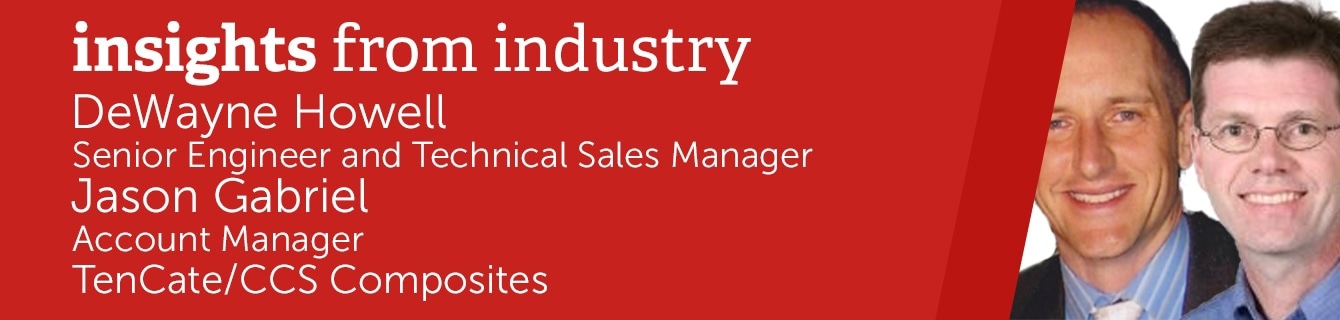
AZoM talks to DeWayne Howell and Jason Gabriel (Technical Engineering TenCate/CCS Composites), about the process of compression molding for composites and what the benefits and applications of this are.
There are many different fabrication processes used to create advanced composite parts - could you give us a description of the compression molding process employed by TenCate/CCS Composites?
There are indeed many different ways to fabricate a part using composite materials. Compression molding is the process we use at TenCate/CCS Composites. We can mold parts that are very small or over 5 feet (1.5 meters) in length, with thicknesses as thin as 0.050 inches and well over 1” (25mm). We mold both thermoset and thermoplastic composites.
In general there are 4 key steps to the process. Note that this is for the more common thermoset composite. Thermoplastics are similar, but we can discuss them in more detail later.
First, in order to mold a part, a high strength metallic tool is machined to the exact dimensions needed to produce the part shape, with some adjustments for shrinkage. The tool consists of a cavity and a core. The cavity defines one side of the part, the core defines the other side of the part, and the void in between these two tools or mold halves is the volume of the composite part to be formed. The tooling is installed in a press and is integrally heated so that the temperature can be controlled throughout the part molding cycle.
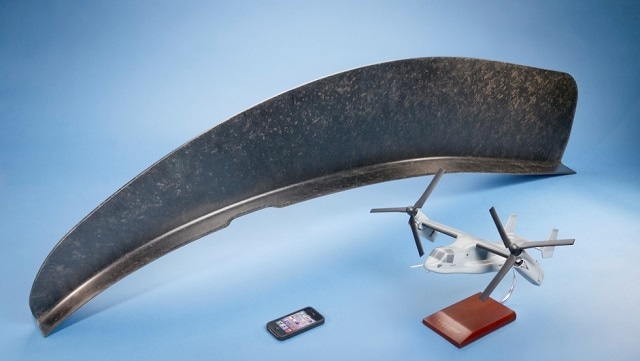
Example of a large compression molded part used on the V-22 Osprey helicopter. ( 60 in length x 8 inch base, and 12 inches height 152x20x31 cm). Image credit: TenCate
Second, the fiber reinforced resin material is pre-formed to the shape of the tool. Preforming is important; there are several methods that can be used and a specific method for a specific part shape can improve part performance.
Third, the pre-form is transferred into the heated cavity of the tool and the tool halves are closed in the press under very high pressures ranging from 800 psi to over 2000 psi (55-138 bar) depending upon material type and part thickness. The tool remains closed for a set period of time based upon the given material. This allows the resin material to melt and flow within the tool, thus completely filling the void between the two mold halves before solidifying.
Fourth, and finally, the pressure is released and the part is removed from the tool. At this point there may be a small amount of resin flash around the edges that needs to be removed, and the part is finished.
What would you consider to be the main advantages of fabricating parts by compression molding?
There are a host of advantages when it comes to compression molding. First of all, just for reference, advanced composites in general offer many advantages compared to metal parts, including lighter weight, high strength, high stiffness and corrosion resistance, depending upon the type of composite material. But, I would have to say that the top 5 advantages across the board when compared to metals and other composite fabrication methods are:
- Part complexity
- Ease of replacing metal by nearly matching the metal part geometry
- The ability to add inserts and rib stiffeners
- Dimensional control and stability
- Lower finished part cost with the ability to make high volumes of parts
Part Complexity -Being a molded part, one can almost think in terms of part complexity to that obtainable with injection molding - almost. Plastic injection molding is capable of very complex geometries whereas typical laminated composites are restrictive in geometric complexity. Compression molding allows for very long fibers, on the order of 1 inch or more, to be integrated into a complex shape. And, our compounds generally offer much more fiber content. Longer and more fibers provide a much stiffer and stronger material than the shorter/fewer fibers found in injection molding materials. Offering a complex shape with these higher mechanical properties is something that neither injection molding nor traditional laminated composites fabrication methods can do, making compression molding an excellent middle ground between the two. Take for example the helmet optical support structure we fabricated (see photo). The complexity shown here is incredible, yet with long fiber reinforcement and a very high volume of fiber.
Replacing Metal - The fact that we can mold very complex parts means that it's possible to take a part designed for metal and more easily convert it to a compression molded part with little need for geometry changes. This just isn't possible with traditional laminated composite methods without also requiring a lot of post fabrication machining. And, by nearly matching the metal part geometry, it's possible to drop-in and replace the metal part without interface issues.
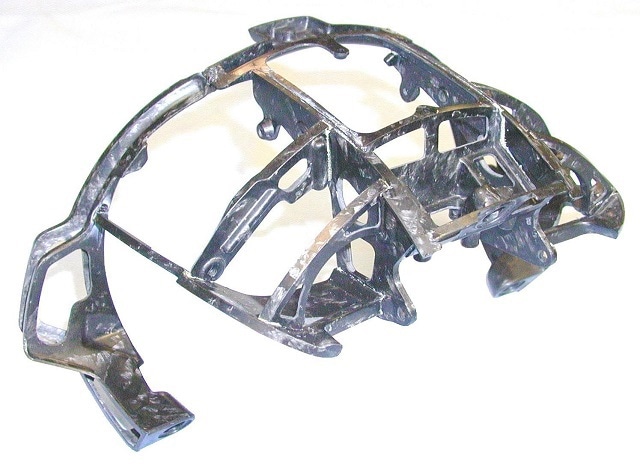
F-35 Helmet Optical Support Structure. Image credit: TenCate
Adding inserts and reinforcement ribs – This is another advantage of compression molding. Metallic or other material inserts can be placed into the mold at the time of forming. These attachment hard points eliminate common secondary processes compared to other composite manufacturing methods. Also, by incorporating ribs into a part, which is easily done by simply adding such a feature to the tool, the bending stiffness and strength can be increased dramatically, with little if any change in part cost. It isn't all that easy to incorporate ribs into traditional laminated composite parts. As an added feature, we can also easily add a galvanic glass surfacing layer or a conductive lightning strike mesh to the outer surface of the part.
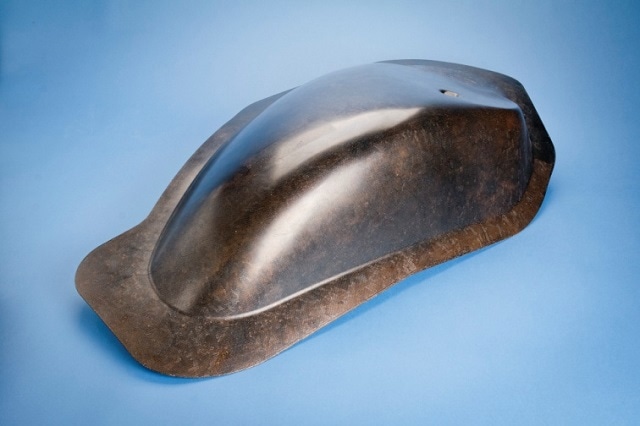
A FLIR display fairing with a copper lightning strike screen integrated into the part surface. Image credit: TenCate
Dimensional control and stability – This is enhanced by the matched metal tooling used in compression molding. Each part produced from the same tool is basically a dimensional duplicate of the previous part. Other composite fabrications processes rely on a soft material to form one side; causing dimensional variation and then additional machining. While compression molded parts can be machined, it is usually reserved for extremely high tolerance areas or the few part section areas that will not be molded directly because of additional mold complexity.
Lower part cost - The finished part cost can be lower than expected. It is not uncommon for TenCate/ CCS Composites to produce a complete complex shaped part in only 5-15 minutes. In addition, the ability to incorporate otherwise secondary features and inserts, reduce labor content, produce low material scrap, achieve high part yields and reduce part inspection time can all attribute to cost savings. Some customers have chosen to replace several assembled, simple shaped parts with one complex compression molded part. This allows for savings in assembly time and the inventory of multiple parts as well.
What types of composite material can be compression molded and are there preferred forms of these materials?
Most fiber types can be compression molded including fiberglass, aramid, standard modulus carbon fiber and every other grade of carbon fiber. When it comes to resin, two general categories are used: thermoset, like epoxies and cyanate esters; and thermoplastics, like PEEK and PEI.
Thermoset composites are the most common materials used at TenCate/CCS Composites. TenCate’s compression molding materials have been specially formulated to give just the right viscosity, at just the right temperature, for just the right amount of time during compression molding. Other suppliers use resins that are “standard” and not specific to compression molding.
Thermoplastics are a relatively new capability and we mainly use PEEK, PPS and PEI fiber reinforced materials, but others are also available. TenCate offers a broad product line of high quality thermoplastic prepregs that can be made into a compression molding material; from lower temperature resins like HDPE up to high performance polymers like PEEK. TenCate is one of the world’s leading companies in high performance thermoplastic composite materials.
CCS Composites molds both “sheet molding compounds” (SMC) and “bulk molding compounds” (BMC). Both mix chopped fiber and a resin, but in different ways.
Sheet molding compounds consist of chopped fibers and resin mixed to form a sheet. Preforms are then cut from the sheet and the leftover sheet is discarded. Or, sometimes the sheet can be rolled or stacked and waste is reduced. Some SMC is made of very high quality chopped unidirectional tape; some is more of a general mixture of chopped fibers and resin.
The preferred material form we use is bulk molding compound. BMC’s represent a well mixed, high quality, unidirectional tape that is pre-impregnated with resin specifically for compression molding. It is then slit and chopped, usually on the order of ½” inch up to 2 inch in length. The fiber contents are relatively high at about 50% by volume and sometimes much more. We have found our custom resin, high fiber volume, mixed with a very high quality prepregging technique produces a very high quality molding compound.
When molding with these materials the fiber orientation is somewhat random and takes on a generally quasi isotropic characteristic in the flat plane of the part. But, it is also possible to orient the fibers or lay in some fabric or continuous fiber material during the pre-forming stage to create a hybridized material with more directionally dominant fiber angles to provide higher stiffness and strength in specific directions and areas.
Could you go into more detail regarding the chopped fiber bulk molding compounds?
Sure. Perhaps the best way to do this is to compare the material to something everyone is familiar with, aluminum alloy, specifically 6061-T6 aluminum. TenCate/CCS offers about 7 grades of thermoset BMCs. Depending upon the carbon fiber used, the resulting modulus of elasticity can be between 60% and 200% of 6061 aluminum. Tensile strength is pretty much equivalent to aluminum for all of the fiber grades, but flexural strength can be greater. The real benefit comes when we compare the specific strengths of the materials.
Specific strength takes into account the density of the material and is a measure of the delivered strength per unit of material weight, which is important to any structure that needs to be lightweight. For example, the specific tensile strength for the MS-4H BMC grade of material is 190% that of aluminum, 230% of steel and 130% of titanium. This table (see attached) summarizes these comparisons.
Table 1. BMC Material Comparisons. Image credit: TenCate
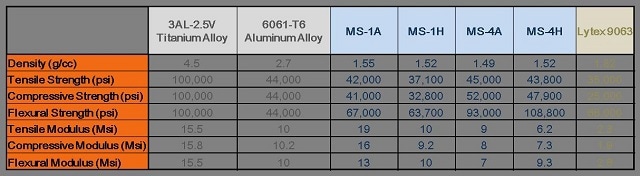
Comparing chopped fiber BMCs to other continuous fiber composite materials, the continuous laminated composite material will always deliver higher strength, at about 150% of BMC. However, when we compare BMCs to continuous laminated composites that include cutouts and holes for attach points the difference in strength is greatly reduced. As an example, on a typical aircraft there are hundreds of cutouts for access panels and there are thousands upon thousands of connections and fastener points. It's common for composite aircraft to be designed based upon an "Open Hole" tensile and compression strength, rather than pristine (no holes) laminate strengths. The Open Hole strengths account for all of those cutouts and attach points and effectively knocks down the strength of the laminated composite.
For BMC materials, the Open Hole strength and the pristine material strength are essentially the same. In fact, Open Hole strength for the BMC is pretty much the same as the Open Hole strength for the laminated composite. So, in parts where cutouts and holes will be present, the BMC compression molded part can give strengths equal to a laminated composite part.
The choice of resin material is another critical factor for BMCs. Our high performance thermoplastic BMCs will produce a part that has excellent flame, smoke and toxicity characteristics, making them ideal for aircraft structures and aircraft interiors. In thermosets, cyanate ester thermoset resins have extremely low out gassing attributes, and epoxies can also have acceptable outgassing, which is important for space based structures. Operating temperatures differ for the various resin systems and can range from 250◦F (120◦C) to over 500◦F (260◦C) depending upon operating loads. All-in-all, BMCs are an excellent candidate for metal substitution and can even rival continuous laminated composites is certain applications.
The rib forming capability you mentioned earlier sounds interesting, do you have an example of a part that includes ribs?
It's a relatively straightforward thing to add ribs to compression molded parts. Because of the high forming pressures involved the BMC material readily flows into cavities in the mold as the viscosity of the resin decreases with temperature. Not only does the resin flow into a rib cavity but fiber flows as well, thereby producing a fiber reinforced juncture at the plate to rib interface.
The function of a rib is to add stiffness and strength to the part. Compared to a flat plate, a single rib that adds only 15% to the part weight can increase the part bending stiffness by over 700%. This chart shows the kind of stiffening that can be achieved in compression molding with only a minuscule increase in weight, and therefore cost.
Table 2. Stiffness Increase with Minimum Weight. Image credit: TenCate
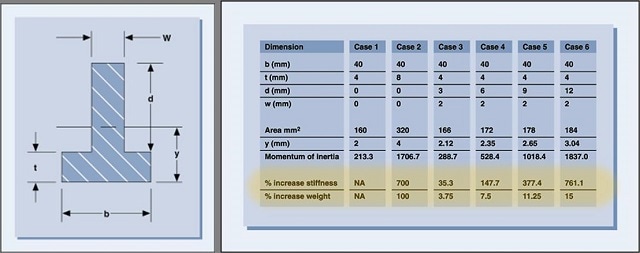
An excellent example of this is an access cover that TenCate/CCS fabricates for the V-22 rotorcraft. Originally the cover was a laminated composite with a honeycomb sandwich core. The core material is effective at separating the two face sheets of the panel which, like ribs, increases the bending stiffness of the cover while adding minimal weight. Sandwich panel composites have several inherent challenges.
Fabrication requires the use of an adhesive to bond the face sheets to the core and there is a propensity over time for the panel to trap water in the voids of the honeycomb. These two issues alone add cost and maintenance to the cover. It is a long process to cut, assemble, vacuum bag, then autoclave cure the panel.
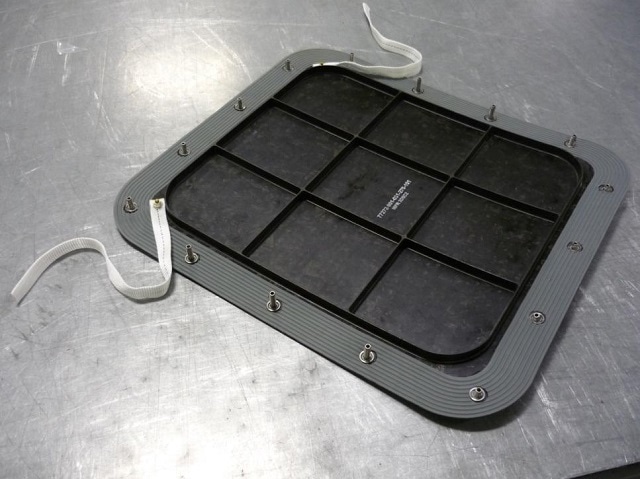
V22 Compression Molded Cover. Image credit: TenCate
TenCate/CCS redesigned the cover to be a single sided, compression molded face sheet with molded-in stiffening ribs. The redesign resulted in a compression molded part that can be fabricated faster and eliminated the need for expensive honeycomb material. Additionally, lightning strike mesh is incorporated as an added layer to the face sheet during molding.
The material molds so quickly that in comparison; the CCS Composites part is finished, while using the old part design, the raw materials were still being cut to shape well before assembly and molding. Lower cost and less maintenance was a definite win for this V22 cover application.
Earlier you mentioned that you can mold parts using fiber reinforced thermoplastic materials and not just thermosets. Are there any differences in the compression molding processes between the two and are there any distinct advantages?
Yes. Thermoplastic compression molding is a relatively new technology at TenCate/CCS. Compared to thermosets, our high performance thermoplastics generally offer superior FST (flame, smoke and toxicity) performance, lower heat release rates (OSU), excellent durability and impact characteristics, high solvent resistance and faster processing speeds. You can see that these benefits of thermoplastics readily lend themselves to aircraft applications.
Compression molding of thermoplastic BMCs requires a slightly different process. Since thermoplastics simply melt instead of crosslink like thermosets, it is important to have tighter controls on the temperature of the material during compression molding. To facilitate this we've developed a proprietary process called, "Xpress". Essentially the Xpress technology allows for us to independently control the temperature of the thermoplastic at many different locations within the mold. And, unlike thermoset compression molding, we can raise and lower the temperature of the part being formed much more quickly. Compared to many other thermoplastic compression molding processes, Xpress offers faster cycle times, reduced part warpage and reduced defects overall, leading to lower costs. And by monitoring the temperature in so many areas during molding, quality and process consistency is improved.
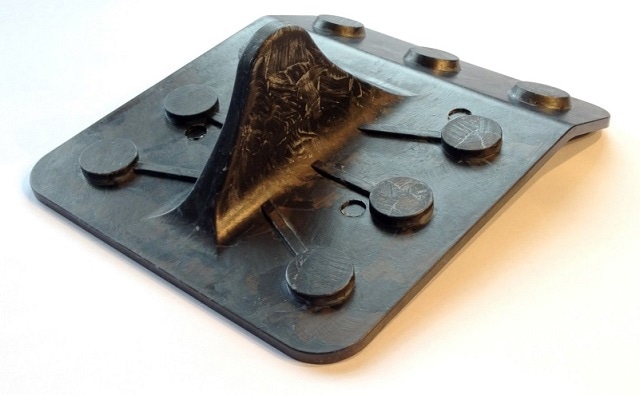
Carbon Fiber/Thermoplastic Bracket. Image credit: TenCate
What are the main applications you are currently seeing for compression molded parts?
TenCate/CCS has been around since 1994 and has worked in many industries. Currently we are generally seeing that about 50% of our parts fabrication business is for aircraft, 25% for space and the remaining 25% in miscellaneous commercial applications. Aircraft applications range from various clips and brackets, to many different covers and access panels, to wing fences and missile components. Space applications also include various brackets, truss tube end fittings and even major load bearing structures on launch vehicles.
Commercial applications center around interiors for aircraft and include structures like trays and panels, but interest is also gathering in the oil and gas industry related to ground exploration hardware. Anywhere complex shaped parts are needed, where injection molding materials do not offer enough mechanical performance, and the weight, cost and corrosion of metal shapes is a concern, we have seen success.
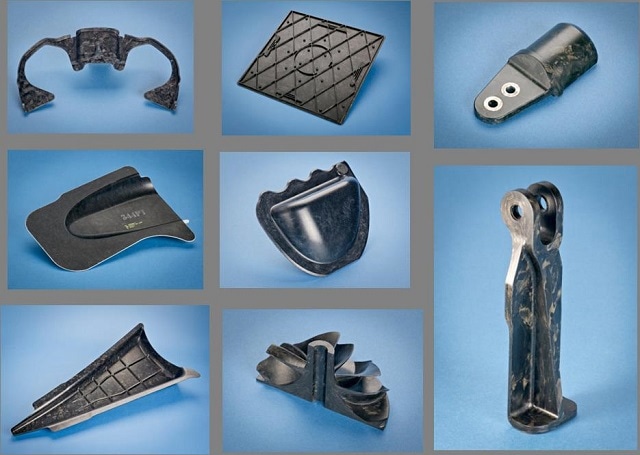
Compression Molded Parts. Image credit: TenCate
What does the future hold for TenCate/CCS composites and do you see any major breakthroughs on the horizon?
Aircraft and space will continue to be a major source of applications for compression molded composite parts. As these materials continue to show their value in performance and cost, qualified BMC materials continue to be selected for more complex shapes on existing and new programs.
Perhaps an even bigger potential for part fabrication is that of thermoplastic parts for the aircraft industry. Since thermoplastic parts have ideal benefits for aircraft, like FST and durability, we expect to see our business grow substantially in this arena. We also see our thermoplastic Xpress technology opening doors to higher volume commercial parts fabrication. With the increased speed of part fabrication that Xpress delivers we can be more price competitive and part delivery enabled. That allows these materials to be used to replace lower cost, and lower performing materials, like castings and injection molded parts.
As TenCate Advanced Composites is primarily a materials company with a wide range of thermoset and thermoplastic products, CCS Composites will continue to have first access to new advanced compression molding materials and the knowledge learned in developing them. It also offers direct supply and support for material and molding from one company. Visit us at www.tencateadvancedcomposites.com.
About DeWayne Howell & Jason Gabriel

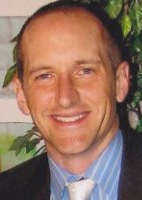
DeWayne Howell is currently a senior engineer and technical sales manager with TenCate's CCS Composites division. DeWayne has been working in the composites business for 28 years for companies such as NASA, ATK and several small companies, including his own, Peak Composites, Inc., where he developed and marketed the CompositePro composites engineering software package.
His work has focused on the design, analysis and development of composite structures for both thermoset and thermoplastic based composites in a wide array of applications. He holds a degree in Aerospace engineering, is a director of the Rocky Mountain SAMPE chapter, and has authored ten technical papers in the field of composites.
Jason Gabriel is an Account Manager for TenCate/CCS Composites, serving the eastern side of North America. Jason represents TenCate’s “CCS Composites” business, which specializes in the compression molding of advanced composite, complex shaped, thermoset or thermoplastic parts.
Jason has spent the last ten years in various R&D, engineering, manufacturing and sales roles within the advanced composite industry. He has a degree in Mechanical Engineering from The Pennsylvania State University.
For additional technical information, please contact TenCate by email at [email protected].
Disclaimer: The views expressed here are those of the interviewee and do not necessarily represent the views of AZoM.com Limited (T/A) AZoNetwork, the owner and operator of this website. This disclaimer forms part of the Terms and Conditions of use of this website.