Thermoforming is a process which involves the heating of ArmaFORM AC grade foam core to its softening point and forcing it against the shape of a male or female mould. The AC grade is a pure thermoplastic core material to both single and double curved surfaces (Figure 1) and hence thermoforms extremely well.
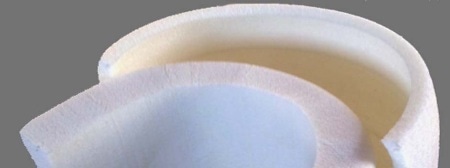
Figure 1. Thermoformed AC grade sheets in different thicknesses.
ArmaFORM AC Grade PET
Normally, foam cores cannot be used at temperatures higher than their glass transition temperature (Tg). The ArmaFORM AC grade PET core material has a Tg of around 75ºC. However, crystallization in ArmaFORM PET cores creates a crystalline structure that acts as a static system until melting starts in the crystalline phase at approximately 240°C to 250°C. It takes a significant amount of time to melt all crystalline structures at 180°C, while it will melt quickly at 240°C. This enables a range of processing temperatures for thermoforming PET cores, but it usually takes place at 200°C.
Thermoforming Methods
A wide range of thermoforming methods are available, such as drape, sweep, pressure, vacuum assisted, free forming, match mould, etc. In this article, all figures were obtained from prior production experience and testing. Normally, changes have to be made based on individual production conditions, such as thickness used, core density, and the radius in the mould.
Thermoforming Moulds
When production moulds are not available, common materials can be used to make thermoforming moulds. When working on a sample, a wooden mould out of plywood can be built to provide satisfactory performance (Figure 2).
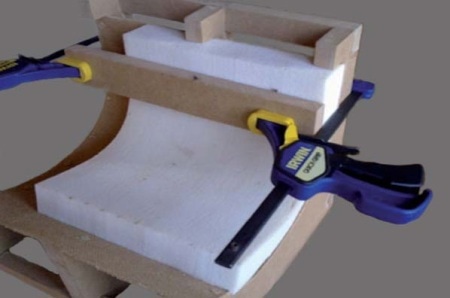
Figure 2. Simple thermoforming mould out of MDF.
However, wood poses a certain disadvantage because the heat builds up in the mould and extends the cooling time, thus affecting productivity. Plastic and composite moulds also tend to accumulate heat. For series production, aluminium or steel moulds are often preferred because they are highly stable and have greater thermal conductivity.
Single curved products having more than 400mm radius can be formed on a male mould. This can either be vacuum bagging or sweep forming. The former is a simple operation and attracts low tooling costs; however, it takes a considerable amount of time to apply the vacuum bag and the sheet might cool down below the desired level. This problem can be overcome by assembling the vacuum bag on a cold sheet and mould, and the mould can then be placed in a hot air oven.
If the radius is less than 400mm, a female mould must be utilized. The product could either be match mould or formed using a vacuum bag. Moreover, vacuum, time, and temperature should be considered to prevent creep effects.
Heating of AC Grade Core Material
The AC grade core material can be heated in a number of ways. Normally, a circulating hot air oven or a heated platen press with fixed stops is used. Infrared heaters can also be used as they are capable of heating through the thickness. A shorter wavelength reduces the temperature in the surface without major difference in core temperature, hence short IR heating should be used. Care should also be taken to reach the same temperatures everywhere in the board. Here, ARMA6 (36kW-short wavelength IR) provides a suitable option.
In all of the three cases, the temperature should be maintained within ±5°C. If the temperature increases beyond the acceptable limit, the dimension stability of the product will be affected and if it is too low, the stiffness will be high and can result in spring back and relaxation of the sheet. It is important to ensure that uniform temperature is present on both sides of the sheet so that the ArmaFORM core sheets do not warp or twist.
Dimensional Stability
Dimensional stability of the ArmaFORM AC grade will change when heated according to specified temperatures and times. If the sheets are not to be edge trimmed following the thermoforming process, care should be taken when the weld lines are oriented along the curvature line, otherwise there is a risk that the edge will not be uniform after thermoforming (Figure 3).
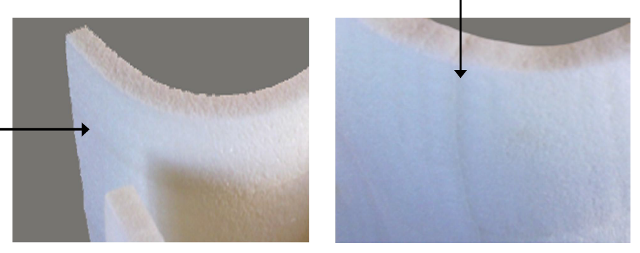
Figure 3. Thermoformed sheets with different orientation of the weld lines.
During thermoforming, the ArmaFORM AC grade is affected in two ways: decrease in density during heating due to sheet expansion, and stretching of the outer radius.
Storage of Thermoformed Core Parts
Even after 6 months of storage, the thermoformed core parts exhibit superior long-term stability with no spring back and relaxation. However, these parts should be kept within 50ºC to prevent spring back and relaxation. During transportation, the pieces should be strapped in a fixture to prevent these effects in case a temperature of 50°C is exceeded.
Conclusion
Thermoforming process can be used on ArmaFORM AC grade foam core to produce AC foam cores in 3D shape and double curve. The thermoformed core parts retain excellent stability with no spring back and relaxation even after prolonged storage.
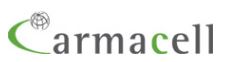
This information has been sourced, reviewed and adapted from materials provided by Armacell Benelux.
For more information on this source, please visit Armacell Benelux.