With ever increasing pressure to improve operational efficiency and reduce fuel consumption in the aerospace sector, airframe manufacturers and airlines are continuously looking for the most efficient ways to reduce aircraft weight.
One obvious way of reducing the weight of an aircraft is to look for viable substitute materials that possess the same or superior performance of traditional materials but with less mass.
Overview of VICTREX PEEK Composite Brackets
Tri-Mack Plastics Manufacturing Corporation, a molder of high temperature engineering thermoplastics located in Bristol, Rhode Island has developed VICTREX PEEK composite manufacturing capabilities to fabricate brackets for aircraft structural applications. The material was specified by Tri-Mack because of its excellent technical features and proven track record.
With respect to present fuel prices, studies have shown that by removing 1kg or 2.2lbs of weight from a short-range aircraft, annual fuel costs can be reduced by up to $100. Ralf Weidig, Victrex Composites Business Leader stated that assuming the composite brackets can remove 100kgs or 220.5lbs of weight, an airline flying around 500 short-range aircraft could save up to $5 million per year in fuel costs by adopting composite brackets.
VICTREX PEEK composites can offer up to 70% weight savings when compared to stainless steel, aluminum, or titanium. The innovative composite manufacturing process used by Tri-Mack also offers several benefits leading to faster part manufacturing cycle times compared to thermosets.
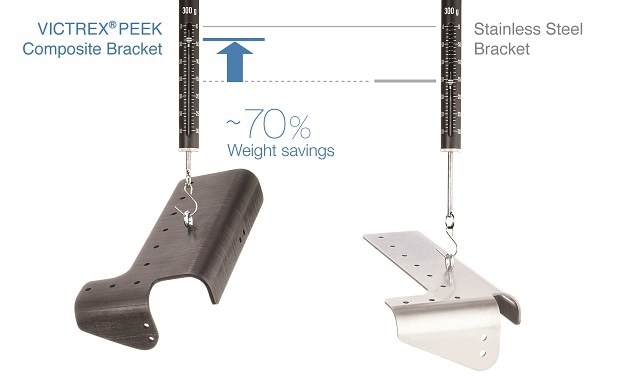
According to the Director of Sales and Marketing at Tri-Mack, thermoset composite parts take hours to be completed, however, VICTREX PEEK thermoplastic composite brackets have manufacturing cycle times measured in minutes.
That speed along with the ability to recycle the material for other applications enables a whole new level of processing efficiency that cannot be achieved with thermosets.
Component lifetime is also a key consideration. VICTREX PEEK thermoplastic composites offer chemical and corrosion resistance to hydraulic fuel, jet fuel, de-icing solution, salt, steam, water and other commonly used service fluids that can influence metal longevity.
VICTREX PEEK composites are capable of offering between four and five times higher fatigue strength, specific stiffness, and specific strength when compared to traditional metals such as aluminum. They can also provide vibration and noise dampening improvements as well as extraordinary mechanical properties making them an attractive and viable solution for engineers looking to replace heavy metals and thermosets.
Advantages of VICTREX PEEK-based Composites
- Up to 70% weight savings while maintaining equivalent strength and stiffness
- Simplify, standardize and consolidate parts for up to 75% quicker assembly times
- Dimensionally stable and shows very good resistance to moisture and creep fatigue
- Very good resistance to jet fuel, hydraulic fluid, de-icing solution, insecticide, cleaning fluids, extinguishing chemicals, water, salt, and steam
- UL94 V-0 rated with low smoke and toxic gas emissions
- Proven track record with over 15,000 aircraft relying on VICTREX PEEK solutions.
Conclusion
Aerospace engineers are looking for lightweight, yet strong materials that offer the freedom to simplify part designs, reduce system costs, and provide durability in harsh environments. Victrex is the world leader in value creation through high performance polymeric solutions with 35 years of experience in displacing metals, thermoset composites, and other plastics in the aerospace market.
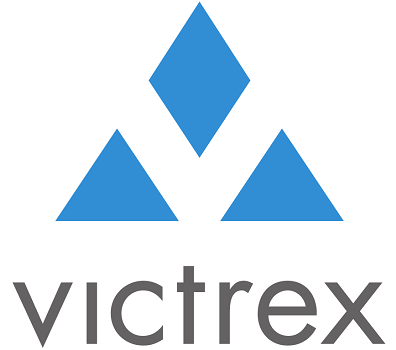
This information has been sourced, reviewed and adapted from materials provided by Victrex.
For more information please download the full brochure from Victrex.