Harper understands how important research and development is for the scale-up of advanced materials. Using the vast experience in thermal process research and development programs, Harper partners with its customers to ensure success as operations are scaled up through process development, optimization and piloting. Clients are offered access by Harper to several research facilities to help in developing a highly efficient and effective regime to meet their goals.
The research centers of Harper are:
- Technology Research Center – Harper Headquarters, USA
- Partner Research Facility – Oak Ridge National Laboratory, USA
- Partner Research Facility – UDRI, OH, USA
- Partner Research Facility – Carbon Fiber Pilot Line, Portugal
Technology Research Center – Harper Headquarters, NY, USA
A large number of companies have used the technology research center for process optimization and process development as they work toward commercial scale-up or with systems requiring unique process specifications. It is possible for customers to use a number of on-site thermal systems to gather data and fine tune their processes, with a focus on varying production rates, temperature regimes, processing times, atmosphere compositions, and flow rates. This results in savings on the investment ultimately required for new thermal processing systems.
Harper has a wide range of thermal systems capable of handling the process conditions. Furthermore they have the ability to make modifications to tailor the existing pilot equipment to specific customer process requirements.
The company’s onsite range of equipment includes:
- Batch or continuous furnaces
- Sizes from small kilns to large furnaces, with 3 temperature zones
- Furnace conditions from atmospheric to nitrogen or specialty gases, with temperatures up to 2500°C
Along with thermal systems, Harper offers sophisticated laboratory equipment to help transfer the technology from the lab to the global marketplace.
The company’s range of lab testing capabilities includes the following:
- SEM/EDX
- surface area measurement
- electron microprobe
- DTA and TGA
- qualitative and quantitative powder XRD
- thermal diffusivity
- high temperature XRD
- dilatometry
- particle size analysis
- thermal and elemental analysis
.jpg)
Figure 1. Research and Pilot Facilities
Due to their experience in the testing and feasibility stage, many customers work with Harper to conduct in-depth studies to determine equipment requirements and help define process parameters for optimal plant design to assist with technical and business strategy and financial planning. The company’s vast capabilities in thermal processing engineering studies include, but are not limited to:
- process cost models
- economics of increased production capacity with current and future state technologies
- analysis of best-suited thermal process technology system for new material innovations
- identification of opportunities for improved product quality and cost reduction
- investigation of solutions for transition from batch to continuous processing
- engineering of material handling solutions for unique processing systems
Partner Research Facility – Oak Ridge National Laboratory, USA
Oak Ridge National Laboratory is home to the Department of Energy’s Carbon Fiber Technology Facility. As part of the Energy Efficiency and Renewable Energy (EERE) program office, this 42,000sq. ft. innovative technology facility is a national test-bed for government and commercial partners to scale-up emerging Carbon Fiber technology. Harper International manufactured this 390-ft long processing line at this DOE facility and is ideal for carbon fiber research and development. Custom unit operation configuration can be done and has a capacity of up to 25t/year, or 4.3kg per hour, enabling the industry to validate conversion of the Carbon Fiber precursors and semi-production scale. The facility aims to be a collaborative research center and is designed as one of the most sophisticated and capable lines in the industry. Clients can gain all of their testing and piloting needs with the Carbon Fiber line’s extensive capabilities including:
- Rated capacity 25 t/year based on 24k PAN tows
- Configured for PAN, polyolefins, lignin, and pitch precursors; Upgradable for rayon and high modulous carbon fibers
- Designed for 3k to 80k tows and web up to 300x12.7mm loft
- Oxidation temperature to 400°C with airflow configurable for parallel, cross or down flow
- High-temperature carbonization to 2000°C
- Low-temperature carbonization up to 1000°C with capability to produce structural or micro/nano-porous fibers
- Post-treatment system designed for compatibilizing fibers with performance or commodity resins
Partner Research Facility – OH, USA
Harper partnered with the University of Dayton Research Institute to offer the clients access to additional innovative R&D systems. The UDRI Multiscale Composites and Polymers division operates an industrial scale, continuous process high temperature Pusher style furnace manufactured by Harper. Materials are placed on a tray or loaded into graphite boats which are placed on the track system and “pushed” through the hot zone of the furnace under an inert atmosphere. The benefit of pusher furnaces compared to a conventional batch oven is that the time consuming process of heating up and cooling down the furnace is avoided, resulting in a dramatic reduction in cost and an increase in process uniformity.
Advanced materials can be tested in this facility, which has the following capabilities:
- Maximum temperature: 2500°C
- Purged nitrogen atmosphere
- Maximum part size is 19 in. x 19 in. x 3 in
- Adjustable residence time at temperature, varying from 30 minutes to 6 hours
Partner Research Facility – Carbon Fiber Pilot Line – Portugal
Harper offers its complete carbon fiber pilot process line at a partner’s facility in Lavradio, Portugal as an open reference and capabilities demonstration to select Harper clients. Harper’s proprietary multi-flow oxidation ovens, advanced LT and HT slot furnaces rated for 800°C and 1800°C respectively, surface treatment and waste gas abatement systems, and winders are included in this facility.
In the Carbon Fiber Pilot Line, Harper clients can utilize the facility for validation of their carbon fiber process, confirmation of material quantities to enable downstream research, assessment of feasibility of continuous operations and validation of design parameters for further scale up.
.jpg)
Figure 2. Full production scale product lines
About Harper International
Harper International is a global leader in complete thermal processing solutions, as well as technical services essential for the production of advanced materials.From concept to commercialization, from research scale to full production line operations, Harper is perpetually on the cutting edge. For decades, they have pioneered some of the world’s most innovative, customized systems, with a focus on processing materials at high temperatures and in non- ambient atmospheres.
Harper’s value proposition is unequaled — decades of industry experience, a highly specialized, multi-talented group of employees, and a passion for partnership. They don’t shoehorn a standard line of products to fit their customers’ requirements. They specialize in first-of-a-kind solutions using our exceptional depth and breadth of knowledge. Harper’s culture is one of genuine ingenuity and creativity, which ensures they are constantly challenging themselves to craft the best-engineered technology solution for their customers’ unique thermal processing needs.
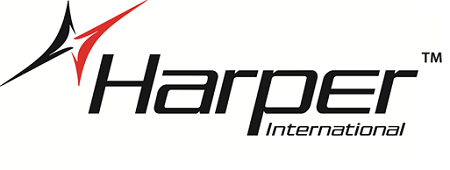
This information has been sourced, reviewed and adapted from materials provided by Harper International.
For more information on this source, please visit Harper International.