Thermo-plastic elastomers (TPE) have become highly popular in the past two decades. They offer attractive properties that are rubber-like enabling aspect and easy plastic processing. There is no need for curing and hence processing and energy costs are reduced. TPE is a family of different products such as thermo-plastic rubber (TPR), thermo- plastic vulcanisate (TPV), thermo-plastic urethane (TPU) and more.
This article is targeted at TPV as this material is most available for cured rubber component replacement with world consumption more than 1M tons a year.
Overview of TPV
As TPV can be processed similar to plastics, characterizing their flow behavior is very essential. Most producers of TPV do not only offer variable hardness grades but also materials having customized processing behavior such as blow molding, injection molding or extrusion grades.
TPV materials are non-Newtonian similar to normal polymeric materials. This means that there is a change in their viscosity with regards to shear rate. This property is very essential for determining precise flow prediction. The most simple viscosity model presently in use is the "power law" model.
The power law model suggests a logarithmic decrease of viscosity against shear rate. This simple model is given as
η = k • ɣ̇ (n-1)
where n is the pseudo-plasticity index or the expression of shear thinning effect.
This parameter can be determined by oscillatory or capillary rheometers. Oscillatory rheometers are more beneficial that capillary rheometers to determine viscosity at much lower shear rate and, at all shear rates, without wall slip. Capillary rheometers can measure at high to very high shear rate but in most cases suffer of catastrophic wall slip hindering meaningful viscosity measurements.
TPE Viscosity Characteristic Test
Figure 1 shows the TPE viscosity characteristic test on an oscillatory rheometer based on a frequency sweep in the melt. This test offers the respective viscosity level for four different products but offers their respective viscosity shear rate dependency.
TPV, however are complicated materials. They have different phases with a discontinuous cured rubber phase dispersed finely in a continuous poly-olefin phase. Hardness is adjusted using the ratio of the cured rubber phase over poly- olefin phase.
.jpg)
Figure 1. TPE viscosity characteristic test on an oscillatory rheometer based on a frequency sweep in the melt
Hard and soft materials are poly-olefin and rubber rich respectively. This nature is similar to rubber or polymer compounds where the dispersed rubber phase can be considered as filler fraction. Hence the simple power law model is not enough for precise prediction. By extending the shear rate range to lesser values, it is possible to observe clear separation of one sample over the others. These results are shown in Figure 2.
.jpg)
Figure 2. Results of extending shear rate range to lower values
The black curve sample shown in Figures 1 and 2 behaves as a pure polymer showing a clear pseudo-plastic nature with a viscosity Newtonian plateau (η*0). The hardness value of this material is 50 Shore D showing a material rich in poly-olefins hence a low level of dispersed rubber particles.
The hardness values of all other materials are 50 to 75 Shore A and are rubber rich materials. Hence Hard TPV and soft TPV can be considered as low and high filler fraction respectively. Hence instead of using the lower law model for all materials, it is good to apply a different model for high hardness material than for low hardness.
The best respective models for these materials are the "Carreau-Yasuda" and the "Hershel-Bulkley".
.jpg)
The last model is especially suited for compounded materials such as plastic and rubber compounds containing silica or CB fillers above percolation level. It features a critical stress (σc) at which the viscosity is infinite and under that the material does not flow. This information is essential for injection mold and extruder die design. Figure 3 shows the critical stress for rubber-rich TPV and the graph also shows that poly-olefin materials as shown in the black curve do not exhibit critical stress.
.jpg)
Figure 3. Critical stress for rubber-rich TPV
.jpg)
Figure 4. Non-linear reaction using Hershel-Bulkley equation
Conclusion
In order to perform this study, the programming of the oscillatory rheometer must be done in the following manner:
- The instrument must be closed at TPV temperature say 180°C. A premolded disc is preferred for testing perfectly homogenous samples. TPV granules may “sinter” offering poor homogeneity.
- Oscillate at minimal strain and moderate frequency for stabilizing material behavior such as 0.5% and 2Hz for 5 to 10mins. S' and S" are recorded to verify that stationary conditions are reached (constant or quasi constant S' and S").
- A frequency sweep is done at low strains not more than 1 to 2% over two to three decades of frequency (ex: 0.3 to 300 Rad/s). Strain constant needs to be maintained over the complete frequency range. All compounded materials show a strong to very strong non-linear behavior against strain.
- Plot η* versus S* or better σ* on a double logarithmic scale. Complex torque and stress have a linear proportionality in closed test chamber DMA's.
- Plot σ* versus shear rate. Next a non-linear regression is done using the Hershel-Bulkley equation.
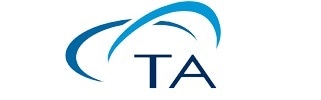
This information has been sourced, reviewed and adapted from materials provided by TA Instruments.
For more information on this source, please visit TA Instruments.