Rising fuel costs and increasing environmental impact are key challenges for the aerospace industry, thus necessitating weight reductions to achieve improved fuel efficiency. OEMs have cost saving goals and considerable backorders to meet for next generation aircraft. Hence, it is critical for them to optimize and simplify the production and assembly process.
Extended service life cycles with high reliability are required as airlines demand over 20 years of safe flying with minimal maintenance requirements. Consistency and security across the entire supply chain is critical to address the rising demands for new aircraft. To meet these challenges, lightweight but strong materials are demanded by aerospace engineers to have more options for simplifying part designs, minimizing system costs, and providing durability in adverse conditions.
Victrex’ Lighter, Leaner Aerospace Solutions
Victrex has over three decades of experience in providing high performance polymers as an alternative solution to metals, thermoset composites, and other plastics in the aerospace industry. With the broadest PEEK portfolio in the market, Victrex with its 35 years of expertise not only provides a wide choice of material solutions to customers, but also offers the technical expertise and application know how to help them in designing next generation applications.
Victrex Polymers
VICTREX PEEK (Figure 1) is a substitute for aerospace materials, including aluminum (40% lighter), titanium (55% lighter), and stainless steel (70% lighter). The material is offered in many different forms, including unfilled, carbon fiber reinforced, or glass-filled pellets or powders, with a melt viscosity ranging from high flow to low (90, 150, 380, 450, 600, 650). It can be compression molded, extruded, injection molded and compounded.
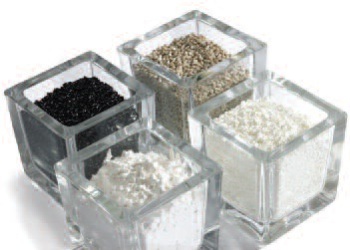
Figure 1. VICTREX PEEK
Polymers for Composites
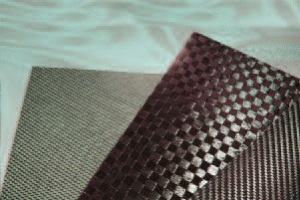
Figure 2. VICTREX PEEK-based composites
VICTREX PEEK can be utilized as a matrix material (Figure 2) for thermoplastic composites to obtain unprecedented strength-to-weight ratios when compared to metals and thermoset composites. The resulting material exhibits 4x specific stiffness, 4x higher fatigue strength, and 5x higher specific strength than aluminum.
APTIV® Films, VICTREX Pipes™ and VICOTE® Coatings
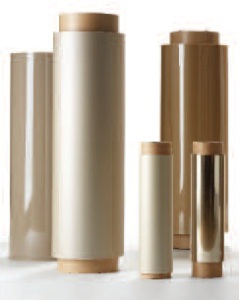
Figure 3. APTIV film
APTIV film (Figure 3) is thin and flexible, with a thickness range of 6-750µm and widths of up to 1.5m. It can be secondary processed by thermoforming, welding, heat sealing, and lamination. It offers up to 60% reduction in weight vs. polyvinyl fluoride (PVF) film.
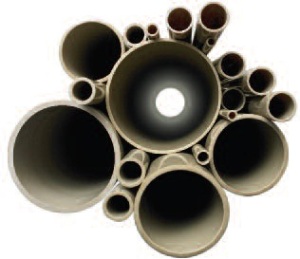
Figure 4. VICTREX pipes
VICTREX Pipes (Figure 4) are innovative lightweight tubing systems that satisfy rigorous performance, quality and safety specifications within the aerospace market. For a 1” tube used for low-pressure fluid transport, the system is 60% lighter than stainless steel tubing, 45% lighter than titanium tubing, and 33% lighter than aluminum tubing, thereby help saving significant fuel costs. It can be clamped, flared, formed and bent.
VICOTE Coatings deliver improved chemical, high temperature, abrasion, and wear resistance in challenging aerospace applications. The one-coat system with smooth uniform surface exhibits superior creep resistance. It is eco-friendly as it is devoid of halogen and is UL V-0 rated.
Broad Range of Aerospace Applications
Brackets, Clamps and Stand-Offs
Composite brackets fabricated from VICTREX PEEK deliver exceptional strength at significantly lighter weights than metals. It has 5x higher specific strength and provides up to 70% weight savings when compared to metals. It can be manufactured within minutes when compared to hours for thermosets.
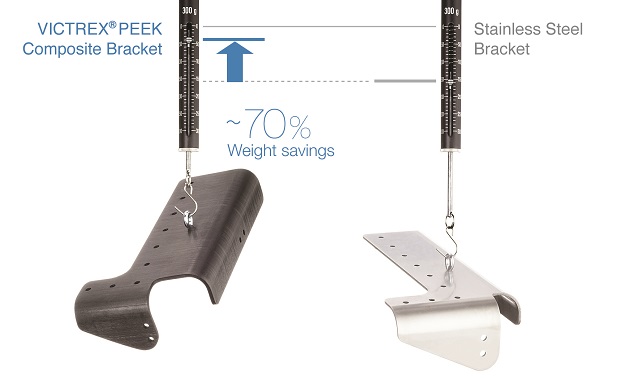
Figure 5. Composite brackets made from VICTREX® PEEK (left) versus brackets made of stainless steel (right)
VICTREX PEEK coupled with a silicone overmold is excellent for wiring and tubing clamps and stand-offs for the Boeing 787. It provides 20% weight savings when compared to aluminum and reduces installation time by 30% when redesigned to consolidate components. Moreover, it eliminates anti-corrosion treatments.
Watch a video about metal-to-plastic conversion on the Boeing 787:
VICTREX® PEEK Clamps provide Weight Savings in Aerospace
Thermal Acoustic Insulation and Fasteners
Insulation systems fabricated from APTIV film deliver durable, flame resistant solutions for lining the entire fuselage of the aircraft. These systems reduce weight by up to 60% when compared to PVF film. They are rated for low flame, smoke and toxicity and pass FAA burn-through barrier and cover film laminate testing.
Connectors and Tubing Systems
Connectors made from VICTREX PEEK have 9% less weight when compared to stainless steel counterparts. They facilitate easier installation when redesigned to consolidate several clips into a one-piece component. They exhibited nominal property degradation when tested in hydraulic fluid at 70°C for 1,000 hours.
VICTREX Pipes systems were chosen for the cargo drainage system of the Airbus A350 XWB. They deliver 33% weight reduction when compared to metal tubing. With superior corrosion resistance, they offer design freedom for improved aircraft space utilization.
Advantages of Victrex Materials
With VICTREX PEEK-based composites and VICTREX PEEK 90HMF40 injection molding grade, engineers can achieve equal part strength and stiffness at a weight reduction of up to 55% when compared to aerospace metals (Figures 6).
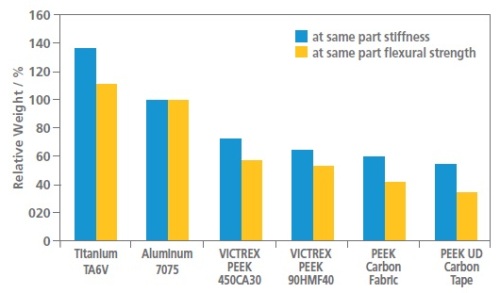
Figure 6. Beam with same structural stiffness and strength at 120°C with aluminum as reference (100%)
VICTREX PEEK is widely recognized for superior chemical resistance over a wide temperature range. VICTREX PEEK 90HMF40 polymer delivers up to 100x longer fatigue life when compared to typical aerospace aluminum alloys. The use of chopped glass or carbon fibers to reinforce VICTREX PEEK makes the material to satisfy or surpass the stiffness and strength of aerospace metals. This thermoplastic also exhibits high mechanical properties beyond the glass transition temperature, thanks to its semi-crystalline structure.
VICTREX PEEK is a fully recyclable material, and exhibits no loss in tensile strength performance over 5,000 hours at 260°C, making it suitable for applications that are under long-term exposure to high temperatures. The material also delivers high mechanical properties at very low temperatures down to -65°C. Filled VICTREX PEEK grades exhibit outstanding dimensional stability due to reduction in coefficient of expansion by the polymers. VICTREX PEEK is inherently flame retardant, thus delivering superior performance when subjected to fire.
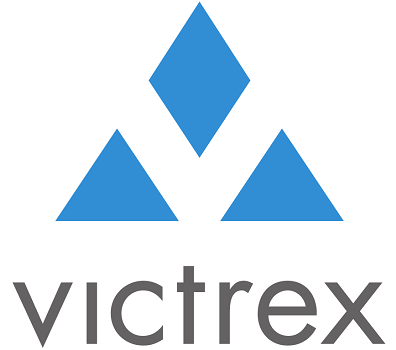
This information has been sourced, reviewed and adapted from materials provided by Victrex.
For more information on this source, please visit Victrex.