A recent article published in npj Materials Degradation explored the defining role of nanoscale heterogeneities in corrosion pathways in a high-strength aluminum alloy via detailed electron microscopy. Age-hardened aluminum alloy 7075-T651 was considered for this study, which investigated the significance of the heterogeneous distribution of Cr-containing dispersoids on nanoscale pit growth.
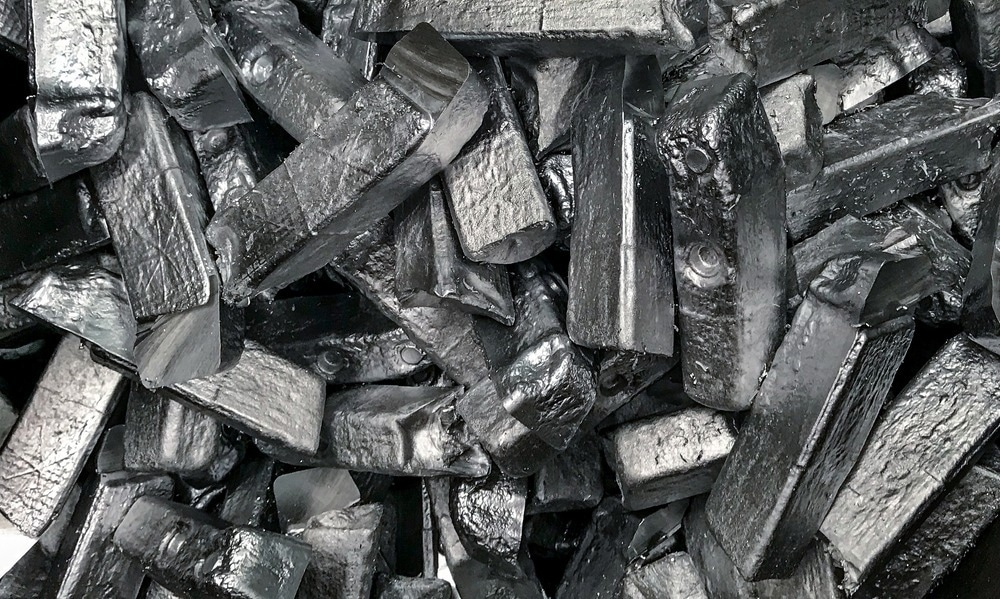
Image Credit: KickaPoo/Shutterstock.com
Background
Age-hardened 7xxx series aluminum alloys are commonly used for structural components in aerospace applications owing to their high strength-to-weight ratio. A specific set of thermomechanical treatments leads to unique multiphase microstructures comprising multiple types of intermetallic particles (IMPs) in these alloys.
However, the heterogeneous microstructure creates several micro-galvanic corrosion sites, which can result in large pits on exposure to aggressive electrolytes and become nucleation points for cracking under tensile load.
Given these alloys' wide range of critical applications, the role of IMPs in pitting and subsequent mechanical failure of 7xxx alloys has been extensively studied.
Several researchers have examined the importance of the morphology of grain boundary (GB) precipitates and their influence on stress corrosion cracking of 7xxx alloys.
However, the transition of intergranular dissolution into a three-dimensional (3D) pit remains less explored. The reason only a few micro-galvanic sites transition into pits with the potential for crack nucleation remains unknown.
Methods
This study used an extruded 7075-T651 Al alloy rod with a diameter of 20 mm. Microstructural and electrochemical studies were conducted on its longitudinal section. Various alloys appearing as IMPs in 7075-T651 were synthesized using pure metals via induction or arc melting under an Ar atmosphere.
Secondary electron micrographs and electron backscatter diffraction (EBSD) maps of the prepared specimens were obtained using a dual-beam scanning electron microscope (SEM). The EBSD data was analyzed using Aztec crystal software.
For post-exposure microscopy, the surface corrosion film after exposure was removed by ultrasonic cleaning in 70% HNO3 for 20-30 minutes. It was analyzed using a transmission electron microscope (TEM).
The evolution of pit density and surface morphology was examined via immersion corrosion testing of the specimen surface in 0.6 M NaCl for 200 hours under ambient conditions. The surface’s open-circuit potential (OCP) and electrolyte pH were continuously measured.
The microstructure of multiple samples exposed for different durations (1, 2, 4, 7, 12, 24, 48, 100, and 200 hours) was analyzed at different time intervals.
Potentiodynamic polarization tests were performed in a three-electrode setup with an Ag/AgCl reference electrode and a Pt mesh counter electrode. Additionally, these tests were performed in 0.6 M NaCl with varying concentrations of AlCl3 and NaOH to examine the impact of electrolyte chemistry.
Results and Discussion
The Cr-comprising dispersoids in 7075-T651 provided interfaces for precipitating coarse ƞ-Mg(ZnAlCu)2 particles, forming solute-depleted regions in the matrix during aging. This made the region more resistant to pit growth than the dispersoid-free region. Heterogeneously distributed dispersoids were also observed around the GBs.
The GBs in the dispersoid-free regions exhibited a continuous, thick line of ƞ-Mg(ZnAlCu)2, suitable for intergranular corrosion. In contrast, the GBs in the dispersoid-rich regions had a noncontinuous ƞ-Mg(ZnAlCu)2 line or coarse, noncontinuous θ-Al2Cu precipitates.
The few anodic ƞ-Mg(ZnAlCu)2 precipitates besides the GB in the dispersoids-rich zones were attributed to the localized consumption of Zn and Mg at the matrix-dispersoid interface. Thus, the dispersoids enhanced precipitation inside the grain, restricting the propagation of intergranular corrosion to enough size (or depth) for stabilizing a pit.
The alloy surface exhibited numerous micro-galvanic corrosion sites related to GB precipitates and constituent particles. However, the direction and rate of pit growth depended on the composition and crystallographic structure of the surrounding matrix. The susceptibility of such micro-galvanic sites to transform into a stable pit followed the order: Al23Fe4Cu > Mg2Si > GB ƞ-Mg(ZnAlCu)2.
Regardless of the nucleation site, the pits initially grew crystallographically with surfaces aligned along the {001} planes. However, within a grain, the pit growth was irregular. Post-corrosion TEM micrographs exhibited restricted pit growth inside the grain around the dispersoids.
A higher metal cation concentration promoted acidification and the entry of Cl—ions inside the pit, decreasing the robustness of corrosion products and increasing anodic dissolution on the pit surface. A pit in a long, dispersoid-free zone grew with minimum interference, while the enhanced anodic dissolution kinetics on the pit surface polarized the surrounding region cathodically, forcing the re-passivation of shallower pits.
Conclusion
The researchers comprehensively demonstrated that the nanoscale microstructural heterogeneity played a considerable role in pit growth and converting a pit into a crack nucleation site. Alternatively, a homogeneous distribution of dispersoids could inhibit pit growth in an aerospace-grade Al alloy 7075-T651.
However, obtaining a uniform dispersoid distribution during the homogenization of as-cast microstructures is challenging. Thus, this study underscored the importance of modifying the alloy composition and casting processes to fabricate a finer as-cast microstructure with minimum dispersoid-free zones. Some suitable techniques include controlling the cooling rate, electromagnetic stirring, and adding inoculants.
Disclaimer: The views expressed here are those of the author expressed in their private capacity and do not necessarily represent the views of AZoM.com Limited T/A AZoNetwork the owner and operator of this website. This disclaimer forms part of the Terms and conditions of use of this website.
Source:
Choudhary, S. & Kelly, R. G. (2024). Nanoscale heterogeneities dictate corrosion pathways in a high-strength aluminum alloy. npj Materials Degradation, 8(1). DOI: 10.1038/s41529-024-00520-3, https://www.nature.com/articles/s41529-024-00520-3