The test instruments from Bose are ideal for researchers who work with mouse and rat in vivo bone loading models. They provide the versatility and control required for performing a range of protocols, whether it is studying how mechanical forces impact bone formation or how loading affects interstitial fluid flow.
.jpg)
Figure 1. Bose compression testing instruments
Customizable Loading Profiles
One can apply several stimulation modes, which include combinations of ramp or sinusoidal inputs and pauses in both displacement and force control.
Lab-friendly Design
This all-electric clean solution is suited to be used in animal research environments. The Bose 5500 and 3100 instruments are lightweight and can be moved easily between research labs and animal facilities.
Versatile Functionality
It is also possible to use Bose test instruments for characterizing bone material properties through compression, bending and torsion tests.
Impact of Mechanical Stimuli on Bone-Related Research Areas
One can study the effect of mechanical stimuli on several bone-related research areas and applications. These include:
- Factors affecting mechanotransduction and gene expression
- Non-use effects (zero-gravity) or over-use effects (fatigue loading)
- Bone formation, resorption, and anabolic processes
- Disease models such as osteoporosis and osteogenesis imperfecta
- Interstitial fluid flow or drug delivery experiments
.jpg)
Figure 2. The impact of mechanical stimuli
Bose Instruments
Bose offers several test instruments that can satisfy present and future research needs. These include the following:
.jpg)
Figure 3. 3100
.jpg)
Figure 4. 5500
In-vivo Loading Accessories
The in-vivo accessories available for fulfilling one’s research needs include:
- Tibia and ulna loading cups for mice
- Platform for resting animal available- 3100 and 5500 test systems
- Low-force load cells (for e.g. 1000g)
- Bridge completion modules for strain gages
- Horizontal or vertical system mounting legs
- Software package to import physiologically-relevant loading profiles
The Need for Torsion Testing
Several components and products are subjected to torsional forces during their application. Designers can understand real-life service conditions, enhance product quality, validate the actual production process and verify the design. Examples of products subject to torsion stress in their typical service environment include biomedical stents, implantable orthopedic devices, fasteners and automotive steering/suspension components.
Types of torsion testing used vary based on the desired information from component or material. Examples include bone screws, biomedical type torsional testing for bone and plate assemblies.
Some type of torsional testing technique can be designed and performed for meeting the needs of each application whether it is for characterizing a torsion insertion test for bone screws, or performing basic failure tests, proof tests, or manufacturing process validation.
Analogies to Tensile/compression Testing
Torsion tests are normally done for determining a material’s torsional characteristics. Similar to properties determined during a compression or a tensile test, the "torque versus angle" diagram, for example, is similar to a "stress versus strain" curve.
The properties determined include:
- Modulus of elasticity in shear
- Yield shear strength (torsional elastic limit)
- Brittle failure (perpendicular to maximum tensile stress, 45 deg)
- Ultimate shear strength
- Modulus of rupture in shear
- Ductility (along the maximum shear plane)
Types of Torsion Tests
Torsion tests may apply to just a rotational motion or to the application of both axial (tension or compression) and torsional forces (moment).
The types of tests include the following:
- Torsion only: Applies torsional-only loads (torque or moment) to the specimen/device.
- Axial-torsion: Applies both axial (tension or compression) load and torque.
- Failure testing: Twisting the product, component, or specimen until failure.
- Evaluating the ductility and fracture toughness of a material
Flexural Bend Test
The flexural bend test is a qualitative test used for studying both the soundness and ductility of a material. Bend tests offer a simple way to describe the material's ability to resist cracking or other surface irregularities during one continuous bend.
A specimen’s fracture toughness can also be determined with a flexural test. The stress intensity factor is present at the crack tip of a single edge notch bending specimen. There are a number of reference documents that detail bending/flexural testing methods for a range of materials and Bose® ElectroForce® test instruments have been used for several of these types of applications.
- E6 Terminology Relating to Methods of Mechanical Testing
- E8/E8M Test Methods for Tension Testing of Metallic Materials
- ISO 12135: Metallic materials. Unified method for the determination of quasi-static fracture toughness
- ISO 12737: Metallic materials. Determination of plane-strain fracture toughness
- ASTM D790: Standard test methods for flexural properties of unreinforced and reinforced plastics and electrical insulating materials
- ISO 178: Plastics—Determination of flexural properties
- ASTM E1290: Standard Test Method for Crack-Tip Opening Displacement (CTOD) Fracture Toughness Measurement
Tension and Compression Testing
Two most basic types of testing material properties are tension and compression testing. This basic material property data is important for component design and service performance assessment. Standard analytical information obtained from compression and tension testing includes compressive strength, elastic limit, elongation, modulus of elasticity proportional limit, reduction in area, strain, yield point, yield strength, and ultimate tensile strength.
Typical test applications and the development areas are:
- The determination of tensile/compression properties of raw material to compare to documented material specifications;
- Experimental material property data for finite-element modeling or other product design to determine desired mechanical behavior and service duty cycles;
- Estimation of component mechanical performance by duplicating the expected service environment.
Important Test Sample Requirements for Testing
Specially-prepared test specimens are used for standard compression and tensile tests. These specimens can be flat plate samples or machined cylindrical samples and have a specific ratio of length to width- diameter in the test area (gage) in order for complying with standard ASTM/ISO testing standards.
Biological samples often need to be tested in their found condition although it is not uncommon to machine smaller samples from specific areas (e.g. bone) of interest. Small-scale testing does not often conform to established standards and the test engineer is left to devise the specimen geometry, gripping method and proper test equipment sizing to get optimized, repeatable results.
A range of Bose® ElectroForce® test instruments have been utilized for effective tensile and compressive testing as part of a comprehensive product design or research program.
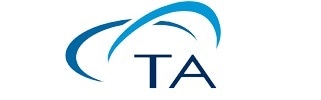
This information has been sourced, reviewed and adapted from materials provided by TA Instruments.
For more information on this source, please visit TA Instruments.