Creep can happen when a metal is strained much below its yield strength at high temperatures. Creep, or time-dependent material deformation, accounts for a large percentage of component failures at high temperatures.
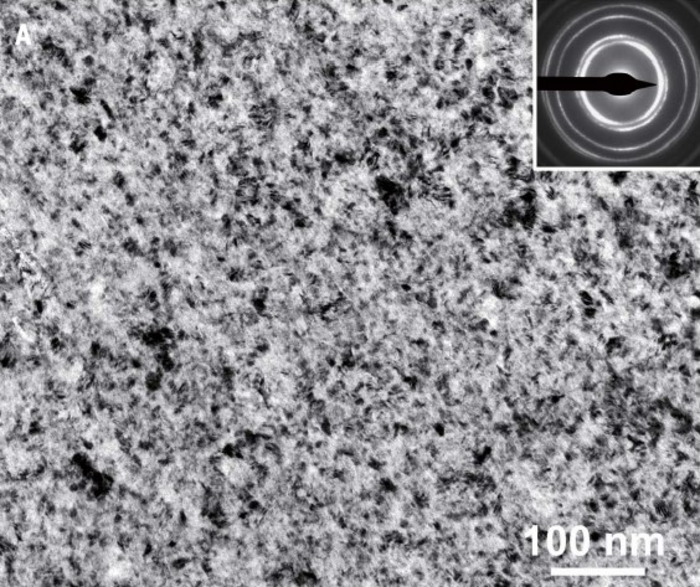
A bright-field TEM image showing extremely fine grains. Image Credit: Institute of Metal Research
Scientists know that removing grain boundaries in materials can help metals withstand high-temperature creep. A group of scientists, however, has found an alternative technique for preventing creep by utilizing stable grain boundary networks.
On November 10th, 2022, the study was published in the journal Science.
The team’s approach to property enhancement differed greatly from typical strategies.
The behaviors of grain boundary networks may be fundamentally alerted when structural relaxation of grain boundaries is triggered through their interaction with partial dislocations below a critical grain size.
Xiuyan Li, Professor, Institute of Metal Research, Chinese Academy of Sciences
The scientists got an unparalleled creep resistance that excelled that of typical superalloys using their unique method.
Creep is an expensive issue. A large proportion of material and component failures at high temperatures are ascribed to creep or its interaction with other degradation processes. The repair and replacement of parts in modern devices cost billions of dollars each year.
In the chemical industry, there is an increasing need for higher fuel efficacy and more reliable nuclear reactors, turbines, and devices. Owing to this increasing demand, there is a growing necessity for enhanced high-temperature creep resistance in advanced alloys.
Traditional development of alloys for high-temperature applications is primarily relying on the skillful addition of various alloying elements for strengthening the matrix or interfaces, or for forming reinforcing precipitates. Such a strategy is facing a dilemma of limited property improvement with intensifying alloying and elevated cost.
Xiuyan Li, Professor, Institute of Metal Research, Chinese Academy of Sciences
Grain boundaries, which are crystal structure defects, are the interfaces where two crystals with different orientations meet. Although conventional wisdom suggests removing grain boundaries to combat creep, the investigators advocated adding plentiful grain boundaries to construct stable grain boundary networks in metal to restrict creep while inhibiting atomic diffusion and hardening at high temperatures.
Recent work on grain boundary relaxation in metals influenced the decision to use this method.
The researchers discovered that grain boundaries can be employed to strengthen alloys at high temperatures, contrary to popular belief that they always damage alloys at high temperatures. Grain boundaries in metals and alloys are recognized to be a “weak component,” as they can move or slide when loaded at high temperatures.
We found that grain boundaries in the nanograined single-phased alloy can be effectively stabilized through a structural relaxation, and the creep performance of the alloy are significantly enhanced at elevated temperatures.
Xiuyan Li, Professor, Institute of Metal Research, Chinese Academy of Sciences
Unlike conventional alloying techniques, grain boundary relaxation provides an innovative and sustainable way to improve the characteristics and performance of alloys for high-temperature applications.
In terms of future study, the team believes that altering grain boundary networks in metals and alloys has the potential to improve stability.
Li says, “Therefore, the next step of this study is to extend this principle to other engineering alloy families for high-temperature applications, including nickel-based alloys and steels.”
The group intends to conduct processing development to further increase grain boundary network stability and to create large-size samples for testing additional attributes and performance at high temperatures.
Li concludes, “Ultimately we hope to realize industrial applications of the high-performance engineering alloys with stable grain boundary networks.”
B. B. Zhang and LI Xiuyan from the Shenyang National Laboratory for Materials Science (SYNL), Institute of Metal Research, Chinese Academy of Sciences; Y. G. Tang from the Institute of Metal Research, Chinese Academy of Sciences and the School of Materials Science and Engineering, University of Science and Technology of China contributed to the study.
The team also included Q. S. Mei from the School of Power and Mechanical Engineering, Wuhan University; and K. Lu from the SYNL, Institute of Metal Research, Chinese Academy of Sciences, and the Liaoning Academy of Materials.
The study was financially supported by the Ministry of Science and Technology of China, the National Natural Science Foundation of China, and the Chinese Academy of Sciences.