This article deals with the evaluation of volatile organic compounds (VOCs) released from museum display case construction materials as these compounds might have an unfavorable impact upon the condition of the artefacts kept inside them.
Generally, museum artefacts are protected against many environmental factors such as dust, excess moisture, exhaust gases, cigarette smoke, spores, pollen, smoke particles, and VOCs from skin and breath. These artefacts were thus placed inside airtight display cases that had limited air exchange rates.
However, the purpose of protecting the artefacts is complete only if the materials used in the display case are low-emitting. Otherwise, overtime VOCs accumulate and cause damage to the artefact. The other complication is that certain artefacts themselves emit harmful chemicals such as acetic acid, nitrogen dioxide, formic acid, and formaldehyde (all are corrosive to metals), calcareous objects, and cellulose-based artefacts such as paper.
Thus, the need to identify the chemicals, residual solvents in materials, and semi-volatile pesticides used for pest control is essential. There is a demand for quick processes for testing as well as some formal standards that can be adhered to when testing all the above-mentioned harmful effects. One such standard testing method is the BEMMA assessment scheme.
The BEMMA Scheme
Germany’s materials research institute BAM (Bundesanstalt für Materialforschung und –prüfung) created a new scheme for evaluating museum display case construction materials called BEMMA (Bewertung von Emissionen aus Materialien für Museumsausstattungen [Assessment of emissions from materials for museum equipment]) scheme.
The BEMMA scheme contains guidelines for handling analytical methods, and for applying limit levels for a variety of chemical classes. The scheme would be useful tool for effective decision-making by curators, restorers and conservators of museum artefacts.
Using the BEMMA scheme, each material can be analysed before a display case is made.
Methods and Materials covered under BEMMA
The following are the five methods for sampling and analysis specified under BEMMA:
- Pumped sampling onto Tenax® tubes and TD–GC–MS –For assessing VOCs and SVOCs from the cabinet air.
- Derivatisation and HPLC – For isocyanates.
- Derivatisation and LC–MS – For formic acid and acetic acid.
- Micro-Chamber/Thermal Extractor™ and TD–GC–MS – For assessing VOCs and SVOCs from materials.
- DNPH cartridges and HPLC – For formaldehyde and other very volatile aldehydes and ketones.
The following are some of the materials where BEMMA scheme can be applied:
- Sealants (e.g. silicone)
- Plastics
- Textiles
- Coatings
- Other materials (e.g. glue).
Criteria for Passing the BEMMA Test
A test report is created based on the data derived from the aforementioned analyses to define whether the material has passed the BEEMA test or not. The following are the criteria fixed by the BEMMA scheme:
- High pollution potential chemicals with such as acetic acid, formic acid, and formaldehyde should not be emitted from the materials, or even be detected.
- Total volatile organic compounds (ΣVOCs): 500µg/m3 maximum (with the exception of sealing materials, for which the value is 2000µg/m3 due to the significantly smaller application surface).
- Total very volatile organic compounds (ΣVVOCs): 100µg/m3 maximum.
- Total semi-volatile organic compounds (ΣSVOCs): 100µg/m3 maximum.
If any of these criteria are not met, then the material fails the BEMMA test. The resulting certification marking clearly defines whether the material can be used or not for the manufacture of display cases.
Sampling and analysis methods
Markes’ Micro-Chamber/Thermal Extractor™ (µ-CTE™) (Figure 1) is a key section of the sampling setup dictated by the BEMMA scheme. It is a compact unit containing four or six small cylindrical chambers that are ideal for sampling chemical emissions both from finished products as well as from corresponding raw materials.
The Micro-Chamber/Thermal Extractor works well alongside a thermal desorption (TD)–GC–MS analysis. Together they are considered as fast and inexpensive materials screening procedures in compliance with industry regulations.
.jpg)
Figure 1. The Micro-Chamber/Thermal Extractor.
In the case of planar materials, the sampling process requires cutting or ‘punching’ out a circular piece of material, which is placed into the chamber (Figure 2). Small glass dishes can also be used to hold samples of resins or adhesives.
.jpg)
Figure 2. Preparing planar materials for sampling using the Micro-Chamber/Thermal Extractor.
The chamber lids are closed and are set at a specific temperature. Pure air or nitrogen is supplied into it. Then after a suitable equilibration period, a sorbent tube is fitted to the outlet of each chamber in order to trap vapours emitted from the sample (Figure 3).
.jpg)
Figure 3. Operation of the Micro-Chamber/Thermal Extractor for sampling emissions of volatile chemicals from flat samples.
Once sampling is finished, the sorbent tubes are tested off-line using TD–GC–MS. In case of testing formaldehyde, a DNPH cartridge is added to the outlet, and then the vapours are sampled.
The cartridge is then studied using HPLC. The presence of multiple chambers helps sampling duplicate materials simultaneously under the same conditions, thus enabling fast processing coupled with a chance of analysing many samples from the same material.
In the BEMMA testing, sampling is performed at room temperature. However, this is not fixed. Higher temperatures can be used for simulating or accelerating conditions in display cases, and for inducing higher-boiling SVOCs into the gas phase.
Pumped Sampling Onto Sorbent Tubes
One of the most multipurpose TD sampling processes is pumped sampling onto sorbent tubes. When specific volumes (from 20mL to several hundred litres) are pumped via the tubes, it guarantees compatibility with a huge concentration range (sub-ppt to high ppm).
For the BEMMA scheme, pumped sampling can be used to evaluate VOC levels within the cabinets. A TD sampling pump is fixed to the end of a sorbent tube filled with Tenax TA, and cabinet air is pumped via the tube with a sampling rate and time suitable for the desired analyte concentration in the cabinet atmosphere. Markes’ ACTI-VOC™ pump is ideal for this purpose as it provides constant flow rates despite sorbent tube impedance.
Analysis of Sorbent Tubes by Thermal Desorption
The thermal desorption method is a ‘front-end’ tool for GC and GC–MS and can be used for the testing of VOCs, VVOCs, and SVOCs in solids, liquids and gases. The method merges pre-concentration, desorption/extraction and GC injection into a single sensitive and fully automated function. The sorbent tubes are heated in a flow of inert gas. The emitted components are transferred to an electrically cooled narrower ‘focusing’ trap inside the TD system.
Once the primary (tube) desorption stage is completed, the focusing trap is also desorbed in a fast manner by heating it quickly in a reverse flow of carrier gas. This aids in transferring the organic compounds into the GC–MS analytical system. This two-stage process promotes improved concentration and creates narrow chromatographic peaks, thus optimising sensitivity across a wide volatility range.
Markes’ thermal desorption system is built such that during injection into the GC–MS, the split effluent can be quantitatively transferred to another sorbent tube. This split effluent can then be desorbed onto the same trap for re-analysis, thus providing a chance to study the same sample under identical or different analytical conditions.
Example application: Analysis of pumped air from a museum case
Figure 4 demonstrates the advantage of using TD–GC–MS to determine problem impurities, showing the analysis of air pumped from a museum case storing an artefact with some amounts of enamel decay The major response from acetic acid shows high levels are likely to be responsible for degradation of the artefact.
.jpg)
Figure 4. Analysis of air pumped from a museum case, with sampling onto Tenax TA and analysis by TD–GC–MS.
Example application: Analysis of a glass sealant
The analysis of a piece of silicone sealant used to combine glass panels used to build museum cases (Figure 5). The presence of butan-2-one oxime means that this material would fail the BEMMA standards, as it is one.
.jpg)
Figure 5. Analysis of emissions from a sealant typically used to join together glass panels, with sampling using the Micro-Chamber/Thermal Extractor and analysis by TD–GC– MS.
Conclusion
There are many different technologies, including TD–GC–MS, to help the museums sector to maintain and protect their artefacts from damage caused by volatile chemicals. Especially, Markes’ Micro-Chamber/Thermal Extractor facilitates rapid and reliable analysis of VOCs emitted from display case construction materials.
About Markes International Limited
Markes International is a specialist manufacturer of analytical thermal desorption instrumentation and associated sampling equipment. The company's comprehensive portfolio of products is designed to automate and enhance the measurement of trace level volatile and semi-volatile organic chemicals (VOCs and SVOCs) in real-world samples.
For over a decade, Markes International has pioneered analytical thermal desorption (TD) instrumentation and associated sampling equipment. Markes has also the widest range of thermal desorption consumable products on the market; the company is widely regarded as being the World leader in thermal desorption technology.
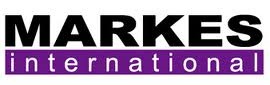
This information has been sourced, reviewed and adapted from materials provided by Markes International Limited.
For more information on this source, please visit Markes International Limited.