TANAKA Kikinzoku Kogyo K.K. (Head office: Chiyoda-ku, Tokyo; CEO: Koichiro Tanaka), which develops industrial precious metals products as one of the core companies of TANAKA Precious Metals, announced today that it has established a gold particle bonding technology for high-density mounting of semiconductors using AuRoFUSE™ low-temperature fired paste for gold-to-gold bonding.
Figure 1. Comparison of AuRoFUSE™ preforms and other materials. Image Credit: TANAKA Precious Metals
AuRoFUSE™ is a composition of submicron-sized gold particles and a solvent that creates a bonding material with low electrical resistance and high thermal conductivity to achieve metal bonding at low temperatures. Using AuRoFUSE™ preforms (dried paste forms), this technology can reach 4 μm fine-pitch mounting with 20 μm bumps. Formed through a thermocompression bonding process (20 MPa at 200 °C for 10 seconds), AuRoFUSE™ preforms exhibit compression of approximately 10% in the compressive direction while showing minimal deformation in the horizontal direction. This gives them sufficient bonding strength for practical applications, making them suitable for use as gold bumps . With the main component being gold, which has a high level of chemical stability, AuRoFUSE™ preforms also provide excellent reliability after mounting.
This technology enables miniaturization of semiconductor wiring and greater integration (higher density) for various types of chips. It is expected to contribute to the high-level technical innovation required of advanced technologies, including optical devices such as light-emitting diodes (LEDs) and semiconductor lasers (LDs), and use in digital devices such as personal computers, smartphones, and in-vehicle components.
TANAKA will actively distribute samples of this technology in the future to promote greater awareness in the marketplace.
TANAKA will present this technology at the 38th Spring Conference of the Japan Institute of Electronics Packaging to be held from March 13 to 15, 2024, at the Tokyo University of Science.
Manufacturing of AuRoFUSE™ Preforms
- Au/Pt/Ti metallization of the bonding substrate to form the base layer
- Photoresist applied to the bonding substrate after metallization
- Exposure/development by holding the photomask, corresponding to the preform shape, over the bonding substrate to form a resist frame
- Flowing of AuRoFUSE™ into the formed resist frame
- Vacuum drying at room temperature, followed by scraping off excess gold particles with a squeegee
- Temporary sintering through heating, followed by separation and removal of the resist frame AuRoFUSE™ preform array (example) AuRoFUSE™ preform lateral SEM image
Achieving High-Density Mounting with AuRoFUSE™ Preforms
Depending on the purpose, various bonding methods are used for mounting semiconductor devices, including solder and plating methods. The solder-based bonding method is a low-cost, speedy method of producing bumps, but because solder tends to spread outward when melted, there are concerns about possible short-circuiting through contact between electrodes as the bump pitch becomes finer. In the development of technologies for high-density mounting, electroless plating is becoming mainstream for producing copper and gold plating bumps. This method can achieve a fine pitch, but because comparatively higher pressures are required during bonding, there are concerns about possible chip damage.
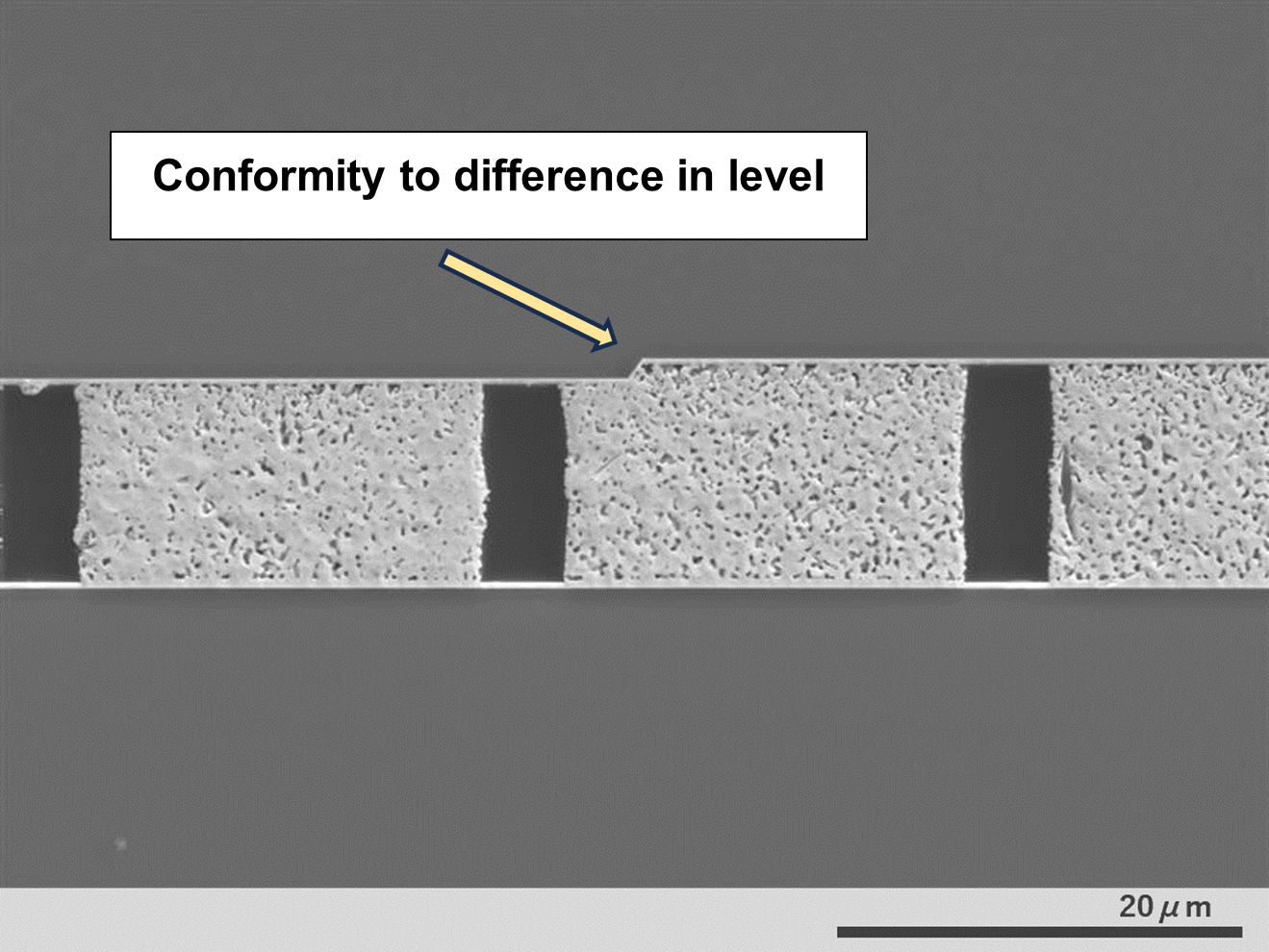
Figure 2. AuRoFUSE™ preform SEM image showing absorption of unevenness during bonding. Image Credit: TANAKA Precious Metals
As precious metals professionals, TANAKA Kikinzoku Kogyo has been conducting research and development into the use of AuRoFUSE™, which enables low-temperature, low-pressure bonding with followability of uneven surfaces due to its porousness, to achieve high-density mounting of semiconductors. The company initially attempted to use the mainstream application methods of dispensing , pin transfer , and screen printing , but the fluidity of the paste made those methods unsuitable for high-density mounting. Using this new technology, the paste is dried prior to bonding to eliminate fluidity, which minimizes spread and enables high-density mounting (Figure 1). The porous structure of the paste makes it easily formable as well, which enables bonding even when there is a difference in height between electrodes or differences in warpage or thickness of the substrate (Figure 2).