Feb 22 2001
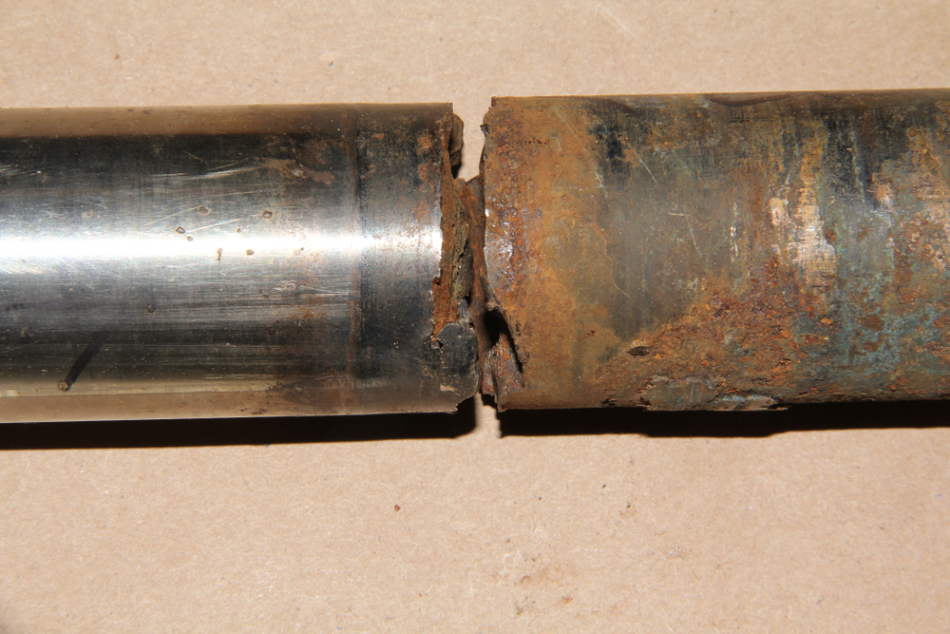
Image Credit: lbrumf2/Shutterstock.com
In a corrosive environment, fatigue constitutes metallic corrosion. This means that there is a premature surface degradation of a particular material, bringing about a shorter time for nucleation.
In addition to the problems that can occur with stress corrosion cracking (SCC) due to the effects of static stress, in many situations, the applied stresses are cyclic as a result of mechanical or thermal effects.
Under non-corrosive conditions, cyclic or varying stress levels can result in fatigue damage at surfaces and ultimately lead to the growth of fatigue cracks and even failure. Under corrosive conditions, fatigue cracks may be initiated, at corrosion pits for example, at a much earlier stage during service life. These cracks may grow faster in the corrosive environment. Importantly, stress corrosion causes intergranular cracks, while corrosion fatigue is associated with transgranular cracks.
The combined effect of both corrosion and fatigue will, therefore, be responsible for failure after a smaller number of stress cycles under these conditions, which is comparable to that which would be expected in a non-corrosive situation.
In ferrous alloys, a fatigue (endurance) limit is obtained under non-corrosive fatigue conditions. At stress levels below this limit, fatigue failure is not expected. Corrosive conditions remove this limit, thereby giving the possibility of failure even at low levels of stress.
The fatigue life accepted as a maximum stress value is also referred to as fatigue strength. Fatigue strength is decreased anytime a material is put into hostile conditions. Accurately calculating the odds of corrosion fatigue requires the consideration of environmental, stress and metallurgical variables.
Corrosion fatigue tends to produce a number of growing cracks, rather than the more normal single crack in fatigue under conditions where corrosion has no influence. The corrosion fatigue cracks usually develop normal to the main tensile stress and do not branch, whereas SCC cracks are highly branched.
While the causes and situations surrounding corrosion fatigue can vary widely, the propagation of cracks brought on by corrosion fatigue is caused by common factors. Increasing stress intensity can facilitate crack growth, particularly in cold dry environments.
The rate of load frequency can also increase crack growth, with cracking decreasing as frequency increases. In a corrosive environment, increased stress ratio increases crack growth. The electrode potential of an aqueous environment in which corrosion fatigue is occurring has a strong effect on crack propagation. Finally, an environment with significant chemical activity can decrease a metal is resistance to corrosion fatigue, and therefore crack propagation.
Corrosion fatigue fracture surfaces may or may not be coated with corrosion products. However, these effects are entirely dependent upon the relative effects of corrosion and stress. There will be more evidence of corrosion at lower stress levels or lower frequencies of stress cycling as a result of the increased time of exposure. Unlike stress corrosion cracking, corrosion fatigue is a general problem and is not confined to a specific alloy environment combination.
Corrosion fatigue assessments are often carried out on materials to determine the possible rate of corrosion fatigue in a particular application, and the potential issues it can cause. For instance, by understanding the crack growth qualities of corrosion fatigue on marine crafts and structures, it is possible to design such things to more efficiently avoid catastrophic failures.
Preventing Corrosion Fatigue
Corrosion fatigue can be easily mitigated, or even prevented, with a number of solutions.
The use of chemical or physical inhibitors and coatings can delay the onset of corrosion fatigue. Measures to reduce or eliminate pressure and vibration on a metallic surface can also significantly reduce corrosion fatigue. Some high-performance alloys are also highly resistant to corrosion fatigue.
References and Further Reading
This article was updated on 17th February, 2020.