Inkjet inks can be defined as colloidally dispersed pigments in solution.
Pigment dispersion has to be accurate so as to prevent instability, sedimentation, or inkjet nozzle malfunction because of agglomeration. A reliable method for better formulation and manufacturing is required to establish that the final product has a uniform particle size distribution.
Generally, pigments, which constitute inkjet inks, are dispersed to small particle sizes (between about 50 and 200nm according to the application) and have to be made colloidally stable. The colloidal stability can be accomplished in two ways - either by surface modification to form a satisfactory surface charge (zeta potential), or by adsorption of specific compounds on the pigment particle surface also known as steric stabilization.
The pigment particle size is very important as large particles may block the channels and jets, hence resulting in damage to the printhead. The AccuSizer single particle optical sizing (SPOS) system from Entegris is suitable for establishing if the final inkjet ink has any oversized particles that may cause a risk for clogging jets and cause other reductions in performance.
This article looks at a few examples where the AccuSizer provides solutions for inkjet ink manufacturing challenges.
Particle Sizing and Counting Techniques
Many methods (e.g., dynamic light scattering (DLS)) are available for establishing the mean particle size of ink dispersions. However very few are good at establishing small amounts of oversized material. Methods incorporating size and counting of individual particles are ideal for the analysis.
The AccuSizer single particle optical sizing system (SPOS) is meant for quantifying the size and concentration of large particle tails present in inkjet inks. The SPOS (Figure 1) is capable of covering a dynamic range of 0.15-400µm. It includes a basic LE400 light extinction and scattering sensor measuring 0.5 to 400µm, which is mounted in the AD sampler. The AD sampler provides automated dilution of the sample to the optimum concentration for the measurement.
.jpg)
Figure 1. The AccuSizer 780 AD
Application Example 1: Effect of Stirring
Several factors affect pigment dispersion. One of them is stirring time. It is important to set an optimal stirring time in order to decrease the number of oversized particles in dispersions. It is also vital to monitor stirring time as over-homogenization could cause increased particle size.
Magenta and cyan pigment dispersions were studied so as to examine the effects of stirring time on oversized particles. The results of the magenta sample, which was stirred for 50, 70 and 90min can be seen in figures 2 and 3. The concentration of tail particles decreased from 4 x 106 particles/mL to 2 x 105 particles/mL.
.jpg)
Figure 2. Effect of stirring on magenta sample
.jpg)
Figure 3. Expanded view of magenta sample
Concentration of large particles >1µm:
- 50 min: 4 x 106 particles/mL
- 70 min: 5 x 105 particles/mL
- 90 min: 2 x 105 particles/mL
The cyan sample (Figure 4) undergoes a decline in the number of oversized particles with stirring time. The particles concentration comes down from 9 million particles/mL to about 3 million particles/mL with only 10 additional minutes of stirring.
.jpg)
Figure 4. Effect of stirring on cyan sample
Application example 2: Effect of Filtration
The following example illustrates the results of a filtration test, where an inkjet ink is filtered using a 2µm on and 5µm filter (Figure 5). Both filters display improvement in the concentration of particles >1µm. The unfiltered sample contained >100,000 particles/mL greater than 1µm while the 5µm and 2µm contained ~70,000 and ~20,000 particles/mL respectively.
.jpg)
Figure 5. Effect of filtration on inkjet ink
Conclusions
The AccuSizer 780 is an excellent system for quantifying the size and concentration of large particle tails in inkjet ink. In this article, the effect of stirring and filtration was examined. The system can be used as a general quality assurance tool, or as a process development tool to test optimum manufacturing conditions. Numerous sensors and configurations are available based on the application needs.
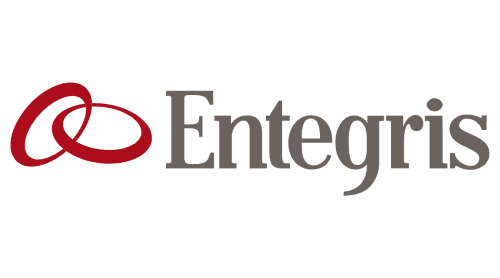
This information has been sourced, reviewed and adapted from materials provided by Entegris
For more information on this source, please visit Entegris