By Surbhi JainReviewed by Susha Cheriyedath, M.Sc.Oct 17 2022
In an article recently published in the journal Ceramics International, researchers discussed the foam-gel casting preparation and characteristics of porous ceramics made of high-strength mullite.
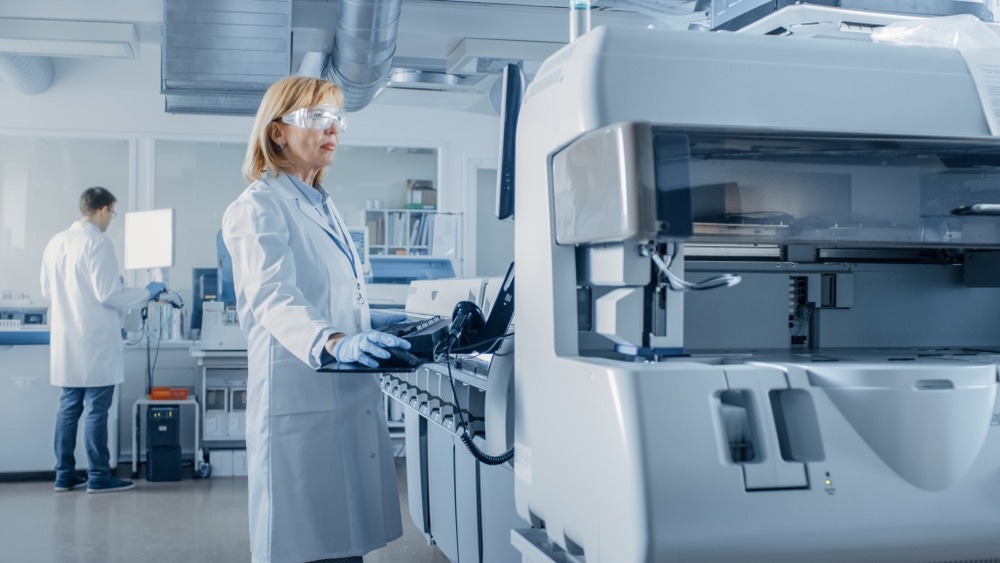
Study: Foam-gelcasting preparation and properties of high-strength mullite porous ceramics. Image Credit: Gorodenkoff/Shutterstock.com
Background
Due to their exceptional qualities, such as wide specific surface area, high mechanical strength, good chemical stability and permeability, low thermal conductivity, and density, mullite porous ceramics have received a lot of interest from researchers as a novel green ceramic material in recent years. Mullite porous ceramics' exceptional qualities and distinctive structure also increase their potential for use as catalyst supports, gas/liquid filters, thermal insulators, and in the biomedical field.
Mullite porous ceramics are prepared using a variety of techniques. Foam-gel casting is one of these techniques that has received a lot of interest due to its unique advantages. The traditional foam-gel casting method does, however, have certain drawbacks, including harsh environmental conditions, toxic monomers, and poor solid loading. When creating high-performance porous ceramics by the foam-gel casting method, the kind and content of the foaming agent are significant determining factors. Natural organisms and short- or long-chain surfactants are two frequent foaming agents.
About the Study
In this study, the authors discussed the development of porous ceramics made of mullite with a high apparent porosity by utilizing a foaming method and a non-toxic, cost-effective poly-glutamic acid (PGA) gelling system. The impacts of the foaming agent and sintering temperature on the apparent porosity, microstructure, and mechanical characteristics of mullite porous ceramics were determined. With a porosity value of up to 80.23%, the produced mullite porous ceramics demonstrated good characteristics with thermal conductivities and bulk densities of 0.17 W/(mK) and 0.62 g/cm3, respectively.
The team demonstrated that the mullite porous ceramics had a high proportion of distinctive near-spherical pores, which significantly increased compressive strength up to 6.1 MPa. Additionally, the photodegradation of methyl orange solution confirmed the possible use of mullite porous ceramics as catalytic supports.
The researchers made mullite porous ceramics with high porosity using the non-toxic and affordable -PGA gel casting technology using sodium dodecyl sulfate (SDS) as the foaming agent. Additionally, the impact of foaming agent dosage in the range from 0 to 0.8wt% and sintering temperature in the range from 1300 to 1600 °C on the microstructure and sintering characteristics of mullite porous ceramics was examined. Additionally, the prepared mullite porous ceramics' potential as thermal insulation materials and supports for high-performance catalysts was shown.
Observations
The compressive strength remained at 6.10 MPa when the apparent porosity was 80.23%. The samples' thermal conductivity and compressive strength were 1.266 W/(m.K), and 62.43 MPa, respectively, in the absence of a foaming agent. The samples' apparent porosity and bulk densities were 79.52% and 0.65 g/cm3, respectively, at a foaming agent dosage of 0.6 wt%. When the dosage was 0.6 wt%, the SDS concentration in the mullite slurry reached the critical micelle concentration, and the foaming agent molecules completely covered the air-water interface.
The slurry had a 0.2% bubble volume without the foaming agent. As the dosage of the foaming agent SDS incremented from 0 to 0.8 wt%, the foaming capacity also increased. The samples' linear shrinkage increased from 1.23 to 2.92% when the sintering temperature was raised from 1300 to 1600 °C. Additionally, the compressive strength increased from 11.4 to 12.37 MPa, the bulk density increased from 0.75 to 0.89 g/cm3, and the apparent porosity decreased from 76.38 to 72.32%.
The findings showed that although densification increased as the sintering temperature increased from 1300 to 1600 °C, the crystalline phase of the samples remained unchanged. The apparent porosity of the mullite porous ceramics increased to 80.23% at a sintering temperature of 1500 °C as the foaming agent dosage was increased from 0 to 0.8 wt%. The thermal conductivity at ambient temperature decreased to 0.17 W/(mK).
Conclusions
In conclusion, this study discussed a method for producing high-porous mullite porous ceramics effectively, which made use of a green, non-toxic γ-PGA gelling system using SDS as the foaming agent. A thorough investigation was done into how the sintering temperature and foaming agent dose affected the microstructure, crystalline phase, and physical characteristics of mullite porous ceramics.
The authors mentioned that porous ceramics made of mullite with a large specific surface area have unique properties that make them effective catalyst supports.
More from AZoM: How are Bioplastics Made?
References
Li, X., Li, S., Yin, Z., et al. Foam-gelcasting preparation and properties of high-strength mullite porous ceramics. Ceramics International (2022). https://www.sciencedirect.com/science/article/pii/S027288422203677X
Disclaimer: The views expressed here are those of the author expressed in their private capacity and do not necessarily represent the views of AZoM.com Limited T/A AZoNetwork the owner and operator of this website. This disclaimer forms part of the Terms and conditions of use of this website.