With the ever-increasing demand for oil, there is a rising need for improved oil recovery techniques to produce more from conventional reserves with high pressure and temperature (HPHT) conditions as well as technical innovation to access alternative resources. In these increasingly adverse conditions, selecting the inappropriate material may cause premature failures and expensive downtime.
VICTREX PEEK polymers have been delivering proven performance in hostile oilfield environments by extending the service life of wellhead equipment and downhole tools. Electrical connectors and seal back-up rings fabricated from VICTREX PEEK are capable of withstanding exposure to many different sour gases, gas fluids and oils, and have a pressure rating of up to 30,000psi and a continuous use temperature range of -60°C to 260°C.
High Performance Sealing Solutions from Victrex
.jpg)
Figure 1. Seals
Sealing systems (Figure 1) are one of the key components functioning in hostile conditions such as those experienced in the oil and gas industry. The increase demand for high consistency, traceability and performance forces oilfield tool makers to replace existing materials such as PPS and PTFE with certified and reliable material solutions like VICTREX PEEK, which are capable of withstanding high pressures and exhibit superior fatigue performance and stable properties over challenging operating conditions.
Watch the 'Sealed to survive the extremes' webinar from Victrex
Key features and benefits of VICTREX PEEK polymers in sealing applications:
- 300 times more creep resistance at HPHT when compared to fluoropolymers
- Proven performance and predictable service life data
- Design freedom with process versatility
- Unlike metal will not wear and gall resulting in damage
Durable Electrical Insulation Solutions from Victrex:
.jpg)
Figure 2. Wire and Cable
VICTREX PEEK polymers have found use in a suite of wire and cable (Figure 2) coating, slot liner and extruded sheath applications in downhole equipment, thanks to their innovative combination of high mechanical, electrical and temperature properties. VICTREX PEEK polymers single-layer extrusion coatings are capable of replacing multi-layer film wraps with no need for adhesives. VICTREX PEEK has high surface hardness for abrasion, inherent moisture stability, and cut resistance to avoid shorts for extended electrical continuity in service.
The following are the key features and benefits of VICTREX PEEK-based electrical insulation solutions:
- Reduced risk of electrical shorts (no pinholes)
- Cut and abrasion resistance allows for thinner insulation
- Thermal endurance extends service life in HPHT environments
- Ease of processing and design flexibility
- No need for adhesives
Proven Electrical Integrity for HPHT
.jpg)
Figure 3. Connectors
HPHT conditions are common in unconventional reserves, deep oil recovery, and even in conventional reservoirs with improved oil recovery techniques. Hence, it is necessary to protect power and data transmission round the clock. VICTREX PEEK has a proven record of success in both power and data transmission applications (Figure 3) in extreme environments, thanks to its consistent dielectric properties in hostile conditions, superior chemical and moisture resistance, and toughness for easier installation exceeding ceramics, glass, epoxy and metal composites.
Victrex PEEK-based polymers deliver:
- Proven robust electrical insulation for HPHT
- Double the power capacity compared to glass-ceramic connectors
- Improved shock and vibration resistance compared to glass connectors
High Performance Pipes for Hostile Conditions
.jpg)
Figure 4. Pipes
VICTREX Pipes (Figure 4), fabricated from VICTREX PEEK polymer for the oil and gas industry applications, deliver improved performance in extreme operating conditions due to their temperature, permeation, corrosion, wear, abrasion and chemical resistance. Exploration and production companies worldwide are achieving performance and cost benefits by replacing existing pipe technologies with Victrex polymer pipes as they offer:
- Extended service life and reduced downtime
- Reduced weight and overall deployment costs in deep water environments
- High durability and superior resistance to permeability and fatigue
- Reduced well operating costs related to tubing corrosion failures
- Excellent Chemical resistance to harsh oilfield operating conditions
In response to standardization requirements of the oil and gas industry, Victrex contracted MERL to perform an investigation to evaluate the compliance of VICTREX® PEEK 450G to the NORSOK M-710 Standard for sour (H2S) ageing at 100 bar and test temperatures of 175°C, 195°C and 210°C for up to five weeks. Results showed no measurable chemical deterioration for the VICTREX PEEK 450G in this time period of testing.
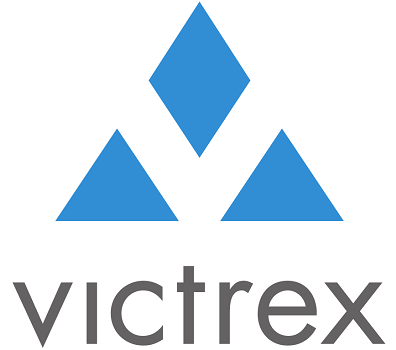
This information has been sourced, reviewed and adapted from materials provided by Victrex.
For more information please download the full brochure from Victrex.