Spring srl, a rapid prototyping and additive manufacturing company based in Monteviale, Italy, opted to reverse-engineer parts in-house rather than outsourcing the work. Following a detailed market analysis, the company purchased Nikon Metrology’s 7-axis CNC articulated measuring arm and a digital laser scanning head.
This sophisticated equipment allowed Spring to digitize components quickly and precisely for 3D printing, and reverse-engineering, as well as also considerably improving the capabilities of the company’s quality control department.
Both small and large parts can be determined using the portable MCAx arm, which also includes a ModelMaker 3D laser scanner, as shown in figure 1 below. The use of Nikon equipment for sourcing elements ensures excellent compatibility and allowed Spring to depend on a single supplier for service, the Italian reseller Leonardo 3D Metrology.
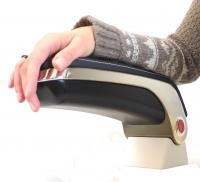
Figure 1. Spring srl uses the Nikon Metrology 3D laser scanner for reverse engineering, testing and dimensional control.
According to Roberto Toniello, Spring’s co-founder and head of their Engineering Department, the Nikon equipment not only enables the company to meet the needs and demands of the customers efficiently but it also provides a more integrated service in shorter lead-times with maximum reliability of results.
Reverse-Engineering as the Input for Additive Manufacturing
If a product has to be reproduced, but the original component has been altered or the CAD model does not exist, the actual component would need to be reverse-engineered.
Scan data is processed by Spring’s technical office using Geomagic Studio. This software imports the raw point cloud data obtained using Focus Handheld software from Nikon Metrology. The point cloud data is reverse-engineered into precise polygon, surface and native CAD models, which are sent to one of 10 CAD seats of Pro Engineer and Unigraphics NX, where STL files are created for driving six Stratasys Fortus fused deposition modeling (FDM) additive manufacturing equipment on site.
The additive manufacturing machines produce parts from thermoplastic materials, layer by layer which range from typical ABS and weather-resistant ASA through to Ultem 9085, a material that is resistant to flames, has high strength-to-weight ratio and certified for aerospace applications. It is also suitable for Formula One and other motorsport applications.
Enhanced Quality Control of Printed Parts
After the components have been built, the scanning equipment is used to inspect them so that their precision is determined, using an interchangeable touch probe or the laser head, or using both in a mixed measuring practice.
Nikon Metrology’s software provides the analysis and measurement environment, with intuitive tools for laser as well as tactile scanning applications. In fact, the scanner is utilized two-thirds of the time as a metrology instrument.
The quality control data thus obtained is evaluated against the original CAD file, whether it is derived from reverse-engineering or delivered by the customer. Out-of-tolerance features if any can be observed and determined. Similarly, part-to-part comparisons can be carried out to ascertain the reproducibility of a manufacturing process.
The Focus software from Nikon Metrology controls these activities, manages the acquired point clouds, carries out the comparisons, performs sophisticated feature inspection and finally generates the reports.
Spring needs to control the quality of components in this way so as to validate precision of parts and also to produce authenticated reports for customers. Particularly, F1 and Aerospace require complete traceability of production back to the raw materials.
However, it was rather complex for Spring to provide that level of expertise before its in-house metrology had been improved. A specific area of growth was the availability of 3D printed thermoplastic cores that are soluble and utilized by Spring’s motorsport and aerospace customers to create laminated composite structures.
Early Appreciation of the Importance of Additive Manufacturing
Founded in 1998, Spring integrated its mould and component design expertise with the additive manufacturing technology and was among the first company to recognize mass customization of products that are tailored according to customers’ specific needs.
The company now serves both ends of the market, producing both prototypes and batches of parts by 3D printing, and also designing and delivering moulds for die casting and plastic injection for longer production runs.
Spring’s co-founder, Fabio Gualdo informed that in series additive manufacturing, the design of a component needs to be optimized. The company recently produced a helicopter component made of Ultem 9085 thermoplastic, instead of the standard aerospace-grade aluminium as shown in figure 2 below.
In conventional manufacture, lead-times stretch to four to six weeks and would cost approximately €500 per piece. In contrast, the 3D printing not only reduced the time scale by by one-third but also reduced the cost by half.
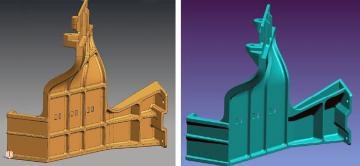
Figure 2. A cable guide for an aircraft modified and printed in Ultem 9085 by Spring srl using FDM technology (right), and the original aluminium version (left). The weight was reduced by 60 per cent, while both cost and time were saved. The Nikon Metrology scanner was used to assist in the redesign and to control the manufacture of the part.
The Need for a Metrology Upgrade
Earlier, Spring’s manual measuring techniques using standard metrology equipment had certain limitations, and hence the Nikon Metrology digital scanning arm was deployed to overcome this issue. Gualdo further added that unlike a coordinate measuring machine, the MCAx arm can be easily transported and enables the company to inspect all shapes and sizes of components.
High Quality Data from all Surfaces
The ModelMaker MMCx laser scanner is cost-effective yet powerful, similar to advanced Nikon Metrology heads, and is based on the laser source intensity. This makes it possible to scan surfaces sans the need for spraying and other pre-treatments.
The equipment has enhanced sensor performance (ESP3) that eliminates the need to manually adjust parameters when scanning different types of surfaces, even those having different colour and high reflectivity.
The advanced digital camera has a fast scan rate and provides a measuring precision down to 24m. In addition, the scanner has true non-interpolated resolution, which makes it possible to scan freeform surfaces and features easily and accurately.
The ModelMaker has a rugged design and is lightweight, making it easy to be used in production environments, while the Ethernet connection of the scanner makes it easy to connect to a laptop.
The MCAx arm has a carbon fibre tubular construction and is also lightweight. It is also counterbalanced and thermally stable. Unlimited rotation of all principal axes allows easy operation, and absolute encoders do away with referencing and warm-up time.
Conclusion
Spring now uses the Nikon Metrology scanning arm to inspect components the same day as they emerge from the FDM 3D printing machine. This saves a tremendous amount of time and money.
It also allows the company to quote more competitive prices with faster turnaround of customers’ orders. Time spent on other areas such as inspecting tools, fixtures, jigs, plastic injection and die casting moulds is also reduced, which leads to reduced costs.
About Nikon Metrology
Nikon is a global leader in optical instrumentation and is still the only microscope manufacturer that actually manufactures it's own glass for its products. Nikon acquired Metris in 2009, bringing further 3D metrology and Measuring capability into the brand.
The new division "Nikon Metrology" today offers the broadest range of metrology solutions for applications ranging from miniature electronics to the largest aircrafts. Nikon Metrology’s innovative measuring and precision instruments contribute to a high performance design-through-manufacturing process that allows manufacturers to deliver premium quality products in a shorter time.
Services Include:
- Highest quality service for all Nikon Metrology products (Nikon, Metris, LK, X-Tek, MetricVision, Krypton)
- Service & software support contracts
- Software helpdesk
- System calibrations and certifications
- Contract inspection services
- Part programming and training application services
- Metrology consulting
- ISO/IEC 17025 Certified Calibration Laboratory(US)

This information has been sourced, reviewed and adapted from materials provided by Nikon Metrology.
For more information on this source, please visit Nikon Metrology.