A recent article published in Giant proposed introducing dynamic boronic ester bonds into liquid crystal elastomers (LCEs) to make them reprogrammable. The effects of printing parameters and boronic bond content on the actuation and re-programmability of LCEs were experimentally investigated.
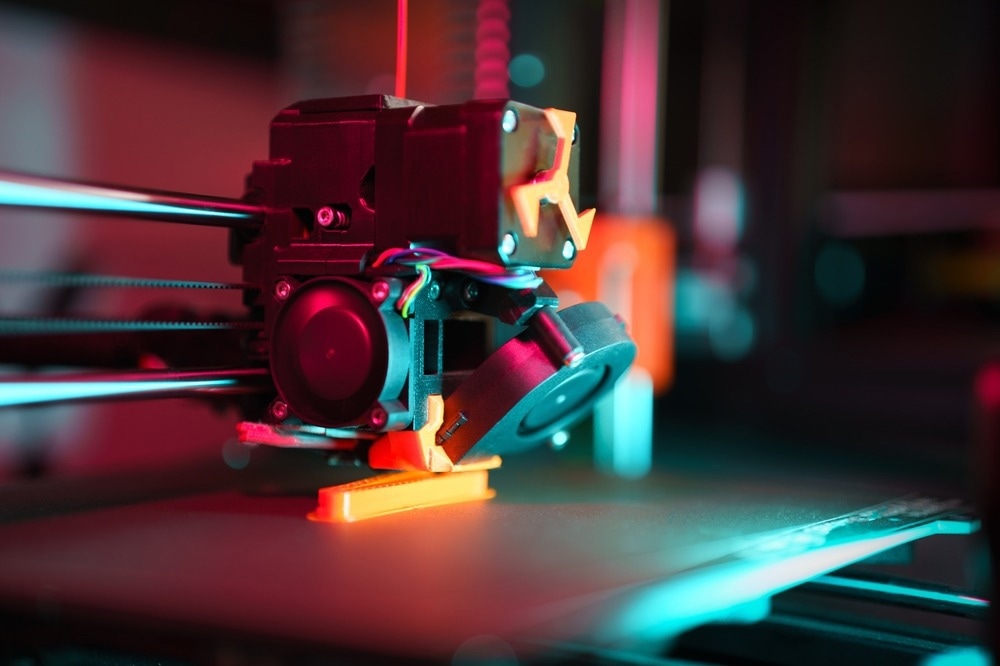
Image Credit: Jakub Zerdzicki/Shutterstock.com
Background
LCEs are soft actuating materials with large and reversible anisotropic deformation ability under cyclic heating and cooling. This deformability acts as a “motor,” enabling complex deformations and driving the locomotion of soft robots. LCEs comprise crosslinked polymer networks (elastic) integrated with liquid crystal mesogens (anisotropic).
Three-dimensional (3D) structure and alignment patterns of mesogens govern the deformation of LCEs. LCEs crosslinked in the macroscopic aligned mesogen state are called monodomain LCEs. Alternatively, polydomain LCEs with random mesogen alignment do not exhibit macroscopic deformation in response to external stimuli.
Different methods are employed to fabricate LCEs with desired shapes and mesogen alignments. However, traditional 3D-printed LCEs require continuous thermal energy input to maintain their actuated shapes. Once cured, they cannot be reprocessed and reprogrammed.
The study introduced dynamic boronic ester bonds into the LCE ink to print structures reprogrammable from polydomain into monodomain state and vice versa by applying external force under elevated temperatures.
Methods
Firstly, 2,2′-(1,4-phenylene)-bis[4-mercaptan-1,3,2-dioxaborolane] (BDB) was synthesized using benzene-1,4-diboronic acid as a source of ester bonds. Subsequently, LCE ink with boronic ester bonds was prepared using BDB in different molar ratios of 20 %, 35 %, and 50 % (denoted as LCE-20, LCE-35, and LCE-50, respectively).
LCE ink with boronic ester bonds was 3D printed by varying printing and curing conditions under 365 nm ultraviolet (UV) light. The printed LCE filaments were additionally cured under 365 nm UV light for 30 minutes.
The printed LCE samples were characterized by 1H nuclear magnetic resonance (NMR) and Fourier-transformed infrared (FTIR) spectroscopy measurements. Differential scanning calorimetry (DSC) and thermogravimetric analysis (TGA) were performed from -50 to 180 °C and 35 to 800 °C, respectively.
The rheological characterization of LCE ink was performed to determine viscosities at different temperatures. Additionally, printed specimens were analyzed using polarized optical microscopy (POM) and wide-angle X-ray scattering (WAXS).
The printed LCE sheets were tested for temperature-dependent stress relaxation, measuring actuation strain and tensile strength under repeated heating and cooling cycles. Adhesion between two printed layers was also measured by the tensile testing method.
Finally, finite element simulations of the deformation of 3D-printed LCE structures were performed on the commercial software COMSOL.
Results and Discussion
The incorporation of BDB made LCEs capable of undergoing bond exchange reactions and rearranging the polymer network when heated above the reaction temperature. Thus, printed LCE structures could switch between monodomain (transparent) and polydomain in response to external heating and loading.
The actuation performance of printed LCE structure could be precisely adjusted by varying printing parameters such as the nozzle’s inner diameter (d), printing temperature (T), and distance between the nozzle and substrate (h).
The LCE specimen became opaque with increasing T, indicating poorer mesogen alignment. In contrast, it became more transparent with decreasing d and h, indicating better mesogen alignment due to increased shearing force.
The measured actuation strain of printed LCE sheets under heating and cooling cycles was also consistent with their appearance. A larger actuation strain was observed for LCE sheets with higher transparency.
The LCE-20 specimen exhibited exceptional reversible actuation behavior maintained after 20 cycles. However, it remained in the monodomain state after exposing to 160 °C for 12 hours, indicating its poor polymer network rearrangement ability.
The LCE-35 specimen contracted upon heating and reached equilibrium at 100 °C. Moreover, its actuation performance could be cycled between 25 and 100 °C at least 20 times without actuation strain loss.
LCE-35 was used for re-programmability assessments by creating active hybrid structures (polydomain cones) at optimized printing parameters. The conical LCE switched between transparent and opaque appearance upon cyclic heating and cooling without mechanical deformation.
Furthermore, the fabricated LCEs could be reprogrammed into an actuated state under external forces, demonstrated using reversible deformation of four-prism structures compressed under 5 kg weight and placed at 160 °C for 8 hours.
Conclusion
Overall, the researchers successfully demonstrated the re-programmability of 3D-printed LCEs between polydomain and monodomain by incorporating exchangeable boronic ester bonds. Tailoring the printing parameters helped optimize the actuation behavior of the printed LCE structures. Moreover, the actuated shape could be predicted well with the finite element method.
The LCE structures’ actuation and reprogramming performance varied with the molar ratio of dynamic boronic ester bonds. LCE-35 specimens exhibited stable reversible actuation and re-programmability between polydomain and monodomain. However, LCE-20 was not re-programmable, while LCE-50 could not exhibit reversible actuation.
A limitation of the proposed methodology was the long time required for the reprogramming process, which required high temperatures. The researchers suggest developing other dynamic covalent networks to improve it, such as room-temperature reprogramming of dynamic disulfide bonds.
Journal Reference
Yu, X., et al. (2024). 3D printing of reprogrammable liquid crystal elastomers with exchangeable boronic ester bonds. Giant. DOI: 10.1016/j.giant.2024.100331
Disclaimer: The views expressed here are those of the author expressed in their private capacity and do not necessarily represent the views of AZoM.com Limited T/A AZoNetwork the owner and operator of this website. This disclaimer forms part of the Terms and conditions of use of this website.