A recent review article published in the Journal of Magnesium and Alloys explored the influence of cooling rate on the microstructure and properties of magnesium alloy, analyzing the observed deviations in detail.
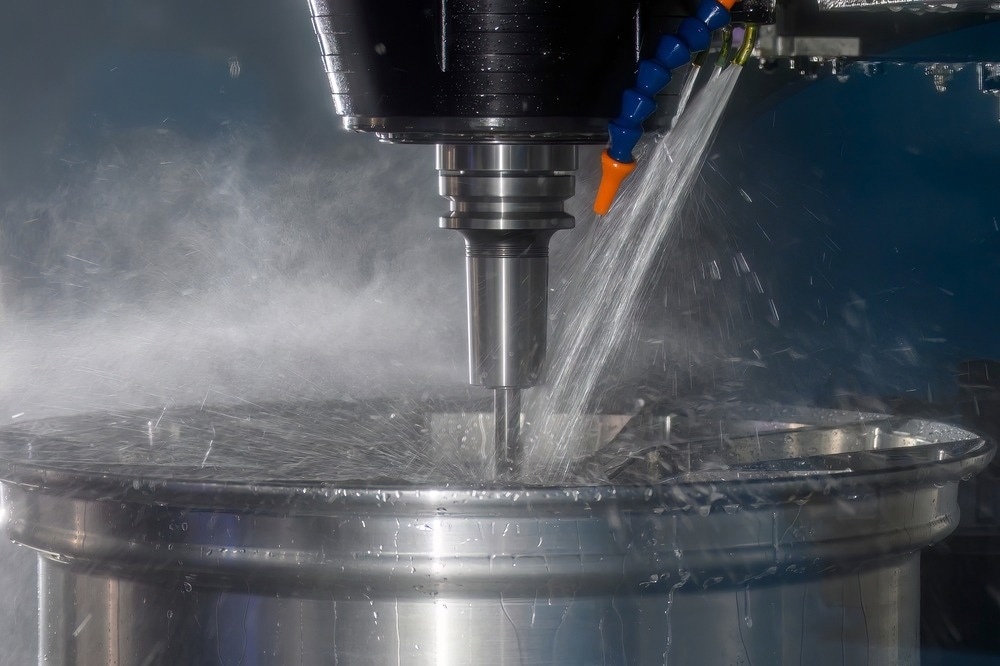
Image Credit: Pixel B/Shutterstock.com
Methods of Obtaining Different Cooling Rates
Different methods are employed to vary cooling rates for magnesium alloys during the solidification process from liquid to solid phase and after the solution/aging heat treatment. These include using wedge-shaped molds, casting molds with different diameters, step-shaped molds, and die-casting molds with diverse thicknesses.
Additionally, molds of different materials, such as sand, graphite, steel, and copper, exhibit different cooling rates.
The cooling environment, such as furnaces, air, water, and using chill blocks at the ends of castings, also influences the cooling of alloys. For instance, rapid solidification technology provides speedy cooling rates, primarily through casting methods such as spray deposition, single-roller rapid solidification, water-cooled copper mold spray casting, and laser rapid solidification.
Effects on Solidification Behavior
The cooling rate affects the solidification of magnesium alloys from liquid to solid phase, thereby affecting the microstructure and properties of the alloy. In the case of Mg-10Gd-3Y-0.4Zr alloy, a higher cooling rate advances the crystallization or nucleation process by promoting the formation of more embryos in the alloy melt. With an increase in the cooling rate, the overall solidification time of the alloy is gradually shortened.
Furthermore, apparent viscosity gradually increases with the decreasing temperature due to the increase of solid fraction. Thus, under continuous cooling conditions, an increasing cooling rate does not allow the transformation of solid phase particle shape to globular, affecting the morphology of the alloy.
The cooling rate also influences the hot tearing susceptibility of magnesium alloy, which is related to dendritic coherence solid fraction. A greater solid fraction results in a lesser liquid in interdendritic regions and, consequently, lower stresses in the solid network. Thus, the hot tearing susceptibility first decreases and then increases with the increase in cooling rate.
Effects on Microstructure
The preparation process parameters of magnesium alloys govern their microstructures. The as-cast microstructure of magnesium alloy changes with variations in cooling rate due to changes in the solidification behavior.
More solute elements are dissolved into the α-Mg matrix when the alloy solidifies at a faster cooling rate, increasing the solid solution of the alloying elements in the magnesium matrix. This influences the alloy’s phase composition, size, content, and distribution. Additionally, amorphous, metastable, and quasi-crystalline phases might form in the alloy, especially due to rapid solidification.
Generally, magnesium alloys exhibit lower grain sizes and are coarsened with increasing cooling rates. This is attributed to the reduction in the size of the constitutional undercooling zone and suppressed diffusion of solute atoms at a faster cooling rate.
Post-Heat Treatment Effects
The cooling rate of magnesium alloy after solution or heat treatment affects the solid solution of alloying elements in the magnesium matrix and the precipitate content, size, and distribution. The larger amounts of alloying elements obtained with a faster cooling rate after solution treatment result in more precipitates with smaller sizes.
Possible local remelting during the heat treatment directly affects the redistribution of alloying elements during subsequent cooling. The significant temperature gradient between the surface and core of the alloy during cooling can also result in a differential stress distribution in the alloy.
While a lower quenching cooling rate exhibits little effect on grain size, it can cause twinning to disappear, increase precipitates, weaken texture, and make the alloy brittle after aging. Notably, the residual stress in an alloy after air cooling is close to zero.
Effects on Properties
The varying microstructure of magnesium alloys with cooling rates directly determines their mechanical properties, corrosion resistance, and oxidation resistance. Fine grain strengthening, solid solution strengthening, and precipitation strengthening due to an increasing cooling rate improve the mechanical properties of magnesium alloys.
Additionally, the uniform microstructure and chemical composition of alloys due to higher cooling rates can decrease the activity and probability of local micro-galvanic corrosion. Solidification at faster cooling rates forms a denser protective film on the alloy surface, further improving its corrosion resistance.
According to the oxidation kinetics of magnesium alloys, a thick oxide film with wrinkles, nodules, and cracks (slow cooling rate) can degrade their oxidation resistance. Alternatively, a thin and dense oxide film (fast cooling rate) enhances the oxidation resistance of magnesium alloys.
Conclusion
This review article comprehensively illustrated the impact of cooling rate during solidification and post-heat treatment of the microstructure and properties of magnesium alloys. However, the experimental trends observed in a certain cooling rate range might not apply to other ranges.
Thus, the authors suggest using computational methods like molecular dynamics and first principle calculations to reveal the internal mechanisms impacting the microstructure and properties of magnesium alloys with varying cooling rates.
Journal Reference
Cai, H., et al. (2024). Effects of cooling rate on the microstructure and properties of magnesium alloy-a review. Journal of Magnesium and Alloys. DOI: 10.1016/j.jma.2024.06.02
Disclaimer: The views expressed here are those of the author expressed in their private capacity and do not necessarily represent the views of AZoM.com Limited T/A AZoNetwork the owner and operator of this website. This disclaimer forms part of the Terms and conditions of use of this website.