of ecological friendliness and from an economic standpoint. It is predicted that the market share of products produced from ferrous waste will increase in the mid-to-long term. This will reduce the need to exploit finite raw materials and thus mitigate the environmental impact of mining and mineral processing.
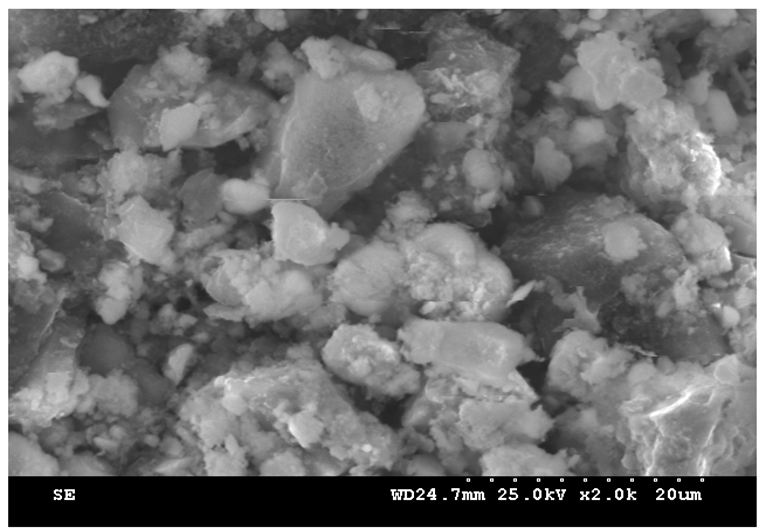
Image of sintering sludge, 4000×. Image Credit: Ardelean, E et al., Materials
The Study
The current work has investigated the potential of producing valuable products from process waste streams in the iron and steelmaking industries. Sludge briquettes from sources such as ferrous sludge and ferrous sludge have been evaluated in the research. Sludge samples were sourced from various sources such as sludge warehouses and steel plants.
Powdered waste was also investigated in the research. Qualitative and chemical analysis was performed on all samples. The authors categorized different particle sizes and morphological characteristics of waste materials.
Briquetting was chosen as it is a reliable and straightforward process. In this process, compaction forces can be adjusted to produce briquettes with distinct characteristics. Furthermore, this process can be easily automated, which improves its industrial and commercial viability.
Laboratory-scale tests were performed to determine the technological characteristics of briquette samples. These were resistant to crushing and cracking. A universal compression/traction testing machine was employed to conduct these tests. Algorithms were employed in the study to optimize the chemical composition of samples and determine optimal mechanical characteristics.
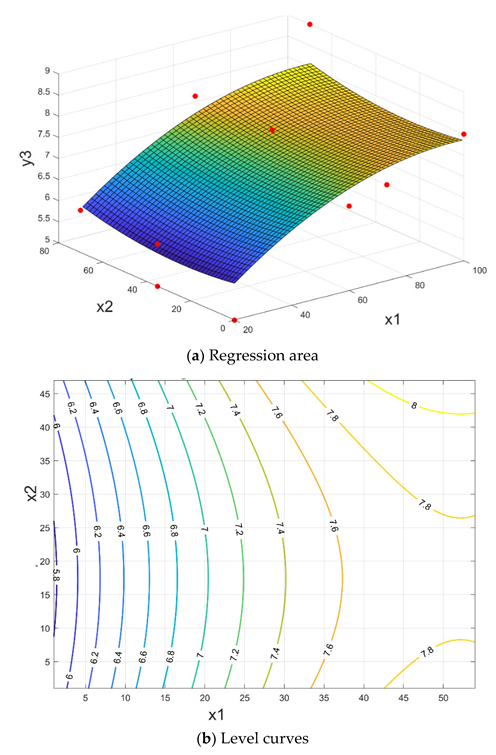
The briquettes crush range depending on the proportion of ferrous sludge and sludge mill scale, for a medium value of sintering sludge y3 = f (x1, x2, x3 med). Image Credit: Ardelean, E et al., Materials
Results of the Study
The authors have determined that briquetting is a suitable process for recovering valuable waste products from waste streams, such as sludge and powdery ferrous materials that would otherwise be wasted. Large particle-sized waste can be efficiently recovered in this process to produce secondary products. Mechanical strength characteristics were observed that were higher than the minimum value.
By using genetic algorithms, a mathematical model can be constructed to determine the briquette recipe’s optimal range of variations. Genetic algorithms were found to be advantageous for this purpose, being more efficient than conventional methods, which use a step-by-step process for solving problems.
Enhanced quality indicators can be obtained by optimizing the process or making changes to the raw batch materials, according to the authors. Binders could be used to avoid hot hardening, and precise control of chemical composition is necessary. These are opportunities for future research in the field of recovering ferrous waste materials and improving the steel and iron-making industry’s sustainability.
Further Reading
Ardelean, E et al. (2022) Recovery of Waste with a High Iron Content in the Context of the Circular Economy Materials 15(14) 4995 [online] mdpi.com. Available at: https://www.mdpi.com/1996-1944/15/14/4995
Disclaimer: The views expressed here are those of the author expressed in their private capacity and do not necessarily represent the views of AZoM.com Limited T/A AZoNetwork the owner and operator of this website. This disclaimer forms part of the Terms and conditions of use of this website.