The challenge faced by Bose was to measure dynamic material properties for optimization of sound performance in Bose products.
Background
Bose has a strict quality assurance program whereby it is able to produce the highest quality products. The main advantages of a good QA program includes consistent production of materials that produce the best sound quality, reduced costs from post-production customer support, and especially for Bose, an excellent reputation.
Bose ElectroForce testing instruments have been used recently to help design, optimize, and produce high-quality passive radiator materials within the Bose SoundLink® and SoundLink Mini Bluetooth® speaker products.
Material testing capabilities offered by Bose ElectroForce test instruments have helped produce never-before-seen sound quality output by these compact and portable speakers. In several cases material properties are variable characteristics that can be measured, optimized, and controlled to create and help consistently produce the highest quality products. Bose discovered that quantitative, dynamic, time- dependent properties of materials used in Bose speaker technologies directly correlate with acoustical sound quality.
Along with its patented linear motor technology, Bose ElectroForce test instrumentation is key part of the Bose QA program for the SoundLink and SoundLink Mini product lines with capabilities to quickly, precisely and easily measure such dynamic material properties.
.jpg)
Figure 1. Optimizing sound performance in Bose products (Take image on page 1- all together)
Experimental Setup and Tests
The Bose speakers use passive radiators, which are made of a proprietary silicone-based material and it was observed that by controlling the dynamic material properties of these components an unmatched sound quality is created with optimized acoustical performance. Dynamic material properties of these passive radiators are monitored accurately using Bose ElectroForce testing instruments as part of the Bose QA program.
Software and test fixtures were customized to meet data output requirements and testing needs for a complete QA solution as shown in Figure 2. Figure 3 shows a representative plot of sound quality (performance) versus quantitative material properties found using Bose ElectroForce instrumentation. In order to pass QA inspection, material properties must fall within specification.
.jpg)
Figure 2. Custom test fixture used for QA testing of Bose® passive radiator materials used in SoundLink® and SoundLink Mini portable Bluetooth® speaker products on Bose ElectroForce® 3220 test instrument.
.jpg)
Figure 3. QA requirements for material properties by Bose ElectroForce instrumentation
Summary
Bose ElectroForce materials testing instrumentation is used by researchers for bringing the best products to market. The complete QA solution includes push-button, technician-level instrument operation with automated pass/fail reporting reducing operator costs. Figure 4 shows an outline of a QA process. This kind of QA program is used by Bose to optimize materials used in popular consumer products, including the Bose SoundLink® and SoundLink Mini portable Bluetooth® speakers.
.jpg)
Figure 4. Example Design Methodology for QA Process
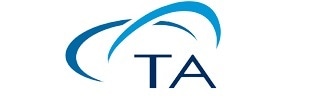
This information has been sourced, reviewed and adapted from materials provided by TA Instruments.
For more information on this source, please visit TA Instruments.