Textile cords in a rubber matrix form a key class of composites, which are used in many different applications, including tires, hoses, shock isolators, and air springs, to name a few.
Today’s automobile tires are some of the most complex of these designs. For a new tire line, the development process involves high cost and is R&D time intensive, often taking 18 months or more.
Finite Element Analysis
One tool used for modeling the tire is Finite Element Analysis (FEA) to achieve reduction in cost and market-reach time for new tire designs. According to Ohtsu Tire Company, through the implementation of tire modeling and simulation, the company was able to eliminate 200 physical tests per month and 10% of its tire development cycle time.
Accurate properties of individual materials, parts and structures are essential for accurate models. Tire cord is one of the parts for which characterization under appropriate conditions is a challenging task.
Tire Cord Dynamic Properties Testing and Results
A leading tire manufacturer provided a tire cord sample comprised two tire cord strands embedded in rubber tabs at both ends (Figure 1) to enable gripping without causing damage to the tire cord. An ElectroForce 3200 test instrument from Bose Corporation that is equipped with a hot/cold chamber was used to perform to the tests at room temperature and at 121°C over a frequency range of 2-200Hz in force control.
.jpg)
Figure 1. Tire cord embedded in rubber tabs at both ends
The required mean value is correlated to 58N per cord with 8.9N per cord of dynamic amplitude. The tire cord demonstrates an extensive creep behavior at this mean force level. Hence, setting a precondition to cycle for 35,000 cycles at 10Hz was done before acquiring any dynamic data. At 121°C, the modulus was roughly 50% of the modulus value at room temperature. However, the measured phase angle (tan delta) was the same at either temperature.
.jpg)
Figure 2. Storage and loss stiffness of tire cord
.jpg)
Figure 3. Relaxation data
Using the ElectroForce 3200 instrument, a conventional stress relaxation test was also performed on the tire cord to a displacement, which generated an initial force of 42N per cord. This test demonstrated that the force was reduced to 28.5N per cord after 10s. The data file size was optimized for this test using level crossing data acquisition. The results are illustrated in Figures 1 and 2.
Conclusion
The results demonstrate the ability of the ElectroForce 3200 instrument to provide accurate measurements of the dynamic properties of tire cords.
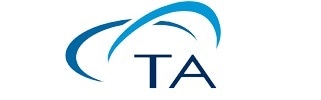
This information has been sourced, reviewed and adapted from materials provided by TA Instruments.
For more information on this source, please visit TA Instruments.