A metal rolling mill in Northern Europe has improved its productivity, ensuring it can maximize the production of high-quality, recycled stainless steel.

Image Credit: ABB Measurement & Analytics
Maximizing production of a totally recyclable material
As the world seeks to reduce energy consumption and pollution, one focus is on the metal industry, a large consumer of power. Ideally, metals should be as recyclable as possible, to reduce the cost and energy involved in extracting, transporting and processing raw materials.
One such metal is stainless steel. As well as having a long life due to its corrosion resistant properties, it also theoretically 100 percent recyclable. It also contributes to protecting the environment in other ways, being used in diesel filters, efficient boilers, solar panels and fuel cells.
An ABB measurement solution has helped one stainless steel plant maximize its production of this material. The integrated site includes a melt shop, a hot rolling mill and several cold rolling mills. The plant uses up to 80 percent recycled steel content to form its stainless steel product.
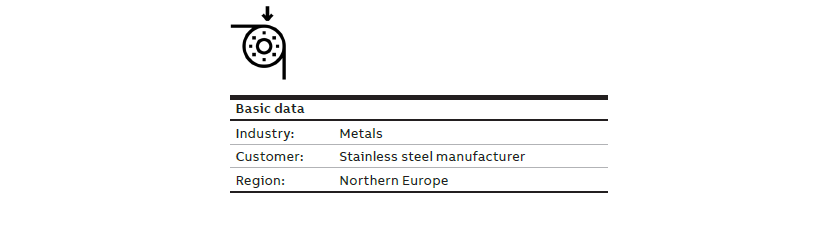
Image Credit: ABB Measurement & Analytics
Improved flatness measurement upgrades rolling mills
A steel plant in Northern Europe has modernized production by making upgrades to the Sendzimir cluster mills.
Commissioned in the 1970s, the number one 20-high Sendzimir cluster mill has been a reliable production tool at the steel plant. The plant has recently modernized its production technology by upgrading the ABB Stressometer flatness measurement and control systems.
The plant produces 100 percent recyclable stainless steel coils that are ideal for a wide variety of applications and is produced using the most advanced technologies and to the strictest quality requirements. It is available in a range of corrosion and heat resistant grades to offer a high-strength, corrosion-resistant material that is lightweight and highly workable.
The integrated site includes a melt shop, a hot rolling mill and several cold rolling mills. The most significant raw material is recycled steel, and the recycled content in ready-made production is more that 80 percent on average. The steel plant provides coils in widths of up to two meters and thickness range from 0.3 mm to 3.5 mm.
The plant’s state-of-the-art melt shop ensures superior control of the product composition, the structure, and the inclusion pattern to produce extremely clean steel. Computerized process control of the rolling mills, heat treatment facilities, and finishing lines ensures consistency and superior control of the targeted properties to ensure that customers get exactly the product they need. Typical applications of stainless steel coil and sheet include the process industry, consumer goods, marine environments and high-end construction.
By upgrading the flatness systems’ electronics and by adding ABB’s patented Extended Singular Value Decomposition system (ESVD), the enhanced flatness control has improved the operational reliability and performance of the rolling mills significantly.
The system controls the actuators in the cold rolling mills, producing the highest quality stainless steel coils. The upgrades have increased productivity by 5 percent, while continuing to use the existing measuring rolls. The most important benefit of the Stressometer flatness control system is improved quality.
Image Credit: ABB Measurement & Analytics
Productivity has reached its highest-ever level
The management and the production team at the steel plant have already noticed significant improvements since the control system was installed. The rolling mill manager and the foreman at the mill are both satisfied with the results achieved.
“Production has been running very well since the installation of the Stressometer ESVD and estimated production is up by approximately 5 percent per year,” says the cold mill manager. “The cluster mills are running perfectly for all coils in fully automatic flatness control at maximum speed. Productivity has now reached its highest-ever level.”
The number of strip breaks has been reduced
Operators at the plant know they can rely on the fully automatic Stressometer flatness control system to handle all rolling conditions. An operator stated, “I trust the automatic flatness control more than I trust myself.”
According to the foreman, the operational reliability is one of the main reasons for the improvement in quality and the reduced number of strip breaks. “The operators do not need to make unnecessary checks after the installation of the Stressometer ESVD. There has been a significant improvement in availability since the upgrades of the systems. The number of strip breaks has been reduced, and today we do not have any flatness-related strip breaks,” says the foreman. This saves a lot of time and provides greater opportunities for process optimization.
The reliability was further explained by the rolling mill manager: “The actuators never go to their limit positions with ESVD, which is a big improvement. Thanks to ESVD we no longer have to put the system into manual mode. The ABB flatness control system always adjusts the actuators to their optimum position,” he says.
Image Credit: ABB Measurement & Analytics
ABB solutions used at the plant
ABB solution
At the plant ABB has installed the following systems:
• Four Stressometer flatness control systems (three 20-high mills with ESVD)
• Three Millmate Strip Scanner systems
• Thirty-two Millmate Strip Tension systems
• Several Millmate Roll Force systems
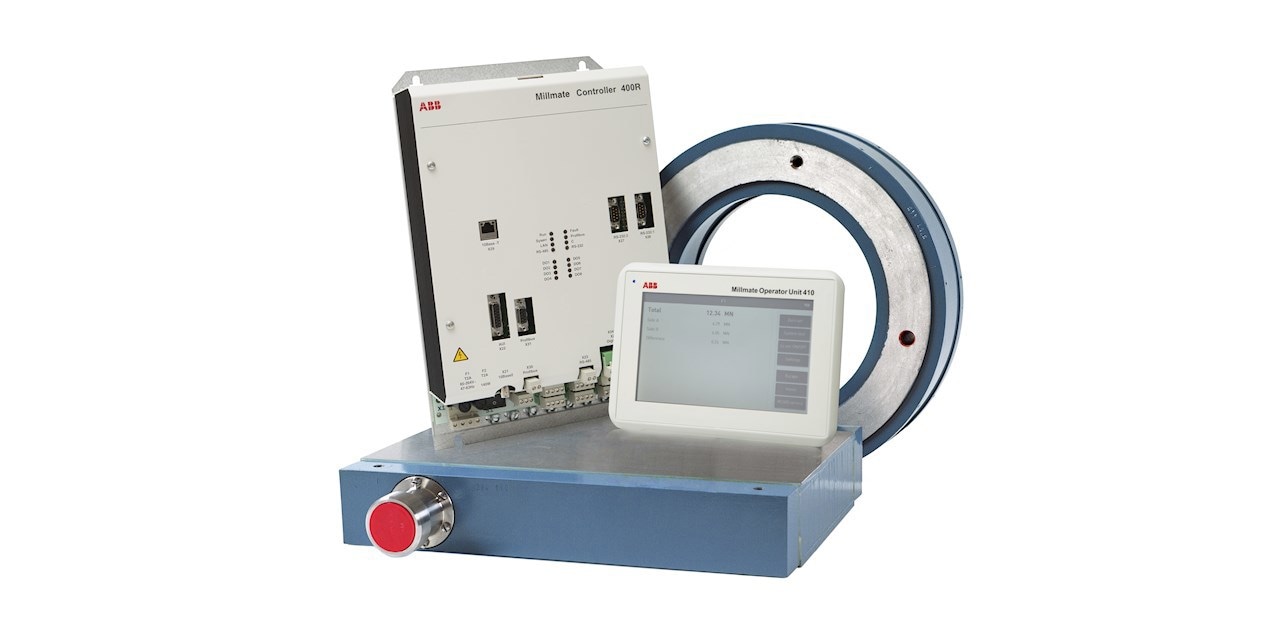
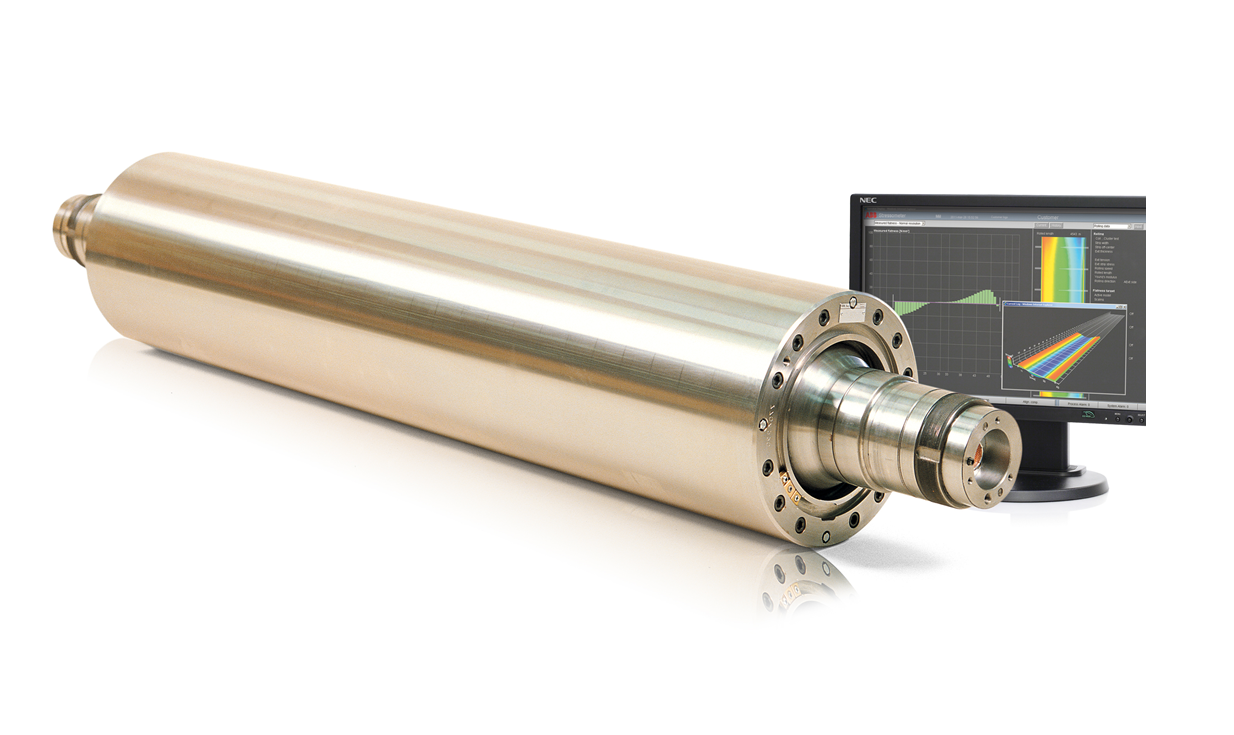
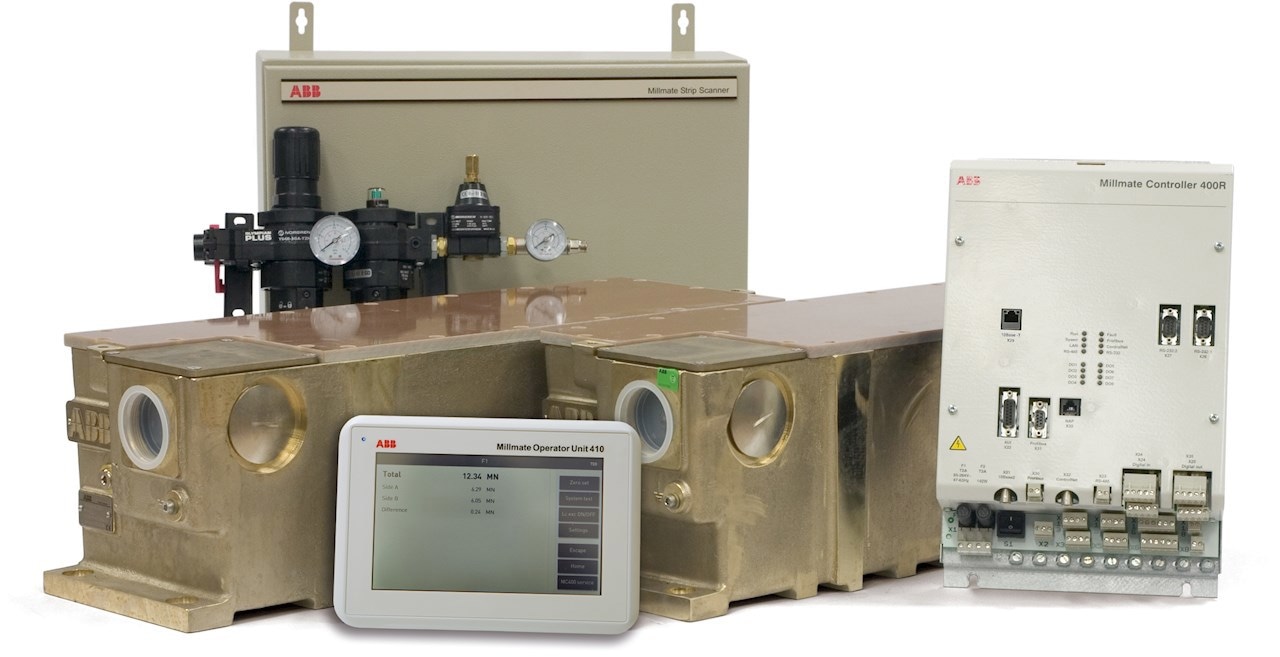
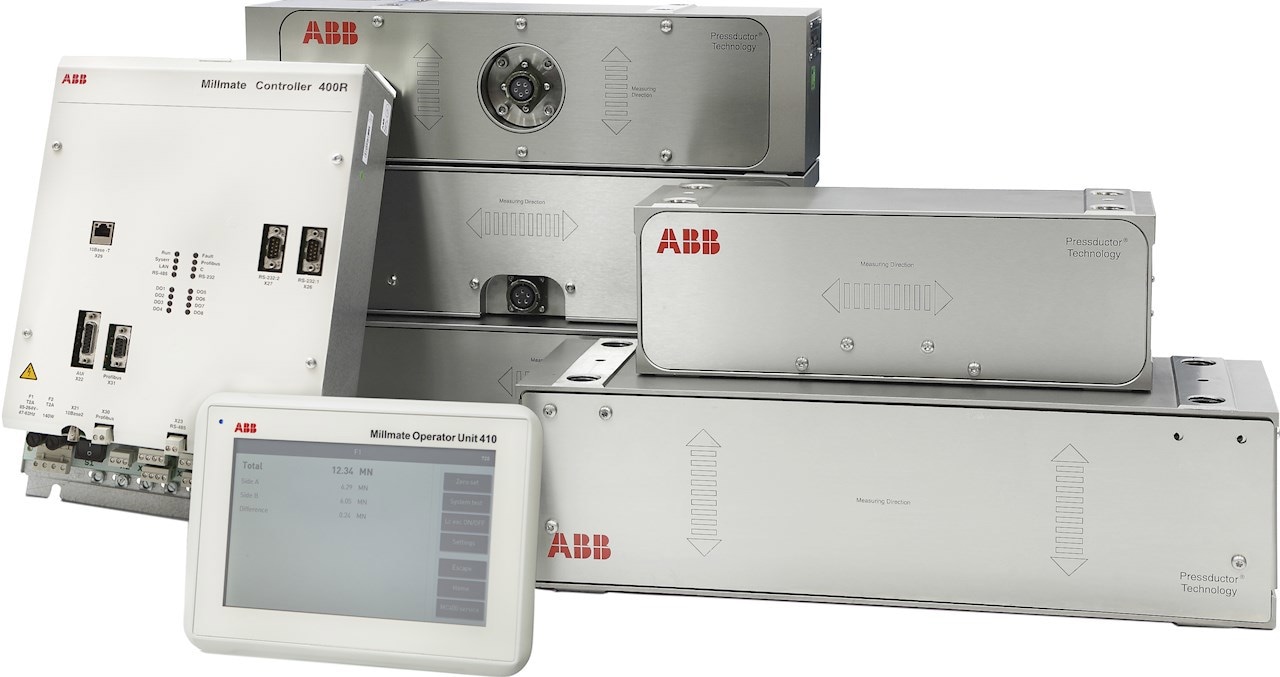
Image Credit: ABB Measurement & Analytics