In a paper recently published in the open-access journal Materials, researchers devised a novel effective reduction technique for producing porous pellets to promote mass transfer in the production of magnesium. It was determined that this can enhance the reduction efficiency while improving the pellet reactivity.
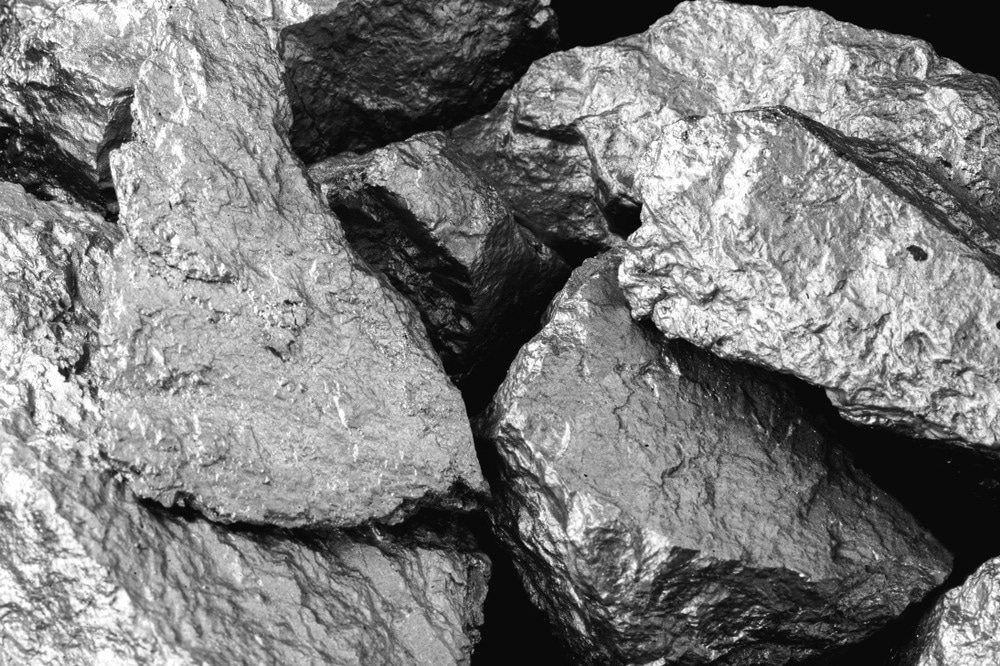
Study: Novel Efficient Reduction Route for Magnesium Production Using Silicothermic Process. Image Credit: RHJPhtotos/Shutterstock.com
Background
Magnesium is one of the lightest metals that form the basis of construction alloys and is also effective at shielding electromagnetic interference. These characteristics are fundamental for magnesium's extensive development potential.
Presently, the primary methods for magnesium production include electrolysis and thermal reduction. Since the Pidgeon method offers the benefits of low investment, low cost, and short process flow, it has been used to generate about 80% of the world's primary magnesium in China since 2007. However, the magnesium sector has stagnated in the previous decade because of pollution, excessive energy consumption, high costs of production, and a lack of alternatives to these challenges. As a result, magnesium synthesis utilizing carbon rather than silicon has emerged as a significant study area owing to its low usage and environmental benefits.
The Pidgeon method extracts magnesium vapor from pellets through a thermal reduction reaction at 1200°C under a vacuum totaling 10 Pa, with a reduction energy usage of about 3tce/tMg. In this study, the factors impacting mass transport on magnesium synthesis utilizing the Pidgeon method and the present critical process were examined.
It was discovered that once the powder was compressed into pellets, the operational distance between the reducing agent and the raw material decreased, which was beneficial to the solid substances’ mutual diffusion. However, it also elevated the magnesium vapor resistance released from the pellets. In order to address this issue, a novel approach for improving mass transfer in magnesium synthesis by creating porous pellets was presented.
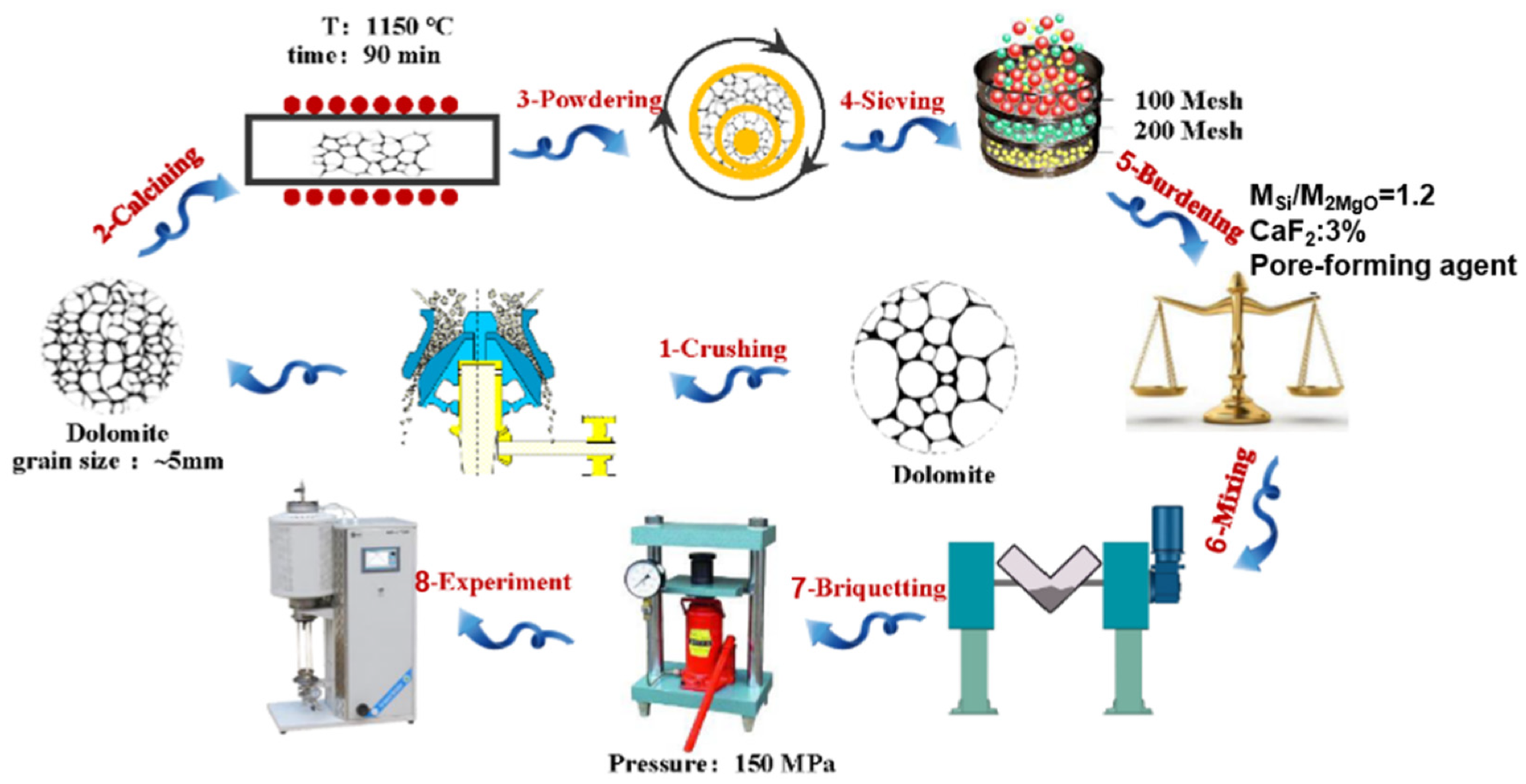
The craft of pellet preparation. Image Credit: Chen, Y et al., Materials
About the Study
In the present study, the same raw materials were used as the ones in a conventional Pidgeon method. Starting material used was calcined dolomite (CaO.MgO); a 75% ferrosilicon (Fe.Si) alloy was the reducing agent. The mineralizing agent was fluorite (CaF2), while 99.9% ammonium bicarbonate (NH4HCO3) was the pore-forming agent.
Some amount of uniform particle-sized dolomite was calcined at 1,150 °C in a muffle furnace for 90 minutes, yielding calcined dolomite having a 47.4% burning loss rate and 30% activity. The dolomite and the 75% Fe.Si were ground using a 100-mesh screen. Furthermore, NH4HCO3 as the pore-forming agent was added in varying ratios to the raw materials, followed by thorough mixing. Finally, the pellet samples’ weight loss curve was obtained after placing them in a vacuum tube furnace, followed by recording the real-time weight change.
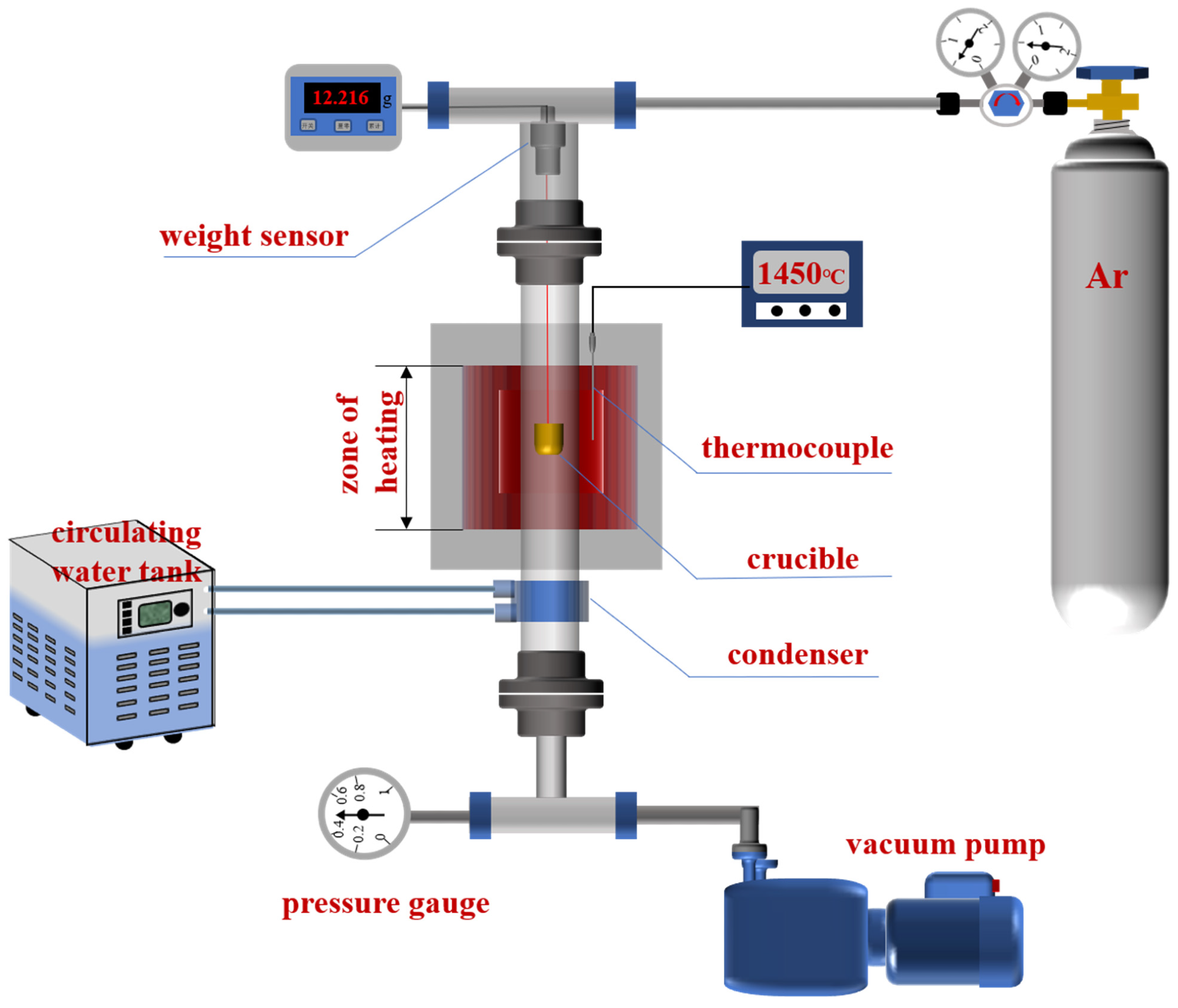
Working principle of the reaction device. Image Credit: Chen, Y et al., Materials
Observations
The gas molecules created due to the pyrolysis of the pore-forming agents are released from the pellets upon sample heating. Following the escape of the gas molecules, cavities bearing strong connectivity were formed within the pellets. This minimizes the resistance to magnesium escape and enhances the magnesium production efficiency as well as the smelting efficiency.
Due to the varying densities of raw materials and the pore-forming agents, the overall pellet density fell to 1.65 g/cm3 from 1.79 g/cm3 when the pore-forming agent ratio increased to 30%. The mass change curves indicated a visible chemical reaction of the pellets in the absence of a pore-forming agent during heating. Furthermore, the evidence of 2CaO.SiO2 as the residual component following the reaction indicated the turning of the pore-forming agent into gas and its escape from the pellets. Additionally, there were no side effects of using NH4HCO3 as the pore-forming agent.
Overall, the reduction conversion curves of the five pellet samples exhibited an "S" pattern, indicating a characteristic solid-phase type of reaction. It can be inferred that increasing the porosity of the pellets reduces the magnesium vapor resistance caused by the reaction, leading to it being released from the pellets, thereby boosting the efficiency of the reduction. Once the porosity attains a particular value, however, a limitation in the reduction rate increase was observed. Although the magnesium vapor's escape resistance decreased, the gas release per unit flow channel was reduced as well. Thus, the wide porosity decreases the reaction materials' contact surface. Furthermore, excessive porosity affects the heat transmission properties of the pellets.
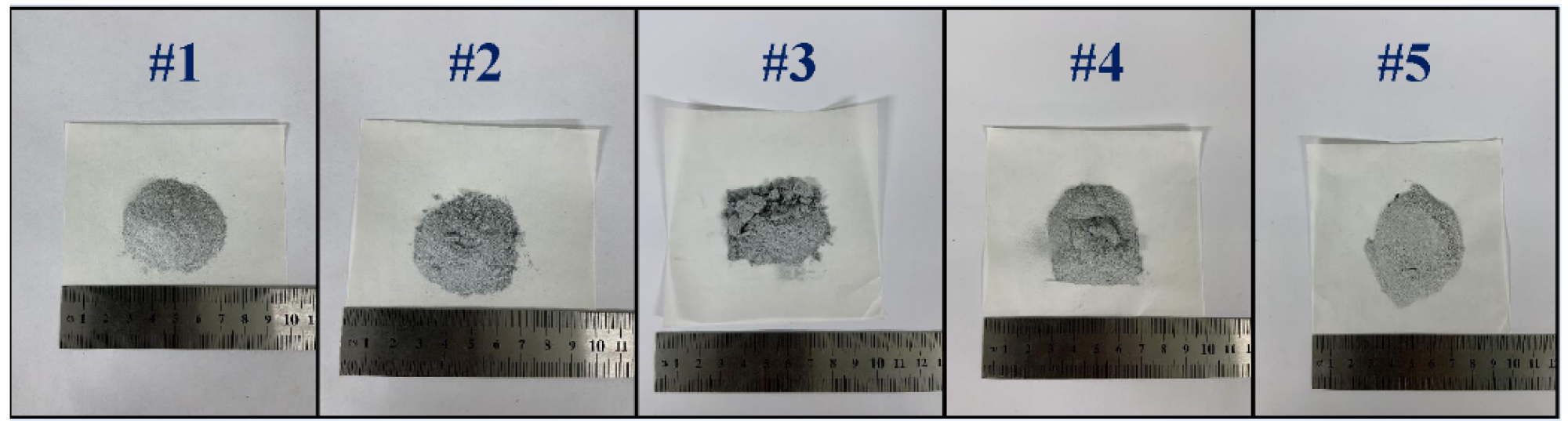
The residue after the reaction of different pellets. Image Credit: Chen, Y et al., Materials
Conclusions
To summarize, the researchers proposed a technological measure to improve the mass transfer in magnesium production by using the silicothermic process to analyze the impact of several factors on mass transfer.
Consequently, the experimental results confirmed that the selection of appropriate pore-forming agent proportions could vastly enhance the reduction and magnesium production efficiency, minimize energy usage, reduce the reduction time, and achieve emission reduction and energy savings.
Disclaimer: The views expressed here are those of the author expressed in their private capacity and do not necessarily represent the views of AZoM.com Limited T/A AZoNetwork the owner and operator of this website. This disclaimer forms part of the Terms and conditions of use of this website.
Source:
; Mai, G.; Che, Y.; He, J. Novel Efficient Reduction Route for Magnesium Production Using Silicothermic Process. Materials, 2022, 15, 6009. https://www.mdpi.com/1996-1944/15/17/6009