By AZoM.com Staff Writers from Original Content Supplied by Tecvac
The aerospace industry, at all levels, is facing challenges of lowering fuel consumption, minimizing lifetime cost of operations, reducing carbon dioxide emissions, and alleviating health and environmental impacts. This necessitates the introduction of new materials to provide lighter and stronger airframes as well as new generation of high-efficient aero engines.
Apart from these developments, there are demands for reducing other environmental impacts such as lowering the use of adverse and environmentally harmful materials and easy material recovery for recycling after the service life of the components. The commercial impact of these demands will be prolonged service life that optimizes potential time on the wing and improves return on investment for the aerospace operators.
Addressing Problems Associated with Lightweight Aerospace Materials
Apart from carbon fiber composites and lighter yet stronger aluminum alloys, titanium is also used as a substitute for steel or other dense metals in aerospace components such as struts and bearings to achieve considerable reduction in weight and fuel consumption.
Although titanium exhibits high strength, corrosion resistance and fatigue resistance, its tendency for metal- to-metal adhesion or galling caused by low hardness and poor coefficient of friction necessitate surface treatment in order to reduce the requirement for more frequent maintenance. In light loading cases, PVD applied titanium or chromium nitride coating that facilitates lubricity can address these problems. However, in heavy loading cases, this treatment is insufficient because of the instability of the substrate.
To overcome this problem, Tecvac offers a duplex coating, which involves hardening of the substrate by producing a hardened nitride diffusion zone that extends to 15-20µm underneath a lubricious PVD applied surface coating. Both hardening and final coating are completed in a single process cycle. The established core process called Nitron-O is available worldwide and can satisfy several requirements of the aerospace industry. Tecvac has customer specific variations to this technique and the ability to explore variations of the process to fulfill specific technical requirements of the customers.
Engine Performance Improvement Solution
PVD applied coatings have several purposes within the engine where improved surface properties of engine parts will extend service intervals. High pressure, temperature and the erosive forces of airflow and impurities in the air stream contribute to service life reduction of compressor aerofoils. These problems can be addressed by Nitron Flight, a multi-layer coating based on chromium, titanium, carbon/metal carbide or chromium/aluminum.
Depending on the process, six to eight layers of Nitron Flight may be applied to form a surface that conforms well to the polished substrate. This results in a low stress surface coating exhibiting high resilience to delamination compared a single layer coating of the same thickness. A major European maintenance overhaul and repair contractor has used this chromium based coating on compressor blades to compare the performance of an untreated reference engine and an engine with a Nitron Flight treated compressor section in on-wing trials that have now completed more than 10,000 flight hours. The results demonstrated the potential of recovering the treatment cost within seven months and achieving savings of $156,000 per engine over a typical five year, 25,000 flight hours (FH), cycle.
Furthermore, the fuel flow (FF) and exhaust gas temperature margin (EGTM) were beyond expectations at 0.5%, whereas the value was 0.3% on the reference engine. After 10,000 FH, the Nitron B coated blades still had coating over them with the super polished substrate remain unaffected compared to the untreated engine where this surface was completely eroded. This smoother surface profile played a key role in improving the airflow in the nine-stage compressor section. This, in turn, resulted in reduced FF and EGTM. Moreover, during the three monthly cleaning cycles, the accumulation of dirt and dust build up on the Nitron B treated blades was much lesser than the untreated blades, thereby descaled more easily.
Alternative Solutions to Toxic Metals
Tecvac, together with Airbus, NMB Minebea, the University of Sheffield, and the National Physical Laboratory, is working on the development of safer alternative coatings for aerospace applications. The objective of this collaboration is to create a range of PVD applied coatings to satisfy specific requirements for sacrificial protection and corrosion resistance with lubricity as an alternative solution to electroplated cadmium, a carcinogen.
Along with the new coating development, the project is also developing processes for coating stripping and reuse to achieve clean and re-surface components to extend their service life, or completely strip them to provide separate uncontaminated waste streams for recovery at the end of their service life.
Tecvac’s Collaborative Research and Development
Tecvac’s R&D department works closely with customers on custom surface treatment processes to satisfy their specific technical requirements. The unit has three PVD tools dedicated for research projects and has access to the complete line of equipment elsewhere in the plant to assess the feasibility of scaling up experimental processes in a production environment.
Conclusion
As contractors, Tecvac addresses these problems by developing innovative techniques to optimize material performance and bring the commercial and environmental outcomes demanded by the manufacturers, carriers and the market. The company serves as a bridge between prime manufacturers, university metallurgical departments, and the maintenance overhaul and repair contractors.
About TECVAC Ltd
Tecvac UK is part of the Wallwork group of companies. Tecvac Specialises in hard coatings, heat treatment, machine build, vacuum brazing and a range of other engineering services.
The Tecvac plant has facilities for thermal processing of components using vacuum Technology. The facility on the outskirts of Cambridge is split into three processing streams:
a) Vacuum Heat Treatment
b) Vacuum Brazing
c) Physical / Chemical Vapour Deposition (PVD / PECVD).
The latter involves the deposition of micro-fine coatings using specialised technologies such as Electron Beam, Magnetron Sputtering and Plasma Enhanced Chemical Vapour systems .
The Facilities include:
- Research and development with three full size PVD machines used exclusively for developing new processes and techniques.
- A dedicated carbon room where six specialised machines apply only carbon based coatings. This offers materials covering the full carbon spectrum from highly lubricious graphite to ultra-hard and resilient near diamond coating. This area also includes specialised equipment for internal pipe coating.
- A general coating area containing 6 machines where a range of PVD coatings can be applied.
- A Machine Production workshop dedicated to the design and manufacture of state of the set PVD machines
- Tecvac’s research and development department is a key driver to the company’s success. A group of experienced scientist and engineers are working on a range of external, internal and customer driven application research projects.
- Tecvac also possess a superb analytical laboratory, equipped to a level equal to or exceeding many university metallurgical departments. This enables the surface micro examination of untreated and treated surfaces and the application of tests to ensure consistency of coating and compliance to specification.
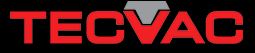
This information has been sourced, reviewed and adapted from materials provided by Composition Materials.
For more information on this source, please visit Composition Materials.