A team of researchers recently published a paper in the journal Additive Manufacturing that demonstrated the feasibility of using a proposed two-dimensional (2D) computational fluid dynamics (CFD) model to investigate the key aerodynamic interactions influencing the morphology of the aerosol jet printed features to optimize the printing process and predict the printing defect occurrence.
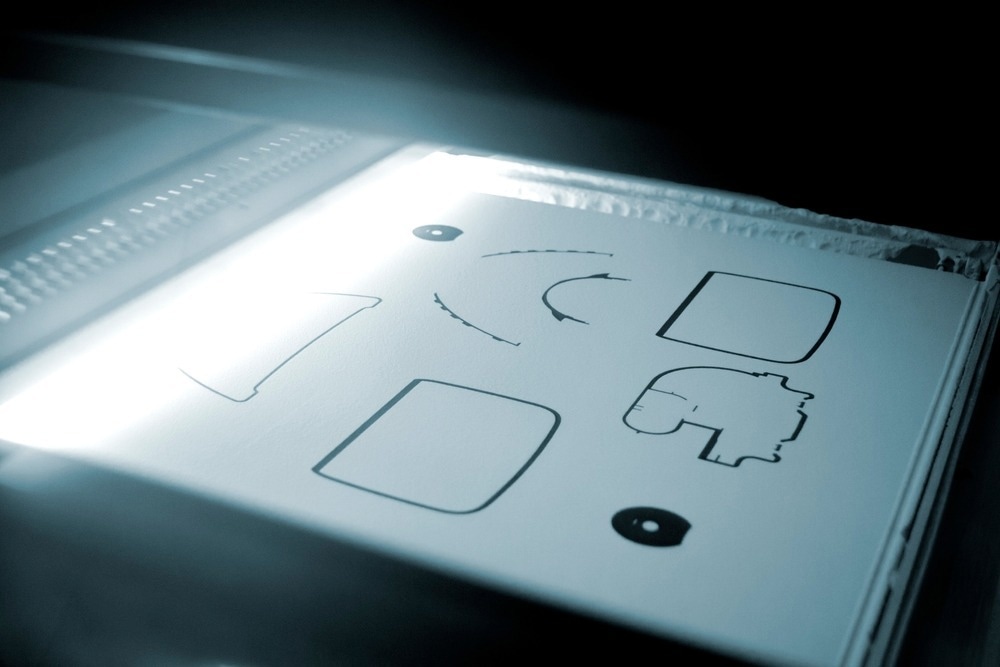
Study: Numerical and Experimental Investigation of Aerosol Jet Printing. Image Credit: MarinaGrigorivna/Shutterstock.com
Background
Aerosol jet printing (AJP) has gained considerable attention with the growing adoption of digital manufacturing. The direct-write, contactless method has been evaluated extensively to fabricate smart packaging systems, flexible electronics, and embedded sensors.
AJP is more advantageous compared to inkjet printing, another maskless printing technique, as it is suitable for micro-scale electronic device fabrication on conformal, non-planar substrates and can print features at higher resolution. This technique depends on complex interactions between several process parameters, such as substrate characteristics, nozzle geometry, ink properties, and atomizer settings.
In AJP, the aerosolized ink droplets are initially transported using a carrier gas to the printhead transition region, where the annular sheath gas envelops the aerosol stream to facilitate collimation and constriction. This three-way multiphase fluid interaction leads to a high-density deposit of aerosol droplets with significantly smaller feature sizes compared to a typical nozzle diameter.
However, the sub-optimal gas flow conditions in the aerosol jet printhead often lead to printed features with over-deposition, material inadequacy, and high edge roughness. Among the causal factors, the volumetric flow rates of carrier gas (CGFR) and sheath gas (SGFR) significantly affect the print quality in AJP.
The carrier gas and annular sheath gas engage in a volume displacement interaction, which facilitates the collimation of the incoming aerosol stream and deposition of narrow features. Typically, the SGFR to CGFR ratio/flow focusing ratio is optimized to realize sufficient aerosol stream collimation before deposition. In commercial AJP systems, one or several aerodynamic lenses are also utilized to focus the aerosol stream exiting the printer nozzle.
Thus, investigating the complex fluid interactions transpiring in printheads using sophisticated computational models that can provide insights required for decision-making during parametric optimization is necessary to rectify the substandard deposition and transport of aerosolized ink streams.
The Study
In this study, researchers identified the fundamental aerodynamic interactions that govern the multiphase flow in AJP using a 2D CFD model. The study aimed to relate the numerically obtained aerosol trajectories and flow fields to morphological signatures observed in the AJ printed features.
Governing equations were solved numerically to calculate the crucial flow variables at several discrete points throughout the fluid domain under laminar and compressible flow assumptions. Researchers performed randomized single-factor numerical experiments to determine the role of SGFR, CGFR, flow focusing ratio, aerosol droplet diameter, and overall gas flow rate (OGFR).
The aerosol stream trajectories through the fluid domain at different process conditions were predicted using a Lagrangian discrete phase model. Additionally, a mathematical model was employed to predict the aerosol stream width at the nozzle exit. The Rosin-Rammler distribution was used to model the droplet diameter distribution polydispersity.
Researchers also performed experimental investigations using an ultrasonic AJP system and compared the experimental measurements with the numerical results to confirm the reliability and accuracy of the numerical simulation.
Ultrasonic AJP typically involves five steps, including ink aerosolization using an ultrasonic transducer, transportation of the aerosolized droplets using a carrier gas, aerosol stream collimation using sheath gas, aerodynamically focusing of the collimated aerosol stream, and aerosol-gas mixture impingement or impaction on a substrate. These steps are performed sequentially.
A Nanojet™ aerosol printing system was used for all printing experiments. Compressed purified dry air stored at 25 oC was used for carrier and sheath gases. Results obtained using a printing nozzle with a 150 µm nominal inner diameter were considered for evaluation. Silver nanoparticle ink diluted with distilled water was used for printing trials.
Polycaprolactone (PCL) substrates cleaned in an isopropyl alcohol-containing bath, air-dried, and treated with corona plasma to improve the wetting behavior were used for the deposition process. A JEOL IT100LA scanning electron microscope and Hirox KH 7700 digital microscope were used to analyze the dimensions and morphology of the printed lines, while the ImageJ was used to analyze the deposited lines.
Observations
The results from the 2D CFD model built on assumptions of compressible, incompressible, and laminar flow demonstrated a good agreement with the measurements obtained from the printing experiments using the Nanojet™ ultrasonic AJP system. Thus, the predictions made by the proposed 2D CFD model can be used reliably to complement the experimental trials while optimizing the printing conditions for the formulation of novel inks.
The simulation results displayed the significance of maintaining the OGFR within a tight window to maximize the chances of obtaining high-resolution features and minimize the occurrence of printing defects.
The width of the ink stream exiting the printer nozzle using the mathematical model. This model provided an accurate and quick estimate of the printed line widths without requiring extensive experimentation.
Narrower line widths without overspray were achieved when aerosol drops with larger diameters were produced and transported to the flow-focusing system. However, CGFR did not always provide sufficient energy to transport larger aerosol drops out of the mist cup.
Aerosol droplets of desired sizes were produced by optimizing the ink formulation, in addition to using a printing nozzle with a smaller diameter and a higher SGFR. Rheological properties of the ink, including surface tension and viscosity, and the ultrasonic transducer frequency and power primarily influenced the droplet size distributions. Thus, the ink properties must be adjusted carefully to achieve desired droplet sizes.
Conclusion
To summarize, the findings of this study demonstrated the feasibility of using the proposed computational framework to predict the occurrence of printing defects and optimize the printing process in AJP. However, sophisticated numerical models must be developed to explain the dynamics of the substrate-ink interactions in a detailed manner.
Additionally, more research is required to model the droplet transport effectiveness from the mist cup to the flow focusing assembly as a function of carrier gas density and flow rate, droplet size, and mist cup geometry to realize high-resolution printing with AJP.
More from AZoM: How Does Laser Cleaning Technology Function?
Disclaimer: The views expressed here are those of the author expressed in their private capacity and do not necessarily represent the views of AZoM.com Limited T/A AZoNetwork the owner and operator of this website. This disclaimer forms part of the Terms and conditions of use of this website.
Source:
Rao, P., Ramesh, S., Mahajan, C. et al. Numerical and Experimental Investigation of Aerosol Jet Printing. Additive Manufacturing 2022. https://doi.org/10.1016/j.addma.2022.103090