Withstanding a certain static load at a maximum deflection without collapsing is the typical requirement for a mechanical structure. However, in actual scenario, the material is exposed to repeated load cycles (fatigue). Hence, designers are also challenged with the task of estimating fatigue life.
Fatigue Test
The fatigue test involves applying cyclic loading to a test specimen to gain insights into the performance of the material similar conditions in actual use. The load applied can either be a fixed load or spectrum load, repeated for millions of times and up to several hundred times per second.
By subjecting specimens to cyclic loading at various levels of stress (S), the number of cycles to failure (N) is estimated at each level. The S-N curve is a common method to determine the time to failure for a specific material as it facilitates ranking materials and measuring the impact of the many secondary variables that influence the fatigue performance of plastics, such as thickness and frequency.
Four-Point Bending Test
Fatigue tests on sandwich structures are typically conducted with bending loads. The four-point bend test method is ideal for the purpose as it provides an almost pure shear stress in the core between the inner and outer supports. The ASTM test standard C393-00 ‘Standard Test Method for Flexural Properties of Sandwich Constructions’ defines the test set-up and requirements for static load. The same basic set-up can be applied for the fatigue testing.
Figure 1 shows the test set-up, where the sample is secured on two bearings and the load is applied at two positions, hence the four point bending test. The test begins with the definition of the static point of break to determine the maximum load. The static test is then followed by the dynamic test that involves subjecting the material at a specific stress level until the sample breaks. The number of load cycles at the break point is recorded and the same test is repeated with different stress levels to get a track record of failures by means of the S-N curve.
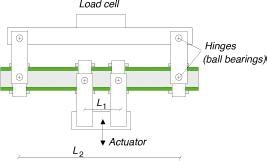
Figure 1. 4-PB set-up.
Fatigue Testing of Armacell Material
At the KTH (Department of Aeronautical and Vehicle Engineering) in Stockholm, Armacell arranged fatigue testing for its Arma-FORM PET AC foam cores. Sandwich panels under analysis were fabricated using the infusion technique by KTH with four layers of glass-reinforced polyester on each side of the panel. The test set-up of the 4-PB sandwich beam for fatigue test and typical fatigue failure mode is shown in Figure 2.
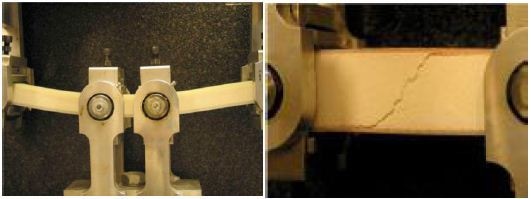
Figure 2. Test set up of the 4-PB sandwich beam for Fatigue Test and Typical fatigue failure mode.
The testing was carried out at 23°C (±1°C) and roughly 50% r.h. The loading ratio is R=0.1 (i.e., the ratio between the minimum and maximum load applied on the sample during a loading cycle). The test frequency was corrected to the load level (i.e., 2-4Hz, to avoid failure caused by local heating in the core). The load ratio selected for Arma-FORM PET AC foam cores. agrees with the value used for testing other core materials.
The common failure mode for cellular foams starts in the part of the beam between the inner and outer supports. At this area, multiple cells fail individually during the fatigue loading, creating a crack propagating at a 45° angle against the laminates.
Experimental Results
The experimental results are illustrated in the S-N curves in Figures 3, 4, and 5. Arma-FORM PET AC foam cores exhibited superior fatigue performance in relation to its static strength. As can be observed, all qualities studied can sustain millions of cycles at load levels relative to 60-70% of the shear strength.
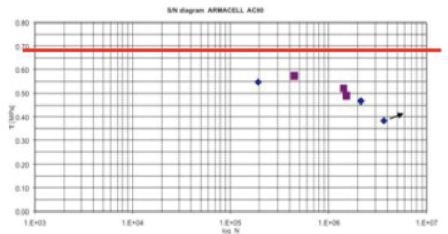
Figure 3. S/N diagram AC 80, the red line indicates approximately the shear strength.
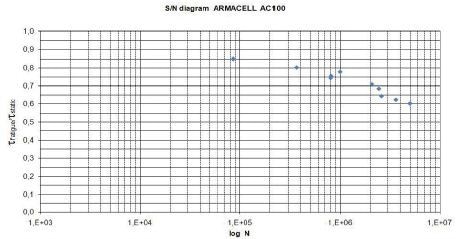
Figure 4. S/N diagram AC 100, Normalized for static shear strength.

Figure 5. S/N diagram AC 115, the red line indicates approximately the shear strength.
For structural core materials, the stress level at which the material sustains 5 million load cycles can typically be described as the fatigue threshold level. This level for PVC, for instance, is typically at 30-35% of the static failure load. Conversely, all ArmaFORM AC grade densities demonstrated a fatigue threshold level greater than 60%. Further analysis is in progress to get more information at high cycle numbers.
One test specimen, AC 100 - F10, was subjected to 5 million load cycles at 60% of the static shear strength. This test was then followed by a residual strength test, which demonstrated that the stiffness is basically the same as the ‘virgin’ material (not yet tested in fatigue). Conversely, SAN-based cores, for instance, began losing strength within a few load cycles. Moreover, the maximum load sustained in the residual test is greater than the strength test (Figure 6), but to the detriment of a lower elongation at break.
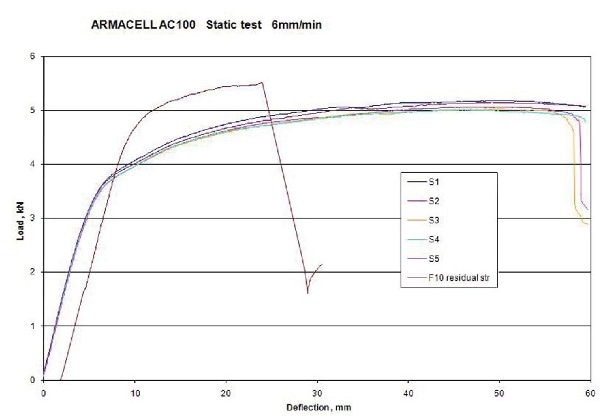
Figure 6. Static load deflection curves for AC 100.
Conclusion
The results clearly demonstrate the superior performance of ArmaFORM PET AC under fatigue shear loading. All ArmaFORM AC grade densities exhibited a fatigue threshold level greater than 60%.
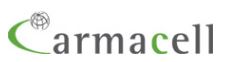
This information has been sourced, reviewed and adapted from materials provided by Armacell Benelux.
For more information on this source, please visit Armacell Benelux.