By AZoM.com Staff Writers from original material supplied by Tecvac
The aerospace industry is one of the most heavily scrutinized, mainly because of the sheer volume of air traffic. The industry also faces constant pressure to cut down its carbon footprint and to make air travel environmentally friendly. Back in 2008, almost 7,000 flights used to take off a day to and from UK airports. Thus, in order to reduce emissions, the Advisory Council for Aeronautics Research in Europe has set specific targets and has stipulated that new aircraft built in 2020 must produce 50% less carbon dioxide (CO2) than those built in 2000.
Development of Lightweight Aircraft
Since the amount of CO2 emitted by an aircraft engine is directly related to the amount of fuel burned, CO2 can be reduced by making the aeroplane lighter. Tecvac, a surface engineering company based in Cambridge, specializes in depositing hard-wearing coatings onto surfaces to extend their lifetime. The company worked with Airbus Operations, Sheffield University and NMB-Minebea to make a product that could considerably reduce the weight of new Airbus aircraft.
Each Airbus aircraft includes about 2,772 steel bearings. As a result, Airbus was looking for a lightweight alternative. To this end, titanium alloy provided a suitable solution. If this alloy is used to replace all of the steel bearings, this could save a minimum of 400kg. However, titanium alloy is not sufficiently strong to bear the aircraft’s weight; for instance, bearings in landing gear have a tendency to wear out under pressure.
Researchers already knew that a hard-wearing coating would not be suitable to overcome this problem. The coating may crack and this in turn can affect the titanium. Tecvac worked on this project and provided a suitable solution by improving existing technology. The company developed an innovative treatment that made the titanium’s surface much more resilient, and then added a hard-wearing coating to the enhanced titanium alloy bearings. A combination of these technologies provided an appropriate solution to Airbus. Using resilient titanium alloy in place of steel bearings resilient titanium alloy means that aeroplanes can become considerably lighter and thus reduce fuel consumption and the impact on the environment.
Market for New Technology
.jpg)
Figure 1. Aeroplane’s landing gear
There is a huge market potential for this novel technology. Manufacturers across the globe are looking for new ways to reduce the weight of aircraft. In fact, Airbus has already placed an order worth £19 million for a specific type of wing structure bearing joining the main landing gear (Figure 1) for the new Airbus A350. Once this structure has been upgraded to titanium alloy, other bearings on the Airbus aircraft will be replaced. Moreover, in addition to the work on new planes, bearings will also be replaced on working planes.
Conclusion
Tecvac is exploring other options to make the titanium bearings stronger and thus increase their capacity to take more weight. The company is also upgrading its manufacturing capability to offer the latest treatments According to Department for Transport estimates, CO2 emissions from UK aviation were 37.5 million tonnes in 2005 and this number is estimated to increase to 60.3m tonnes by 2050. Therefore, demand for this type of technology is likely to increase.
About Tecvac
Tecvac UK is part of the Wallwork group of companies. Tecvac Specialises in hard coatings, heat treatment, machine build, vacuum brazing and a range of other engineering services.
The Tecvac plant has facilities for thermal processing of components using vacuum Technology. The facility on the outskirts of Cambridge is split into three processing streams:
- Vacuum Heat Treatment
- Vacuum Brazing
- Physical / Chemical Vapour Deposition (PVD / PECVD).
The latter involves the deposition of micro-fine coatings using specialised technologies such as Electron Beam, Magnetron Sputtering and Plasma Enhanced Chemical Vapour systems .
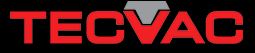
This information has been sourced, reviewed and adapted from materials provided by Tecvac.
For more information on this source, please visit Tecvac.