A recent article published in Nature Materials established a reproducible protocol for characterizing the microstructure of lithium and sodium samples for anode-free solid-state batteries (SSBs) using a combination of focused ion beam (FIB) and electron backscatter diffraction (EBSD). Electrodeposited films at Cu|Li6.5Ta0.5La3Zr1.5O12, Al|Na3.4Zr2Si2.4P0.6O12, and steel|Li6PS5Cl interfaces were characterized using the proposed method.
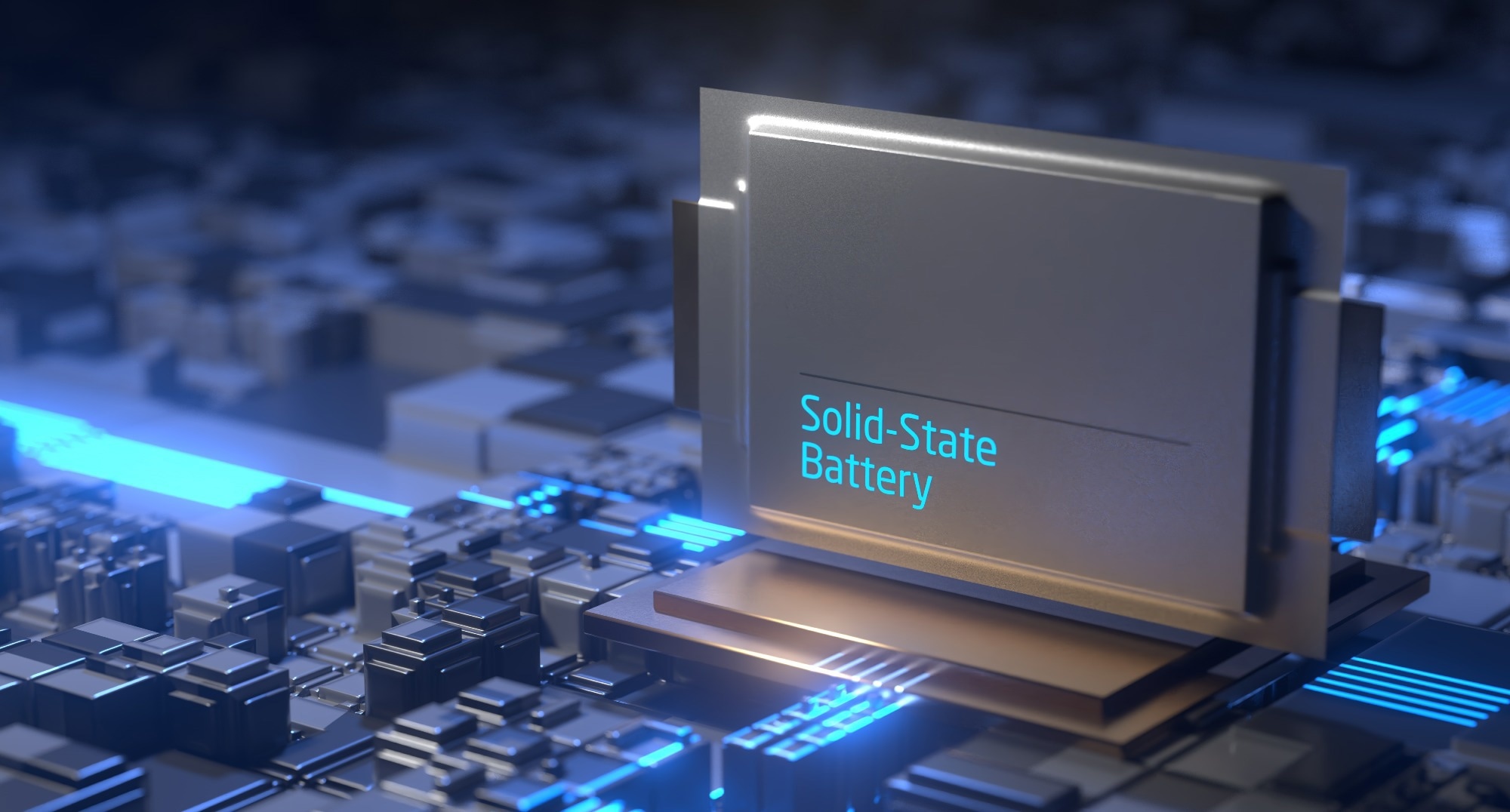
Image Credit: JLStock/Shutterstock.com
Background
SSBs are becoming popular due to their potential to surpass lithium-ion batteries as advanced energy storage devices. The successful implementation of lithium or sodium metal anodes in SSBs represents a significant technological advancement.
Anode-free or reservoir-free cells (RFCs) have emerged as an alternative to using alkali metal foils for cell fabrication, eliminating the need for costly handling of reactive alkali metal foils. However, controlling the morphology and microstructure of plated alkali metal at the collector-electrolyte interface is challenging.
The microstructure can significantly influence the anode performance. Additionally, the effect of alkali metal grain growth during storage at room temperature remains unknown. In this context, EBSD is the most suitable method to analyze the microstructure of metals and their evolution in SSBs. However, EBSD requires a very well-defined sample surface (flatness, crystallinity, and chemical composition).
Thus, this study presented a protocol to analyze the microstructure of lithium and sodium foils and deposited films in RFCs using EBSD.
Methods
Commercial lithium (R-Li) and sodium (R-Nametals were used for microstructural characterization without further purification. Their microstructures were modified by melting cleaned lithium and sodium ingots in stainless steel (SS) crucibles at 400 °C and 250 °C, respectively.
The resulting samples were quenched (Q-Li and Q-Na) in liquid nitrogen inside an argon-filled glovebox. Cross-sections for EBSD analysis were prepared by cutting through these ingots using a microtome blade.
Lithium and sodium were electrodeposited through a potentiostat using three cell configurations: Cu| Li6.5Ta0.5La3Zr1.5O1 (LLZO)|Li, SS| Li6PS5Cl (LPSCl)|Li, and Al| Na3.4Zr2Si2.4P0.6O12 (NZSP)|Na. Electrode connections inside a scanning electron microscope (SEM) were made for in situ EBSD experiments through a micromanipulator system.
Small passivation-free lithium and sodium metal ingots were inserted into a homemade EBSD holder at a 70 ° angle to the horizontal or alternatively set at 20 ° for cross-sectional EBSD analysis.
The electrodeposited lithium and sodium at the current collector-solid electrolyte interface were characterized by EBSD after fracturing the assembled Al|Na|NZSP|Na and Cu|Li|LLZO|Li cells perpendicular to the sample surface, followed by FIB polishing. The recorded EBSD maps were evaluated using the AZtecCrystal software package.
Results and Discussion
SEM images of each metal foil obtained after preparation exhibited lines and multiple triple junctions, indicating grain boundaries due to preferential degradation or morphological changes from pressing. Sodium foils displayed less pronounced lines, likely due to differences in impurities, mechanical properties, and surface chemistry.
The apparent grain sizes of R-Li (~100-300 µm), Q-Li (10-50 µm), and Q-Na (200-600 µm) confirmed the strong influence of thermal processing on the lithium and sodium microstructure. No grain growth was evident after Q-Li and Q-Na were stored at room temperature. EBSD analysis of freshly prepared surfaces validated these results, with exemplary Kikuchi patterns representing crystalline and sufficiently passivation-free surfaces.
Cross-sectional analysis revealed significant differences between thermally processed and reference metal foils for lithium and sodium. All cross-sectional maps displayed vertical grain boundaries, which were attributed to the high aspect ratio of the analyzed foils and their larger grain size compared to the foil thickness.
The average grain size for electrodeposited lithium was 20-100 µm at the SS|LPSCl and 10-100 µm at the CC|LLZO interfaces. Sodium at the carbon-coated Al|NZSP interface exhibited a grain width of around 10-150 µm. These grain sizes were smaller than those of other analyzed alkali metal foils, indicating minimal room-temperature storage grain growth in the electrodeposited films.
The signature voltage profile, inverse pole figure maps, and forward-scatter electron images of a stripped sodium anode confirmed the formation of pores close to the Na-NSZP interface. This preferential pore formation in grains instead of grain boundaries demonstrated rapid vacancy diffusion along grain boundaries, affecting the anode microstructure and electrochemical performance.
Conclusion
The researchers successfully established a comprehensive protocol for analyzing the microstructure of alkali metal foils using EBSD, enabling reliable surface and cross-sectional analysis. This protocol's success relied on maintaining inert gas or high vacuum conditions at all stages, delicate FIB cutting/polishing under cryogenic conditions, and the high sensitivity of the EBSD system.
Thermal processing allowed for tailored microstructures in both lithium and sodium, yielding varied grain sizes (10-200 µm for lithium and 200-600 µm for sodium). Grain growth was ruled out during room temperature storage and cryogenic FIB preparation. Moreover, the charging protocol and applied pressure governed the electrodeposited metal microstructure, presenting opportunities for optimizing metal anodes in SSBs.
Journal Reference
Fuchs, T., et al. (2024). Imaging the microstructure of lithium and sodium metal in anode-free solid-state batteries using electron backscatter diffraction. Nature Materials. DOI: 10.1038/s41563-024-02006-8, https://www.nature.com/articles/s41563-024-02006-8
Disclaimer: The views expressed here are those of the author expressed in their private capacity and do not necessarily represent the views of AZoM.com Limited T/A AZoNetwork the owner and operator of this website. This disclaimer forms part of the Terms and conditions of use of this website.