A recent article published in Advanced Powder Materials introduced a recrystallization method using Ni catalysts to modulate the mass transport and decomposition of lithium oxalate (Li2C2O4), enhancing cathode pre-lithiation in Li-ion batteries (LIBs).
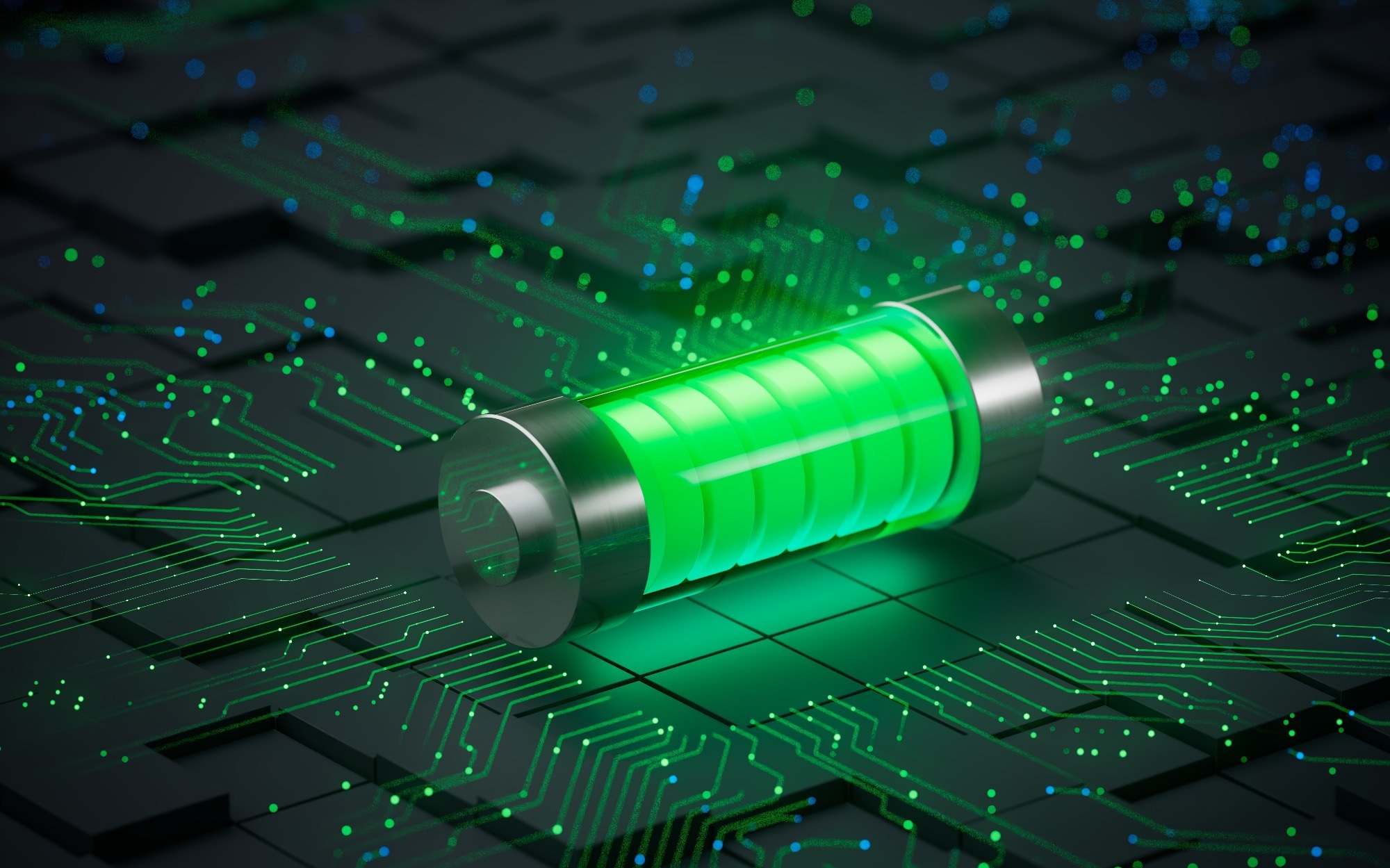
Image Credit: JLStock/Shutterstock.com
Background
Achieving higher energy density in LIBs requires silicon-based anode materials, which are known for their high specific capacity and low cost. However, the significant volume expansion of silicon (approximately 300 %) causes solid electrolyte interface fractures, consuming active Li+ and lowering the initial coulombic efficiency (ICE).
Pre-lithiation technology has emerged as a solution to this issue. While anode pre-lithiation is challenging and incompatible with current manufacturing processes, cathode pre-lithiation offers high compatibility with commercial LIB production.
Lithium oxalate (Li2C2O4) is a promising lithium compensation material with high theoretical capacity, air stability, and low cost. However, its low electronic conductivity and slow decomposition hinder commercial applications.
This study proposed Li2C2O4 recrystallization with atomic Ni catalysts (Ni-LCO) to enhance surface reactivity, shorten ionic transport pathways, and improve decomposition kinetics.
Methods
Nitrogen-doped reduced graphene oxide (N-rGO) was used as the base, and N-rGO loaded with nickel atoms (Ni/N-rGO) served as the catalytic solution. Both were prepared from graphite oxide and nickel (II) chloride hexahydrate via hydrothermal processing at 180 °C for 6 hours, followed by thermal reduction at 900 °C for one hour. Subsequently, Li2C2O4 was recrystallized (R-Li2C2O4) using commercial Li2C2O4 (P-Li2C2O4) with N-rGO and Ni/N-rGO to produce N-LCO and Ni-LCO, respectively.
The prepared materials were characterized using X-ray diffraction (XRD), scanning electron microscopy (SEM), and high-angle annular dark field-scanning transmission electron microscopy (HAADF-STEM). Particle size, specific surface area, and porosity were also measured.
The four-probe test method was used to assess the electronic conductivity of the samples, while in-situ differential electrochemical mass spectrometry (DEMS) was employed to analyze gas evolution during the charging of Ni-LCO. The Ni content in Ni-LCO was determined using inductively coupled plasma mass spectrometry (ICP-MS) after acid dissolution.
CR-2032 half cells were assembled with lithium-foil electrodes, while full cells were constructed using NCM811 (Ni-rich LiNi0.8Co0.1Mn0.1O2) and NCM811-Ni-LCO cathodes paired with SiOx anodes. To compare performance, battery cycling and electrochemical measurements were conducted for each cell type.
In addition to experimental studies, the adsorption model and underlying decomposition mechanisms of Ni/N-rGO with Li2C2O4 were investigated through spin-polarized density-functional theory (DFT) computations performed using the Vienna ab initio simulation package based on the projector augmented wave method.
Results and Discussion
XRD pattern of R-Li2C2O4 demonstrated no impurities from the recrystallization process with weaker diffraction peaks than those of P-Li2C2O4 due to the reduced particle size of R-Li2C2O4. SEM images also confirmed the decreased particle size after recrystallization.
This reduction in particle size likely results in more reactive surfaces and shorter ion transport distances in R-Li2C2O4. The maximum intensity diffraction peak of Li2C2O4 changed from (020) for P-Li2C2O4 to (111) for R-Li2C2O4, a highly reactive crystal face capable of accelerating decomposition rate.
In the electrochemical test, R-Li2C2O4 (150.6 mAh/g) delivered almost twice the specific charge capacity of P-Li2C2O4 (76.7 mAh/g) at 20 mA /g, corresponding to a higher decomposition rate. Additionally, the de-lithiation potential of Li2C2O4 decreased slightly from 4.9 V to 4.88 V after recrystallization, attributed to the shortened Li+ diffusion pathways.
To improve its electrochemical performance, Li2C2O4 was modified with different conductive additives, including super P black carbon (SP) and ketjenblack (KB). Notably, a mass ratio of 5:4 of KB to R- Li2C2O4 enhanced the decomposition efficiency to 99.7 % and reduced the decomposition potential to 4.46 V, which is the upper limit for traditional battery systems.
After recrystallization, SEM images showed uniformly dispersed R-Li2C2O4 particles in the N-rGO and Ni/N-rGO matrix. Due to their hierarchical and highly porous three-dimensional structures, the N-LCO and Ni-LCO systems achieved nearly 100 % decomposition rates, with initial charge capacities of 525.4 mAh/g and 527.3 mAh/g, respectively.
DFT calculations indicated a weaker adsorption tendency between Li2C2O4 and Ni-N4, resulting in a lower dissociation overpotential. In contrast, the N-rGO configuration tightly restrained the Li2C2O4 molecule.
In half-cell tests, the discharge-specific capacities of NCM811 and NCM811-Ni-LCO were similar, with no significant differences between their second charge-discharge cycles. Additionally, Ni-LCO did not compromise the cycle stability of the cathode material while significantly increasing the cell’s reversible capacity.
Conclusion
The researchers successfully demonstrated catalytic recrystallization of Li2C2O4, increasing its decomposition efficiency from 14.6 % to 100 % while modulating the corresponding decomposition potential from 4.90 V to 4.30 V.
The NCM811//SiOx full cell assembled with Ni-LCO showed a ∼30.4 % increase in the reversible capacity and a ∼21.5 % higher capacity retention ratio than the cell without Ni-LCO. This approach presents a promising pathway for highly efficient pre-lithiation technology, contributing to a more sustainable and reliable energy future.
More from AZoM: Guide to Lithium-ion Battery Solutions
Journal Reference
Zhang, H., et al. (2024). Unlocking the decomposition limitations of the Li2C2O4 for highly efficient cathode preliathiations. Advanced Powder Materials. https://www.sciencedirect.com/science/article/pii/S2772834X24000460
Disclaimer: The views expressed here are those of the author expressed in their private capacity and do not necessarily represent the views of AZoM.com Limited T/A AZoNetwork the owner and operator of this website. This disclaimer forms part of the Terms and conditions of use of this website.