Most failures in mechanical components and structures are caused by fatigue, making the study of fatigue and its failure mechanics essential. Responsible for approximately 80 % of recorded failures in metallic structures and machinery parts, progressive damage from fatigue effects presents a significant challenge for designers and structural engineers.1
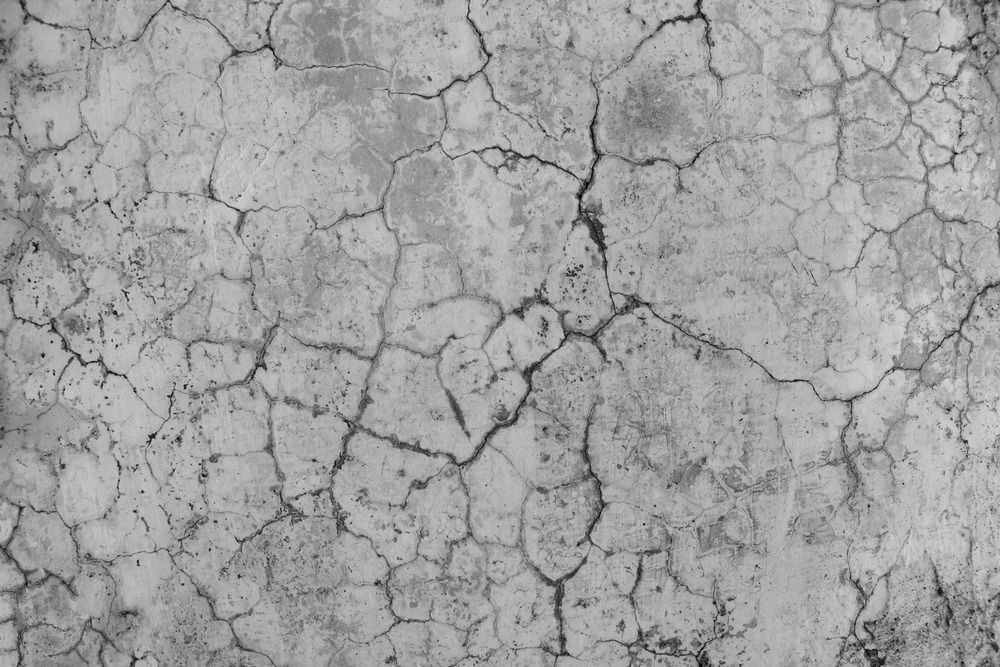
Image Credit: ParasharMangela/Shutterstock.com
A significant incident attributed to fatigue was the rupture of the fuselage in De Havilland’s Comet commercial jetliner in 1954. Continuous pressurization and depressurization cycles created fatigue stresses near the square-shaped windows, resulting in stress concentrations that led to fatigue cracks. These cracks eventually grew, causing the aircraft to crash mid-flight.2 This incident underscores the importance of thoroughly studying fatigue mechanisms and types.
Overview of Material Fatigue
Mechanical parts are more frequently subjected to cyclic loads than solely static loads. Fatigue issues are commonly observed in turbine blades, aerospace components, locomotive systems, large structures like bridges, and mechanical gears.
Cyclic loads result in fluctuating stresses, causing microscopic damage or micro-cracks. These micro-cracks can proliferate under continuous cyclic loading over time, leading to failure at stress levels well below the material’s specified yield or failure stress. This type of failure, known as fatigue failure, necessitates a thorough analysis of stress and strain under repeated loading cycles, along with regular maintenance, to prevent excessive damage from fatigue.3
Mechanism of Fatigue Failure
Fatigue failure is a gradual process that develops over time, with several stages that contribute to microscopic damage.
Cyclic stresses are essential for initiating fatigue cracks, and the number of applied stress cycles significantly influences the fatigue life of materials. Structural experts in various industries define the stress cycle based on specific loading and conditions.
For instance, in steel bridge design, structural engineers calculate fatigue life by considering the passage of a single truck along the bridge length as one stress cycle for a structural member.4
Stages of Fatigue Failure
Fatigue failure begins with crack initiation, which grows progressively under continuous loading. Structural engineers generally categorize the fatigue failure cycle into three main stages: crack initiation, crack propagation (encompassing both short and long crack growth), and final failure or separation.
Crack Initiation
Fatigue cracks typically initiate at locations with geometric or structural discontinuities, such as machined holes, slots, cross-sectional irregularities, and near riveted connections.5 These discontinuities lead to dislocations that accumulate under continuous stress cycles, forming persistent slip bands. These slip bands act as primary stress raisers or concentration points where fatigue crack initiation begins.
At points of highest stress concentration, crack nucleation primarily occurs due to intense plastic deformation. Accumulated plastic deformation from repeated loading and unloading cycles can result in fatigue cracks.6
Crack Propagation
The short crack propagation stage marks the initial phase of crack growth, where numerous small cracks form within the material, with their sizes largely dependent on the microstructure of the discontinuity.7 Since these cracks are on the scale of the microstructure, factors such as grain size and stress levels are crucial in determining crack growth.
If the applied stress is sufficiently high, a few cracks will overcome microstructural barriers and continue to grow. Once these cracks reach the scale of characteristic mechanical dimensions, they are classified as mechanically short cracks.
This stage is followed by rapid crack growth, primarily perpendicular to high-tensile microscopic stress planes. Here, longer cracks form, with the local microstructure exerting minimal influence on their propagation.
Final Fracture
Final fatigue fracture occurs when a crack reaches a critical length. This threshold dimension for catastrophic fatigue failure is not fixed; it varies based on the geometry, material properties, and stress cycles of the structure.8
Close examination of fatigue failure surfaces reveals a smooth region resulting from crack growth and surface wear, alongside a rougher region formed when the load becomes excessive.9 Another characteristic of fatigue failure is the presence of beach marks—fine, arch-shaped lines that start at the crack initiation point and extend to the ductile fracture zone. These marks, also known as macroscopic striations, indicate the progression of the crack.
Understanding S-N Curves and Fatigue Life
In the 1850s, Wohler was the first to study the fatigue behavior of steel structures and to develop S-N curves. Investigating a train crash in France caused by repeated low-level cyclic stresses, he observed that failure occurred at stress levels much lower than the ultimate tensile strength of the materials. He plotted a graph with stress amplitude (S) on the vertical axis and the number of cycles (N) on the horizontal axis for fatigue analysis, known as the S-N curve.10
The S-N curve typically slopes downward. Researchers have described the S-N curve in various ways, all conceptually and theoretically accurate. One approach divides the S-N curve into three distinct phases: the finite life line, the knee point, and the fatigue limit horizontal line.11
What is a SN Curve?
When cyclic stress amplitude is plotted against the number of cycles to failure, a downward trend is observed. Initially, this downward trend indicates the finite fatigue life region, showing that as the magnitude of cyclic stresses decreases, the material endures more cycles and has a longer fatigue life compared to higher stress levels.
The trend continues until reaching the knee point, where the graph flattens into a horizontal line. The knee point represents the minimum number of cycles at which applied stresses no longer cause failure. The horizontal line beyond the knee point represents the fatigue limit, below which the material does not experience fatigue failure.
Another way to represent the S-N curve is by highlighting the plastic and elastic regions, including the ultimate, yield, and endurance limits.11
The highest point on the graph is the ultimate tensile strength, indicating the maximum stress the material can endure. The yield strength point marks where permanent deformation begins, and the endurance or fatigue limit is the knee point, below which the material does not fail. Beyond the fatigue limit, the curve forms a horizontal line.
The crankshafts in locomotive engines are carefully designed to operate within the infinite fatigue life region, below the fatigue limit line. This region is identified as infinite fatigue life based solely on the number of cycles to failure, without accounting for other factors such as corrosion or environmental conditions.
The elastic region, located between the yield strength and the fatigue limit, is also known as the high-cycle stress region. Here, crack propagation during fatigue is significantly influenced by geometric irregularities. S-N curves are fundamental for evaluating the fatigue life of metals, and experts use various testing methods to plot these curves for specific materials.10
Factors Affecting Fatigue Life
Research over the years has shown that structural design is a key factor influencing fatigue life, with material properties playing a significant role. Different materials have distinct microstructures that impact the crack propagation process during the fatigue cycle.
Effect of Surface Finish and Surface Treatment
Surface finish and conditioning are critical for determining fatigue strength, as cracks typically initiate at the surface. Proper surface treatments, like shot-peening and cold-rolling, result in smoother finishes, which can enhance fatigue life. These techniques are widely used in industry to improve fatigue characteristics.12
Environmental Factors in Fatigue
Environmental conditions also impact fatigue life. Research shows that saline solutions accelerate crack growth, reducing the fatigue life of structural components.13 Additionally, operating temperature significantly affects fatigue strength; higher temperatures are associated with reduced fatigue strength in materials.
Corrosion is another environmental factor that contributes to mechanical component failure. Studies have shown that corrosive environments have a more pronounced negative effect in the low-cycle region compared to the high-cycle region. Thus, corrosion reduces the fatigue strength of a material, with greater deterioration observed at lower stress amplitudes.14
Geometrical Parameters in Fatigue Strength Determination
The geometry of structural parts significantly influences fatigue life. Design irregularities, such as notches and holes, create localized stress concentrations that are analyzed in fatigue assessments. Complex geometries lead to stress concentration points that accelerate crack growth.15
In structural design, engineers must consider loading conditions, operational environment, and temperature variations to select appropriate geometries and treatment methods. This approach optimizes functionality and enhances fatigue life, supporting cost-effectiveness and efficiency.
Types of Fatigue Failure
Fatigue failures generally result from either high-amplitude cyclic stress or low cyclic stress. If failure occurs after a mechanical sub-system has undergone thousands or millions of loading cycles, it is classified as a high-cycle fatigue failure.16 High-cycle fatigue stresses lie within the elastic range of the S-N curve. Designers commonly use Finite Element Analysis (FEA) to identify regions susceptible to high-cycle fatigue failure.17
Low-cycle fatigue failures are characterized by high-amplitude cyclic stresses applied to a component for a low number of cycles. These stresses typically exceed the yield strength of the material, with failure occurring after even a few hundred cycles. Significant plastic deformation often occurs before the final collapse in low-cycle fatigue.18
Thermal fatigue, another form of fatigue failure, is caused by cyclic stresses from thermal loads or fluctuating operating temperatures. Designers address this by minimizing thermal gradients and optimizing operating temperatures.19
Fatigue Testing
Among traditional fatigue testing methods, the rotary bending and deflection bending tests are widely used. The rotary bending test enables fatigue testing at higher frequencies. In this test, a round specimen is rotated in specialized equipment with constant bending stress applied, subjecting it to complete cycles of alternating tensile and compressive stresses.20 Rotating bending fatigue tests are performed on solid round fine wire to determine the fatigue strength of metallic materials over a specified lifespan within the fatigue regime.
As per ASTM, the deflection-bending test is used for metallic sheets and strips to evaluate their resistance to fatigue crack development and fatigue-based damage under a high number of cycles (105 to 109 range). This test helps assess how material variations influence fatigue strength and provides data for selecting copper alloy spring materials for repeated strain cycling conditions.21
In automotive and aerospace component testing, multiaxial fatigue testing is used, where components undergo complex cyclic stresses, resulting in repeated multiaxial stress applications. For turbine engines and other thermomechanical systems, fatigue testing involves varying thermal and mechanical loads to replicate real-life conditions. This approach tests fatigue strength under applied loads and offers insights into the effects of thermal fluctuations.22
Enhancing Fatigue Resistance
Fatigue is a critical failure phenomenon observed in both daily life and industrial settings. Researchers are developing methods to enhance material fatigue resistance through various techniques and by creating new testing methods.
Advances in manufacturing processes are expected to significantly improve component fatigue life, resulting in cost savings and substantial economic benefits.
More from AZoM: Harnessing AI and Machine Learning for Advanced Materials Testing
References and Further Reading
- Hosseini, Z., et al. (2018). On the theoretical modeling of fatigue crack growth. Journal of the Mechanics and Physics of Solids. https://doi.org/10.1016/j.jmps.2018.07.026
- Federal Aviation Administration (2024). De Havilland DH-106 Comet 1. [Online] Federal Aviation Administration. Available at: https://www.faa.gov/lessons_learned/transport_airplane/accidents/G-ALYV
[Accessed on: October 29, 2024].
- Khalifeh, A. (2023). Perspective Chapter: Fatigue of Materials. Failure Analysis - Structural Health Monitoring of Structure and Infrastructure Components. https://www.doi.org/10.5772/intechopen.107400
- Schilling, C. (1984). Stress cycles for fatigue design of steel bridges. Journal of Structural Engineering. https://doi.org/10.1061/(ASCE)0733-9445(1984)110:6(1222)
- Nishida, S. (2014). Failure analysis in engineering applications. Nikkan Kogyo Shimbun, Ltd. Available at: https://books.google.com.pk/books?hl=en&lr=&id=SCSjBQAAQBAJ&oi=fnd&pg=PP1&dq=S.+Nishida,+Failure+Analysis+in+Engineering+Applications,+Butterworth+Heinemann,+Oxford,+UK,+1992.&ots=oGhC71jgSe&sig=w7kb23Y1_epKR9aOk7NnyBwSTM0
- Lukáš, Petr. (1996). Fatigue crack nucleation and microstructure. Fatigue and Fracture. ASM International. https://doi.org/10.31399/asm.hb.v19.9781627081931
- Vallellano, C., et al. (2008). On the estimation of microstructural effects in the near-threshold fatigue of small cracks. The Journal of Strain Analysis for Engineering Design. Available at: https://doi.org/10.1243/03093247JSA351
- Zerbst, U., et al. (2019). Defects as a root cause of fatigue failure of metallic components. I: Basic aspects. Engineering Failure Analysis. https://doi.org/10.1016/j.engfailanal.2019.01.055
- González-Velázquez, JL. (2018). Fractography and failure analysis. Switzerland: Springer International Publishing. https://doi.org/10.1007/978-3-319-76651-5
- Siemens. (2019). What is a SN-Curve? Simcenter-Training. [Online] Siemens. Available at: https://community.sw.siemens.com/s/article/what-is-a-sn-curve
[Accessed on: November 01, 2024].
- Murakami, Y., et al. (2021). Essential structure of S-N curve: Prediction of fatigue life and fatigue limit of defective materials and nature of scatter. International Journal of Fatigue. https://doi.org/10.1016/j.ijfatigue.2020.106138
- Altair HyperLife. (2023). Other Factors Affecting Fatigue. [Online] Altair HyperLife Fatigue Analysis Overview. [Online]. Available at: https://2023.help.altair.com/2023/hwdesktop/hlife/topics/solvers/os/analysis_fatigue_other_factors_r.htm [Accessed on: November 01, 2024].
- Huneau, B., et al. (2006). Evaluation of environmental effects on fatigue crack growth behaviour of a high strength steel in a saline solution with cathodic protection. International journal of fatigue. https://doi.org/10.1016/j.ijfatigue.2005.04.011
- Morgantini, M., et al. (2018). The effect of corrosive environment on fatigue life and on mean stress sensitivity factor. MATEC web of conferences. EDP Sciences. https://doi.org/10.1051/matecconf/201816503001
- Li, Z., et al. (2021). A fatigue life estimation approach considering the effect of geometry and stress sensitivity. Theoretical and Applied Fracture Mechanics. https://doi.org/10.1016/j.tafmec.2021.102915
- Ansys. (2024). How to Assess and Prevent High-Cycle Fatigue Failure. [Online] Ansys. Available at: https://www.ansys.com/blog/how-to-prevent-high-cycle-fatigue-failure [Accessed on: November 02, 2024].
- Lambda Technologies Group. (2023). High Cycle Fatigue. [Online] Lambda Technologies Group. Available at: https://www.lambdatechs.com/high-cycle-fatigue/ [Accessed On: November 02, 2024].
- Quadco Engineering (2024). Differences between high-cycle and low-cycle fatigue? [Online] Quadco Engineering. Available at: https://www.quadco.engineering/en/know-how/material-fatigue-difference-between-high-and-low-cycle.htm [Accessed on: November 02, 2024].
- Inspection Engineering. (2023). Overview of Thermal Fatigue. [Online] Inspection Engineering. https://inspectioneering.com/tag/thermalfatigue [Accessed on: November 02, 2024].
- Yalcin, D. (2021). Rotating Beam Fatigue Test Method. iMechanica. (Online). Available at: https://imechanica.org/node/25113 [Accessed on: November 02, 2024].
- ASTM International. (2021). ASTM B593-20. Standard Test Method for Bending Fatigue Testing for Copper-Alloy Spring Materials. [Online] ASTM International. Available at: https://www.astm.org/b0593-20.html [Accessed on: November 02, 2024].
- Biopdi. (2023). Comprehensive Guide to Fatigue Testing: Methods, Materials & Applications. [Online] Biopdi. Available at: https://biopdi.com/fatigue-testing/ [Accessed on: November 02, 2024].
Disclaimer: The views expressed here are those of the author expressed in their private capacity and do not necessarily represent the views of AZoM.com Limited T/A AZoNetwork the owner and operator of this website. This disclaimer forms part of the Terms and conditions of use of this website.