By Surbhi JainReviewed by Susha Cheriyedath, M.Sc.Oct 20 2022
In an article recently published in the open-access journal Scientific Reports, researchers discussed the development of laboratory tools that could measure bulk materials under difficult circumstances through 3D printing.
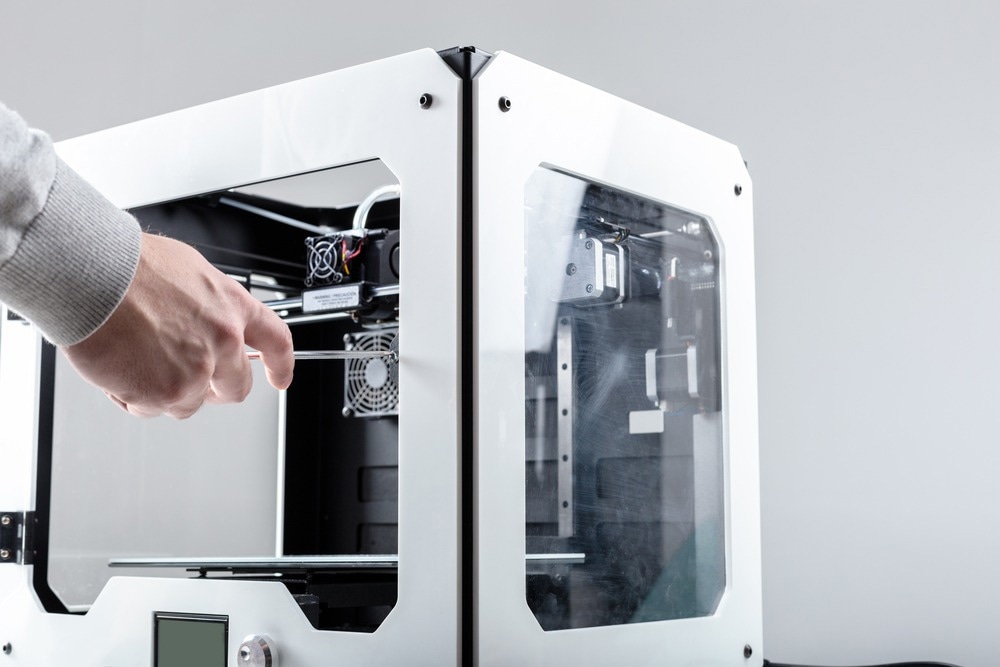
Study: 3D printed laboratory equipment to measure bulk materials in extreme conditions. Image Credit: FabrikaSimf/Shutterstock.com
Background
In the previous few decades, scientists and engineers made tremendous advancements in the exploration of planets and celestial bodies and learned about their resources and features. Aside from getting to the planets, it is still challenging to land safely anywhere in the universe. The goal is to gather information and formulate plans for developing radiation-shielding homes and landing locations, as well as for creating appropriate buildings. In the past ten years, there has been a lot of research done on resources for in situ lunar manufacture, and numerous technologies have been suggested.
Ceramic-based items are used to mimic the materials found in distant worlds. During the exploration missions, it will be essential to be able to measure the mechanical-physical characteristics of in situ regoliths and bulk material resources. Currently, getting spare parts to orbit may take years because it is incredibly expensive to carry any equipment from Earth. Fused deposit modeling (FDM) technology adapted for microgravity has partially solved this issue. The technology is, however, exceedingly expensive and not readily accessible for study. Studies on the usage of printed elements in measuring devices and/or equipment meant to measure bulk materials are lacking despite advancements in the field of 3D printing.
About the Study
In this study, the authors discussed the utility of instruments created using the 3D printing technique of material extrusion to test specific mechanical-physical characteristics of bulk materials. The feasibility of measuring the mechanical-physical properties of bulk materials was investigated when printing original or modified measuring devices was not possible. Schulze's ring shear tests, compressibility tests, Freeman's FT4 shear tests, and stability and flow rate tests were carried out using original instruments made of aluminum or steel as well as 3D-printed instruments made of polylactic acid and acrylic styrene acrylonitrile as sample material. The outcomes of tests conducted using both original and printed instruments were compared. The test results indicated that the 3D-printed measuring instruments could be used within a 5% range of measurement error.
The team used fused filament fabrication (FFF) 3D printing technology. Regolith simulant samples were evaluated. The measurements of the mechanical-physical properties of the lunar mare simulant (LMS-1), lunar regolith simulants, and lunar highlands simulant (LHS-1) were presented. These properties included EAIF (δ), compressibility, LAIF (ϕ), ffc, cohesion (c), stability index (SI), basic flowability energy (BFE), and flow rate index (FRI).
The researchers studied the shape and particle size distributions of two lunar regolith powders. Data from 3D-printed instruments made of polylactic acid and acrylic styrene acrylonitrile materials were compared to those from standard measuring devices. Comparisons were made between the values of the EAIF, LAIF, compressibility, ffc, c, SI, FRI, and BFE.
Observations
The 3D printing procedure allowed for the adjustment of surface stiffness and roughness within specific bounds. Tribocharging could also be an important material-specific parameter, influencing the measurement outcomes. When employing PLA-printed instruments, the Schulze's shear cell and lid were 2.5 times lighter as compared to the original measuring tools, and more than three times lighter when using ASA-printed tools. The FT4's vessels were 3D printed with 2.6 times lighter vessel assemblies.
The measuring tools for the 3D-printed FT4 were more than four times lighter than the original measuring tools, and the blade and shear head for the ASA-printed FT4 was more than ten times lighter. FDM printing was more accurate, produced items with greater surface quality, and had superior mechanical qualities than FFF.
The lunar simulant powders were based on the terrestrial environment and imitated particle size distribution, mineralogy, and chemical composition. The blade that was created using FFF technology in 3D printing was not a replica. The blade curvature could not be produced with a precision high enough in the manufacturing process to be geometrically similar. The curved part's surface layering was visible to the naked eye due to the poor surface smoothness. The measured values of the SI and FRI were minimally altered by the smoothing of the blade surface.
The mechanical qualities, ultra-violet (UV) and color resistance, lower density than PLA, and temperature resistance made the ASA filament an excellent choice for the laboratory setting in a harsher environment. In vacuum chambers used for space qualification testing, wear, or radiation, the material could endure thermal cycling. The material was employed in complex mechanical engineering applications as well as the aerospace, oil, and aviation industries. It required fused deposition modeling (FDM) printing technique with nozzle temperatures over 400 °C.
If the shear was not carried out properly in the plane, the flatness of the surface could result in differing compressibility values. When 3D printed containers were utilized, and test energy consumption was increased, the FRI and the SI values remained steady and consistent.
Conclusions
In conclusion, this study determined whether measuring equipment created utilizing the 3D printing technique of material extrusion could be used to assess certain mechanical and physical characteristics of bulk materials under difficult circumstances.
The authors mentioned that mechanical-physical qualities should be measured in places where low weight is crucial, where interchangeable equipment was required to measure approximations, and where a rapid result is more crucial than an exceedingly precise result. They stated that when building tools on-site, 3D printing offers substantially more flexibility than traditional methods of milling steel, etc.
Reference
Divis, J., Hlosta, J., Zurovec, D., et al. 3D printed laboratory equipment to measure bulk materials in extreme conditions. Scientific Reports, 12, 17331 (2022). https://www.nature.com/articles/s41598-022-22114-2
Disclaimer: The views expressed here are those of the author expressed in their private capacity and do not necessarily represent the views of AZoM.com Limited T/A AZoNetwork the owner and operator of this website. This disclaimer forms part of the Terms and conditions of use of this website.