Fourier transform infrared spectroscopy (FTIR) is a measurement technique which generates an infrared spectrum of emission, absorption, Raman scattering or photoconductivity of a liquid, solid or gas.
An FTIR spectrometer is capable of collecting spectral data in a broad spectral range at the same time - this makes it preferable to dispersive spectrometers for many applications, as they can only determine intensity across a narrow range of wavelengths at a given time. The name Fourier transform infrared spectroscopy stems from the fact that a Fourier transform is needed to produce the actual spectrum from the raw data before it can be analyzed.
Polyurethanes
Polyurethanes are polymers which have excellent resistance to low and high temperatures, mechanical stress and chemicals, and do not degrade under sunlight. They also have excellent insulation properties with regard to noise, temperature, and electricity. Therefore, polyurethanes are used as substitutes to metals and plastics in a wide range of applications.
Polyols and isocyanates are precursors of polyurethane that can be highly reactive and toxic. A number of surfactants, catalysts, and additives are also utilized in the production process. Hence it is essential to reduce manipulations during the manufacturing process so that exposure to these compounds is reduced considerably.
Process Control for Polyurethane Synthesis
In order to achieve the desired properties for specific applications, the synthesis process for polyurethanes can be adjusted in a number of ways. However, it is important to control each stage of the manufacturing process to prevent adverse changes of the end product.
Using FT-IR spectroscopy for in-situ monitoring of polyurethane synthesis gives a better understanding of chemical reactions by monitoring a number of products and reactants continuously. This not only increases responsiveness compared to off-line laboratory analyses, but also prevents safety issues related to sampling.
Parameters controlling the measurement and display can be edited on-the-fly to optimize the monitoring of all components. This article describes the application of the ABB MB-Rx reaction monitor for real-time monitoring of isocyanates in phenylisocyanate and ethylene glycol reaction to produce urethanes.
MB-Rx Reaction Monitor
The ABB MB-Rx reaction monitor (Figure 1) allows direct access to real-time experiment data through an intuitive software and a robust insertion probe. The instrument is simple, reliable, and delivers excellent analytical performance. This plug-and-play system can be utilized any time sans the need for additional consumables.
.jpg)
Figure 1. ABB MB-Rx reaction monitor and complete experimental setup.
Chemical reaction in a batch reactor needs a fast and efficient method to determine the usage of reactants and also the formation of products and by-products to improve an industrial process in a short period of time. The MB-Rx instrument enables process development and research and development teams to get real-time insight into the progress of chemical reactions as they occur.
MB-Rx Analyzer for In-Situ Reaction Monitoring
Thanks to its small footprint, the MB-Rx can be utilized in crowded fumehoods to allow easy access to reactors. Its non-hygroscopic optics eliminate the need for desiccant cartridges. The instrument is also easy to use and works with a room-temperature detector. This means users do not have to worry about refurbishment constraints related to Stirling cooled-detectors or nitrogen supply for cryogenically-cooled detectors. The software interface enables fast set-up of new experiment templates, and all chemical and spectral properties can be monitored in real-time.
With a cast aluminium construction, the MB-Rx solution provides excellent protection for rigorous application in industrial settings. In addition, the combination of permanently-aligned optics and durable light source makes the instrument practically maintenance-free. Also, the integrated health monitoring checks operate endlessly while the MB-Rx is in operation, allowing chemists to focus on the reaction rather than the measurement interface.
Experimental Procedure
Experimental Plan
The reaction was carried out based on the reaction between phenol and phenyl isocyanate illustrated by Friebe and Siesler. First, ethylene glycol was dissolved in chloroform, and AlCl3 catalyst was added, followed by phenyl isocyanate. Temperature was maintained at 50ºC.
Experimental Setup
The following materials and parameters were utilized:
- Instrument: ABB MB-Rx reaction monitor
- Accessory: ZrO2 ATR probe + chalcogenide optic fibers
- Measurement Intervals: 30s to 1 min
- Resolution: 8cm-1
- Software: Horizon MBTM FTIR
- Scans: 19 - 39
- Material: Graham condenser, universal holder, thermometer joint adapters, clamp, probe, 4 necks round- bottom flask, stirring bar, hot plate with magnetic stirrer, support ring, and thermometer
In order to prevent exposure to hazardous materials, chemical manipulations and reaction run were carried out under a fume hood.
Results
Reaction Run FT-IR Spectra
In Figure 2, the spectra display a number of regions where changes can be seen over the course of the reaction. The upward trend observed at lower frequencies is the outcome of the penetration depth difference as a function of wavelength, which is characteristic of ATR measurements. This effect was partially offset by using a reference taken in chloroform, thereby showing a similar behavior.
.jpg)
Figure 2. Reaction run FT-IR spectra acquired during the reaction and major variations observed. Image Credit: ABB Ltd.
Trends and Parameters
Trend 1 (electric blue): υ(N=C=O) [Isocyanates]-reactant → Variation 1
- Type: Peak Area
- Range: 2179-2303 cm-1
Trend 2 (cyan): υ(N=C=O) [Isocyanates]-reactant → Variation 1
- Type: Univariate model (peak area) – Isocyanates wt%
- Range: 2179-2303 cm-1
Trend 3 (black): υ(C=O) [Urethanes]-product → Variation 2
- Type: Peak Area
- Range: 1683-1786 cm-1
Trend 4 (orange): [Unknown] Side reaction → Variation 3
- Type: Peak Area
- Range: 2603-2717 cm-1
.jpg)
Figure 3. Trends of isocyanates (blue/cyan, decreasing), urethanes (black, increasing) and side reaction (orange, increasing). Image Credit: ABB Ltd.
Discussion
Figure 3 shows trends of final urethanes and phenylisocyanate (NCO and NCO Univariate), demonstrate the capability of the MB-Rx to monitor urethane and isocyanates functional groups by means of the cubic zirconia (ZrO2) probe.
In this feasibility study report, the synthesis of polyurethane is imitated by phenylisocyanate (diisocyanates-like) and ethylene glycol (polyol-like); the former is generally utilized to produce links between the polyol chains.
The instrument’s performance, the application of chemometric models, and the frequency of the measurements give precise data on the reaction, i.e., end point, kinetics, and side-reaction to optimize the polyurethane synthesis. The MB-Rx also makes it possible to control the feed tanks or to inspect the quality of end products in a manufacturing line.
Conclusion
The feasibility study shows how the ABB MB-Rx instrument makes it possible to monitor the synthesis of polyurethanes. Products and reactants can be easily monitored simultaneously, at a higher rate than is permitted when using grab samples.
In addition, no manipulations had to be carried out during the reaction run, thus preventing risk of exposure to chemicals that are toxic and reactive. The responsiveness of the MB-Rx solution also makes it possible to improve experimental conditions and to tweak measurement settings on-the-fly for efficient development of novel reactions.
Thus, the ABB MB-Rx solution offers a number of benefits when compared to other methods, leading to reduced costs and increased safety of the entire reaction process.
About ABB Analytical Measurements
ABB's capabilities encompass one of the largest portfolios on the market for laboratory, at-line and process FT-IR/FT-NIR analyzers. They perform real-time analysis of the chemical composition and/or physical properties of a process sample stream.
ABB’s advanced solutions combine analyzers, advanced process control, data management, process and application knowledge to improve the operational performance, productivity, capacity and safety of industrial processes for customers while lowering environmental impact.
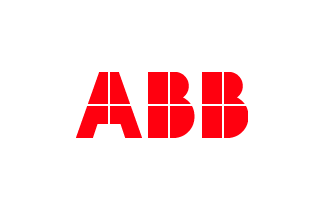
This information has been sourced, reviewed and adapted from materials provided by ABB Analytical Measurements.
For more information on this source, please visit ABB Analytical Measurements.