It is a lot safer if the face mask fits, state Flinders University medical specialists, after coming up with a cost-efficient method to tailor N95 filtering face-piece respirators (FFRs) for health workers who are on the front line of the pandemic and respiratory viruses like influenza.
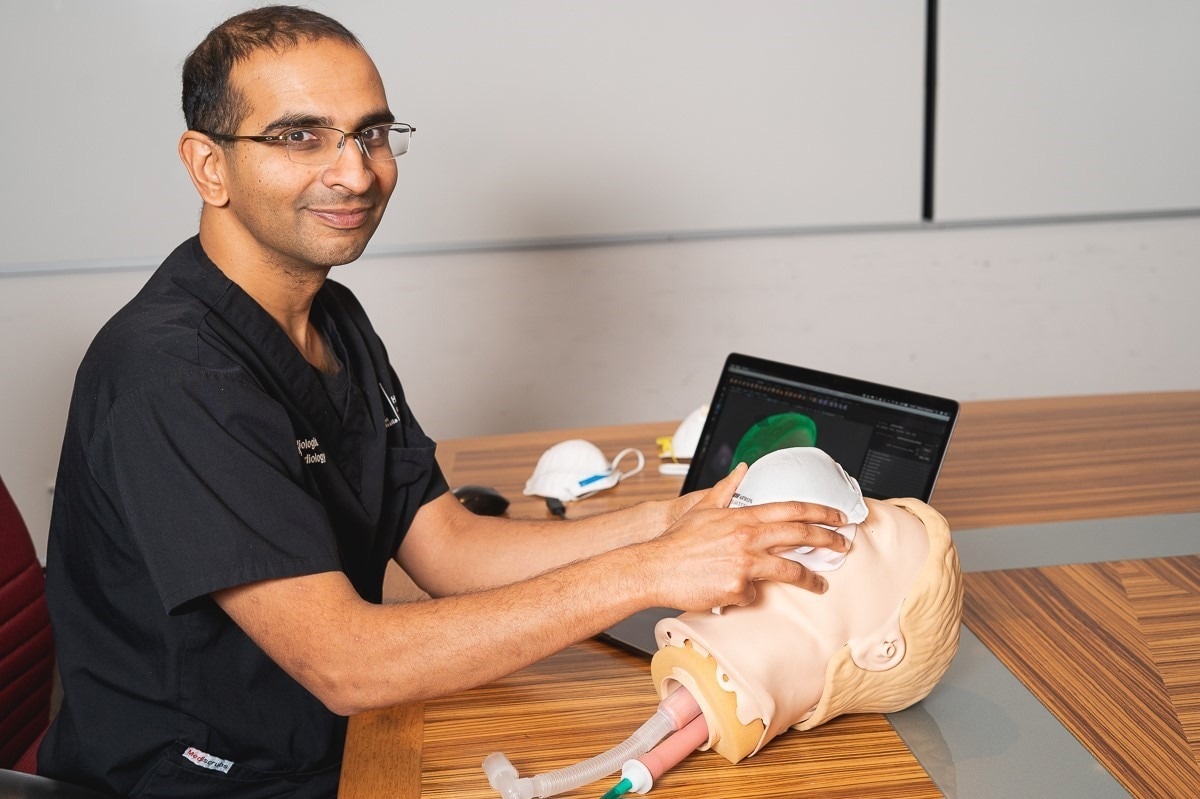
Professor Anand Ganesan working on the 3D facial modeling technology. Image Credit: Flinders University
Scientists state that the reduction in “leakage” and larger comfort for the wearer whose face has been personally fitted can also enhance respirator and mask safety in a broad range of industrial settings in health care and beyond.
Individually and anatomically personalized 3D-printed face frames represent a rapidly scalable technology to significantly improve health care worker protection and comfort, and fit-testing pass rates.
Darius Chapman, Cardiology Research Fellow, Flinders University
Working with public hospital workers at the time of the COVID-19 pandemic, Mr. Chapman, with clinician and cardiac electrophysiology scientist at Flinders, Professor Anand Ganesan, headed the project to compare the performance of customized 3D printed frames to enhance N95 FFRs test scores in association with regular respirators.
They employed a mobile iPhone camera and an app to generate 3D scans of the faces of volunteers. These scans were then fed into a software program to characterize every user’s facial features and structure to scale.
A plastic and then silicone-coated frame was then built using a commercially available 3D printer from those individual facial impressions or virtual scaffolds.
“Overall, the quantitative fit testing significantly improved, as did the respirator comfort and tolerability factor,” adds Mr Chapman.
“With further refinement, this system could considerably advance the correct fitting of N95 and other FFRs, which have become increasingly important in our health care systems during the pandemic. The ability to generate the low-cost 3D-printed mesh from a readily available mobile device technology means that individual face scans can be easily and cost-effectively generated around the world in any location.”
A proposed workflow for this technology could involve the scans being sent direct to fabrication centers which could be located at a distance from hospitals or other health facilities. Further, using readily available consumer-grade 3D printers and materials at low cost could be an important practical advance to decreasing leakage from N95 FFRs in workers as well as other people at high risk of severe outcomes from respiratory virus, like immunocompromised people.
Professor Anand Ganesan, Flinders University
Journal Reference
Chapman, D., et al. (2023) Personalized 3D-printed frames to reduce leak from N95 filtering facepiece respirators: a prospective crossover trial in health care workers. Journal of Occupational and Environmental Hygiene. doi.org/10.1080/15459624.2023.2205471.