Polyurethane foam can be divided into two categories, such as open-cell and closed-cell foam. The former is a plastic with incomplete cell walls and include holes through which air and liquid can easily travel, while the latter is a plastic created of bubbles that are continuous and completely oblong or spherical.
.jpg)
Figure 1. Polyurethane foam stack. Image Credit: General Plastics
General Plastics Manufacturing, a manufacturer of rigid and flexible polyurethane foams, develops both types of polyurethane foams: open-cell flexible foams and closed-cell high-density foams. The company offers premier rigid, flexible, and self-skinning polyurethane foams that are utilized for high-performance applications by original equipment manufacturers.
Rigid Polyurethane Foams
The term “rigid polyurethane foam” includes two types of polymers such as polyurethane formulations and polyisocyanurate formulations. Depending on the manner in which they are manufactured and in the resulting performance, these polymers are distinguished from each other.
Polyisocyanurate Foams
Polyisocyanurate foams, also known as trimer foams, are insulation-grade foams that are often produced in large blocks (Figure 1) through a continuous extrusion process. These low-density blocks are then put via cutting machines to make sheets and other kinds of shapes. They are low cost, have a stiff, brittle consistency, and are made in densities ranging from .8 and 6 pounds/cubic foot. These foams usually shed dust when abraded. Although not as heavily cross-linked as polyisocyanurate materials, isocyanate foam polymers provide significant cost benefits for users.
Polyurethane Foams
Significantly different and more useful in composite constructions, polyurethane foams are made in large blocks or buns via a batch process or a continuous- extrusion process. These blocks are then cut into sheets and other shapes and can be molded into discrete part shapes.
Integral-skin Foams
Integral-skin foams, also known as self-skinning foam, combine a low-density core and a high-density skin. They can be made in a closed-mold process or an open-mold process. In the latter case, two reactive components are combined and poured into an open mold, which is then closed and the mixture is allowed to expand and cure.
Foam Density
Foam densities range from about 3 to 50 pounds/cubic foot. Depending on the foam production process, foams of the same density can differ in strength. Different manufacturing techniques demand different foam curing temperatures and chemical formulations. Integral-skin foams from General Plastics enable items like aircraft armrest padding to be easily removed from the mold in the precise shape needed or airbrushed in the preferred color.
Properties and Applications of Polyurethane Foams
General Plastics’ polyurethane foams are smooth, uniform, and grain-free cell structures that support very fine surface finishes. The products can be easily cut, shaped, and carved even with common woodworking tools. The foams can be machined or CNC-milled without producing static, and do not contain glass fiber fillers or glass-beads that can affect foam strength or damaged cutting tools.
The polyurethane sheets are dimensionally stable and do not twist, warp, or bow. They can tolerate extreme cold or heat and retain excellent strength, stability, and rigidity even at extreme heat. The sheets are highly resistant to most chemicals and solvents and do not absorb water, rot, decompose or dissolve in subgrade applications. The foams bond easily to fiberglass laminating resins, metals, etc., and can be used with adhesives, grouts, and concrete. They absorb minimal paint and can be easily finished with virtually any resin or coating system.
General Plastics’ LAST-A-FOAM series is CFC and VOC-free and does not release toxic fumes or leach chemicals into the surroundings. The materials are flame- retardant and biologically and chemically inert, and hence are resistant to fungal growth and insects.
Eco-friendly Foams
General Plastics produces high-density foam products that are environment-friendly. The products include post-consumer, post-industrial, and renewable material resources. Flexible, rigid, and self-skinning polyurethane foams are used in the aerospace, marine, defense, nuclear and other industries. In addition, they are often utilized in tooling and mold making; for protection of radioactive or explosive materials; as composite core and prototyping material; and as a wood substitute for sculptures, dimensional signs and displays.
Conclusion
General Plastics meets NQA, MIL-1-45208A and MIL-P-26541 requirements and supplies aerospace-grade foams that satisfy Boeing Company D6-82479, BMS 8-133 and FAR 25.853 specifications. The products do not degrade, oxidize, crack or change in chemical properties over time. Foam chemicals are completely mixed in large batches prior to insertion into molds and foam buns are subjected to an elaborate stress-relieving process to prevent warping or bowing.
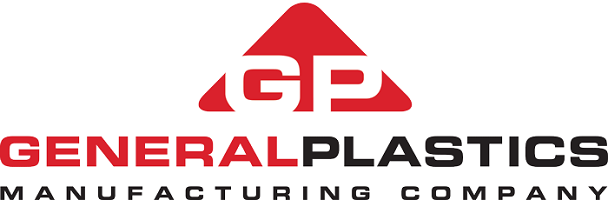
This information has been sourced, reviewed and adapted from materials provided by General Plastics Manufacturing.
For more information on this source, please visit General Plastics Manufacturing.