High-performance motorsports are extremely demanding, often requiring high-tech carbon fiber part modifications with very little advanced notice.
Complex on-screen designs are manufactured and supplied to the track before being immediately installed, with certain teams requiring parts to be manufactured from designs and delivered in under 45 hours. This is made possible thanks to the tooling used.
Carbon fiber parts are generally molded in an autoclave (essentially a high-pressure oven) under pressures up to 6 bar and at temperatures between 120 °C and 180 °C. The mold utilized in shaping the part should be made from a material that is capable of performing in these challenging conditions.
If accuracy is to be maintained, the mold must also be able to accommodate the part’s thermal expansion. To achieve this, the mold is generally made from carbon fiber - the same material as the parts it is molding.
High-performance motorsports tend to rely on carbon fiber parts crafted from prepreg. Prepreg is a combination of carbon reinforcement in unidirectional or woven form that has been impregnated with a specific amount of resin - usually epoxy. Toray’s AmberTool® HX56 product is at the forefront of this particular market.
A prepreg requires appropriate time, heat, and pressure in order to cure the resin and create a finished laminate.
To assemble the part, a series of pre-cut prepreg pieces are combined into a negative-shaped mold. This is processed in an autoclave, and the newly formed positive part is removed. Before any of this can take place, however, the mold must first be created, and being able to rapidly produce this mold is essential.

Image Credit: Stephen Barnes/Shutterstock
Mold Production
To produce the mold, the tooling prepreg is first laminated on the master/pattern, resulting in a mold thickness of approximately 5 to 6 mm. This is initially cured at a low temperature (typically 55 °C to 60 °C) on a master/pattern in order to maintain accuracy. It is then post cured to higher temperatures (up to 200 °C) in a freestanding state.
Production time must be minimized. The chart below provides an overview of a typical production process, highlighting how an initial curing time of 8 hours and a post-cure time of 20 hours actually account for 63% of the 45 hours required to fully produce a part.
With this in mind, the processing time for the mold materials must be kept as low as possible while ensuring that high surface quality is maintained.
A typical process route for a complex 1 m2 part would include the following steps:
- Design verification: 2 hours
- Master pattern production: (a positive shape representing the ultimate component shape): 3 hours
- Carbon fiber mold lamination on the master pattern using AmberTool® HX56: 4 hours
- Initial mold cure (HX56 55 °C cure = total time in autoclave): 8 hours
- Mold finishing and post-curing: 20 hours
- Carbon fiber part lamination: 1 hour
- Carbon part curing (total time in autoclave): 6 hours
- Final part finishing and trimming: 1 hour
- Delivery
These steps result in a total production time of 45 hours. It should be noted that in instances where performance characteristics of the final part do not necessitate such a high specification, cure times may be reduced to cut total production time by up to 10 hours.
Thanks to their ease of use and their capacity to deliver unparalleled quality surface finish, Toray’s AmberTool® series tooling prepregs are true ‘tools for speed,’ and ideal for use in today’s highly demanding market
The AmberTool® series is manufactured at Toray’s thermoset center of excellence in Langley Mill, the U.K., and the company’s products have a long, proven history of reliable quality service. From September 2020, AmberTool® HX56 is also available in the U.S., enabling rapid delivery to the North American high-performance motorsport markets.
Using AmberTool,® high-performance industries such as Formula 1 teams are able to deliver newly designed parts to their required destination in under two days.
Acknowledgments
Produced from materials originally authored by Jed Illsley from Toray Advanced Composites.
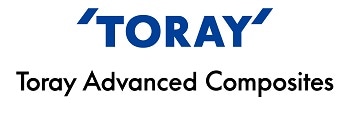
This information has been sourced, reviewed and adapted from materials provided by Toray Advanced Composites.
For more information on this source, please visit Toray Advanced Composites.