Different materials are used to make packaging in various shapes depending on the products it is intended to protect. Some forms of packaging include sealed bags to maintain the freshness of food, bottles for beverages, and biomedical packaging to keep products sterile (Figure 1). A series of material tests needs to be performed to determine the ability of the packaging to deliver the intended function.
.jpg)
Figure 1. Different materials are used to make packaging in various shapes depending on the products it is intended to protect.
Testing of Bottles
Bottles for juice, soda, and water are available in different sizes and shapes. They are tested for structural rigidity to ensure that they won’t experience any crack when filled or fold over when stacked. They are also subjected to burst testing to identify the point of failure when filled with fluid. Dimensional measurements are preformed to ascertain trouble-free passing of bottles through production lines. Structural integrity is ensured by checking consistency through thickness measurements at various points.
Since bottles are often shipped on pallets and stored by placing them on top of each other, it is necessary to perform a top-load test to assess their rigidity and identify their ability to withstand stacking forces. These tests are normally performed on a digital force tester equipped with compression platens to exert a force on the top of the bottle.
The tester is programmed to move its crosshead down depending on the bottle height so that it will apply a force low enough to make contact with the bottle top. The next step involves compressing the bottle down to a set displacement point and recording the force reading at that point. Initial bottle height and force reading at that displacement point must lie within a tolerance range prescribed by the quality department to give assurance to the users that the bottles deliver the desired function for the fluid they hold.
Testing of Seals
The seals applied on packaging for cereal, potato chips, cookies, and yogurt are thoroughly tested to ensure their ability to deliver the desired performance. These seals may be pressure sealed or adhered together. If the seal used for sealing the bag material is much stronger than the bag material, the bag rip open despite the seal, causing the food to fall out of the bag. The strength of the seal is determined by peel testing, which involves pulling the seals apart. This test provides valuable data to determine the bag’s structural integrity during the application of forces.
Peel Tests
Different types of peel tests are available and provide different results. A testing system like the Lloyd LS1 testing machine is required to perform the peel tests. A common test involves cutting a strip four inches long and one inch wide with the in the middle. This testing procedure is called a T-Peel. The ends are secured in the grips to pull the sample apart at a preset test speed, thereby allowing the material to be pulled apart uniformly. Average Peel and Maximum Force are the common results. Average Peel is also termed Seal Strength or Peel Strength.
Burst strength testing is performed to evaluate the integrity of the entire bag. It involves compressing the sealed bag between two platens and taking maximum force reading before bursting. This test ascertains that the products remain fresh and are not ruptured by the force exerted during stacking or packing together of the bags. Packaging testing with the Lloyd Material Tester is illustrated in the following video:
Packaging Testing with the Lloyd Material Tester
Conclusion
This article presents only some of the examples of the packaging tests to protect the packaged products, to keep their freshness, or detect the expiry date usually printed on the package.
About Lloyd Instruments
Lloyd Instruments designs, manufactures and is a recognized world supplier of universal materials testing machines and polymer test equipment. Also suppliers of the Chatillon® range of force gauges and force measurement instruments.
Lloyd Instruments test machines and material testing software are designed to determine the physical and mechanical properties of raw materials, components and structures, as well as the performance of finished goods. Our instruments are used in diverse industries including plastics, packaging, medical devices, pharmaceutical, electronic components, textiles, metals, composites, paper, building materials and much more for applications in production testing, quality control, laboratory testing, research and in universities.
Lloyd Instruments year's of experience in designing and producing materials testing machines is complemented by it’s dedication to provide its customers with expert applications expertise and comprehensive technical support, service and training options. Lloyd Instruments has sales office and distributors in most countries and is also an ISO 9001:2000 registered company including ISO TickIT registration for its materials testing software. The company is part of AMETEK, Inc., a global US manufacturer of electronic instruments and electromechanical devices.
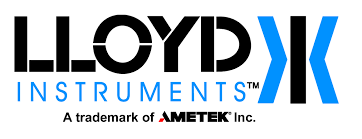
This information has been sourced, reviewed and adapted from materials provided by Lloyd Instruments Ltd.
For more information on this source, please visit Lloyd Instruments Ltd.