A paper recently published a paper in the journal ACS Energy Letters reviewed the role of isostatic pressing (ISP) in large-scale solid-state battery (SSB) production.
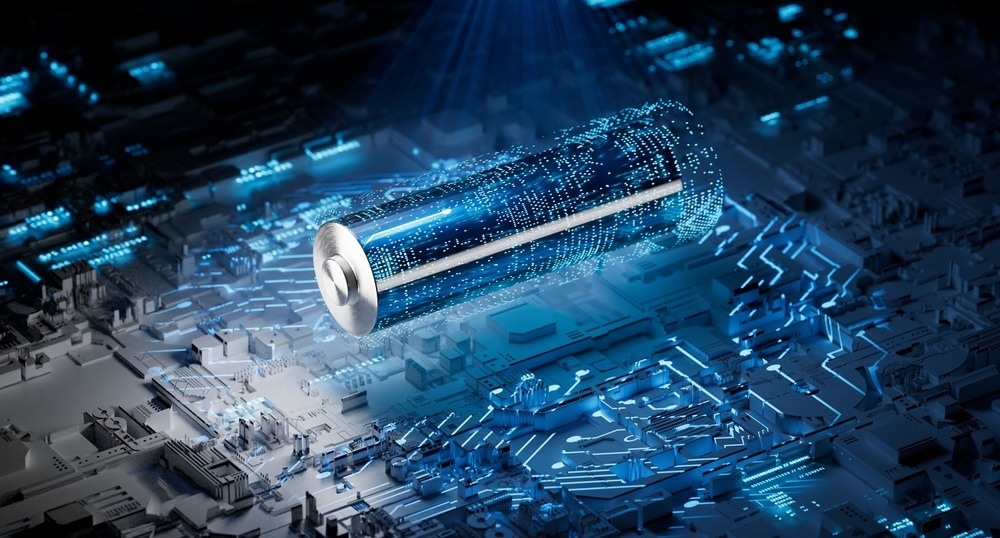
Study: The Role of Isostatic Pressing in Large-Scale Production of Solid-State Batteries. Image Credit: JLStock/Shutterstock.com
Background
SSBs have gained significant attention as a suitable alternative for energy storage applications due to their low cost, high energy density, improved safety, and long cycle life. However, significant processing and material challenges are currently hindering the practical deployment of SSBs.
For instance, the power and energy densities of SSBs are significantly lower compared to lithium-ion batteries. In a complex system such as an SSB, envisioning, developing, and streamlining the production systems that can handle different chemistries, form factors, materials, and processing conditions are increasingly becoming essential.
Scalable processing of thin lithium metal anodes, thick composite electrodes, and thin solid electrolytes and their integration into cell configurations are crucial to enhancing the near-market SSB value proposition.
ISP is a process that covers most of the processing conditions required for the large-scale production of solid electrolyte materials. ISP can be used to generate dense, thin solid electrolyte layers used in practical SSBs. Moreover, the technique offers a pathway toward the integration of the solid electrolyte, anode, and cathode layers into a tri-layer, dense system for commercial applications.
In this paper, the authors reviewed recent studies on SSBs that leveraged ISP techniques and their impact on the electrochemical performance of the systems. The authors also conducted a techno-economic analysis to implement ISP at a commercial scale.
ISP Processing Pathways
ISP can be classified as hot isostatic pressing (HIP), cold isostatic pressing (CIP), and warm isostatic pressing (WIP). The uniformity and density of a sample after an ISP treatment depend on the optimization of process conditions, including pressure, temperature, and time of the ISP cycle.
HIP, WIP, and CIP can be differentiated by their process conditions. CIP can offer up to 600 MPa ISP capabilities depending on the equipment size and design. Liquid composed of an additive, such as oil, and water are often utilized as the pressure medium.
WIP also offers similar pressing capabilities and can be performed in standard CIP vessels. The pressurizing medium is externally heated and then circulated into the pressure vessel. High temperatures up to 150 oC with good temperature uniformity can be achieved using compatible bag material and high-temperature oil.
The pressure medium must be selected carefully in this WIP while handling reactive materials, such as sulfides and lithium, to eliminate potential chemical reactivity. However, lithium metal anodes can be processed using WIP/CIP techniques by properly optimizing the experimental conditions.
Standard HIP equipment offers up to 200 MPa capabilities and high temperatures up to 2000 °C with excellent temperature accuracy and uniformity. Inert argon gas is typically used as a pressure medium to protect the furnace and workpieces from high temperatures during operation.
The processing time in the HIP is significantly higher compared to other ISP processes, requiring several hours in place of minutes, owing to the high compressibility of gas compared to liquid. However, recent developments in vessel cooling and design strategies have allowed uniform rapid cooling (URC), which substantially reduces the processing time.
Application of ISP to SSBs
In SSBs, ISP will be utilized for the compaction of individual components, such as thin solid electrolyte films, and tri-layer anode/solid electrolyte/cathode cell assemblies to enable enhanced performance. The batch processing of stacked solid electrolyte sheets or film wound spools can be performed using ISP to fabricate the dense thin films.
Although pouch cells, cylindrical cells, and tri-layer assemblies are compatible with ISP treatment, cylindrical cells are preferred over other geometries for ISP to ensure pressure uniformity across the surface sample and achieve a higher container volume packing fraction to realize a higher throughput.
ISP treatment allows the consolidation of internal defects and voids for maximum density and uniformity, achieving close contact between particles without any geometrical limitation while preserving the sample shape. Moreover, ISP allows the fabrication of larger components, offers superior material properties, and increases the length-diameter ratios.
Critical Evaluation of ISP Implementation in SSBs
The application of ISP in the field of SSB has been limited until now. Most studies used an average of 200-250 MPa ISP for solid electrolyte material in the CIP cycle. However, the ISP process conditions were typically un-optimized, and the selection of the 200-250 MPa processing pressure was arbitrary in nature.
WIP has not been used for solid electrolyte densification in previous studies, while HIP treatment was used in a limited number of studies. The solid electrolyte phase purity remains unaffected by all ISP treatments, including HIP treatment.
During sintering, the need for mother powder that currently accounts for a considerable amount of material waste for lithium lanthanum zirconium oxide (LLZO) material processing can be eliminated or minimized by tuning the processing conditions using garnets.
The opaque pellets become translucent after HIP treatment, indicating high densities and larger grain sizes that lead to improved electrochemical and transport properties. Moreover, grain growth during the ISP treatment can lead to specific preferred orientations.
Cathode particles with crystallographic orientations demonstrate better performance compared to the polycrystalline alternatives in SSBs. Thus, the ability of ISP to grow and control preferred orientations during the integration/sintering process can significantly improve the SSB performance and facilitate the development of high-performance battery systems.
Although the solid electrolyte densification work using ISP is often performed for sodium superionic conductor (NASICON) or garnet-type crystalline materials, the use of these densification strategies for softer electrolytes, such as argyrodites and sulfide, will also be beneficial.
For instance, WIP and CIP processing used on anti-perovskite solid electrolyte materials significantly improved the density and porosity of the materials. Additionally, the use of WIP led to the formation of small rod-like crystals.
Thus, the application of ISP to soft solid electrolyte materials can allow the processing of these materials with a greater degree of local microstructural control, which is essential for producing durable SSBs.
The ISP densification mechanism heavily relies on material properties, which necessitates careful optimization of pressure-temperature-time correlation for every material system.
A few studies also demonstrated that the mechanical properties of solid electrolytes improved after ISP treatment. For instance, HIP-processed lithium lanthanum titanate (LLTO) displayed a 223 MPa average Young’s modulus compared to 192 MPa obtained using traditional sintering approaches. More research is required to assess the effect of ISP processing conditions on the solid electrolyte surface to design resilient interfaces for SSBs.
The use of ISP treatment for the densification of NASICON and garnet-type materials increased their conductivity. However, a large variance was observed in ionic conductivity values even within the same materials due to the lack of process optimization of the HIP and CIP processes. Additionally, the inherent defect chemistry and crystal structure also affect the conductivity of a solid electrolyte.
Eight-five to one hundred percent pellet densities were realized using ISP techniques for several processing pressures. Moreover, different solid electrolyte|electrode assemblies/cells integrated using an ISP treatment, such as HIP or CIP, demonstrated an improved interfacial contact between the electrode and electrolyte interfaces.
Thus, the cells demonstrated a higher discharge capacity that is similar to the capacity of the practical liquid electrolyte-based cells. Moreover, no secondary phase is generated by ISP processes, indicating minimal reactivity between the electrode and electrolyte due to high pressures. Moreover, SSB symmetric cells and full cells integrated using ISP treatments showed exceptional cycling stability, with several cells displaying stability up to 1000 cycles.
Among the ISP techniques, WIP is the most suitable to improve the layer density, lithium deposition uniformity, solid electrolyte structural integrity, and cathode|solid electrolyte interfacial adhesion.
Techno-Economic Analysis for Large-scale SSB Production using the ISP Processes
The authors conducted a techno-economic analysis of the ISP processing costs for large-scale SSB manufacturing. They assumed that all electric vehicles in the next two decades, which is almost 50 million based on different projections, will be built using SSB packs.
The required solid electrolyte and tri-layer cell volume were projected assuming a pack and cell configuration composed of 500 μm cell thickness, 75 μm solid electrolyte thickness, 0.2 N/P ratios, and four mAh cm−2 cathode loading.
Cylindrical form factors were preferred over planar configurations, while solid electrolyte film rolls and/or tri-layer films were used during ISP processing. ISP was used in two separate stages of the SSB manufacturing process, including tri-layer cell integration and solid electrolyte laminate formation.
Based on the analysis, the author predicted the need for 8−15 HIP/WIP/CIP units for handling the cell integration and solid electrolyte processing, and the ISP running cost for cell integration will be $1−20K/GWh depending on the ISP technique used for processing. These results provide an early estimate of the processing costs to meet the future demand for SSBs in electric vehicles.
Conclusion
An optimized ISP process can play a crucial role as a durable and high-performance SSB cell and component fabrication tool. However, more research is required to address the existing challenges in ISP implementation in SSB manufacturing. Specifically, the ISP technique must be optimized for SSB cells and components to improve SSB performance and realize large-scale production.
More from AZoM: How are Graphene Batteries Made?
Disclaimer: The views expressed here are those of the author expressed in their private capacity and do not necessarily represent the views of AZoM.com Limited T/A AZoNetwork the owner and operator of this website. This disclaimer forms part of the Terms and conditions of use of this website.
Source:
Balasubramanian, M., Muralidharan, N., Dixit, M. et al. The Role of Isostatic Pressing in Large-Scale Production of Solid-State Batteries. ACS Energy Letters 2022. https://pubs.acs.org/doi/10.1021/acsenergylett.2c01936