By Taha KhanReviewed by Lexie CornerAug 16 2024
Conventional manufacturing processes typically involve subtracting material from a larger block through cutting, drilling, or milling. In contrast, AM(AM) builds objects layer by layer, adding material precisely where needed. This approach enables the creation of complex geometries, intricate designs, and customized products that would be challenging to achieve using traditional techniques 1, 2
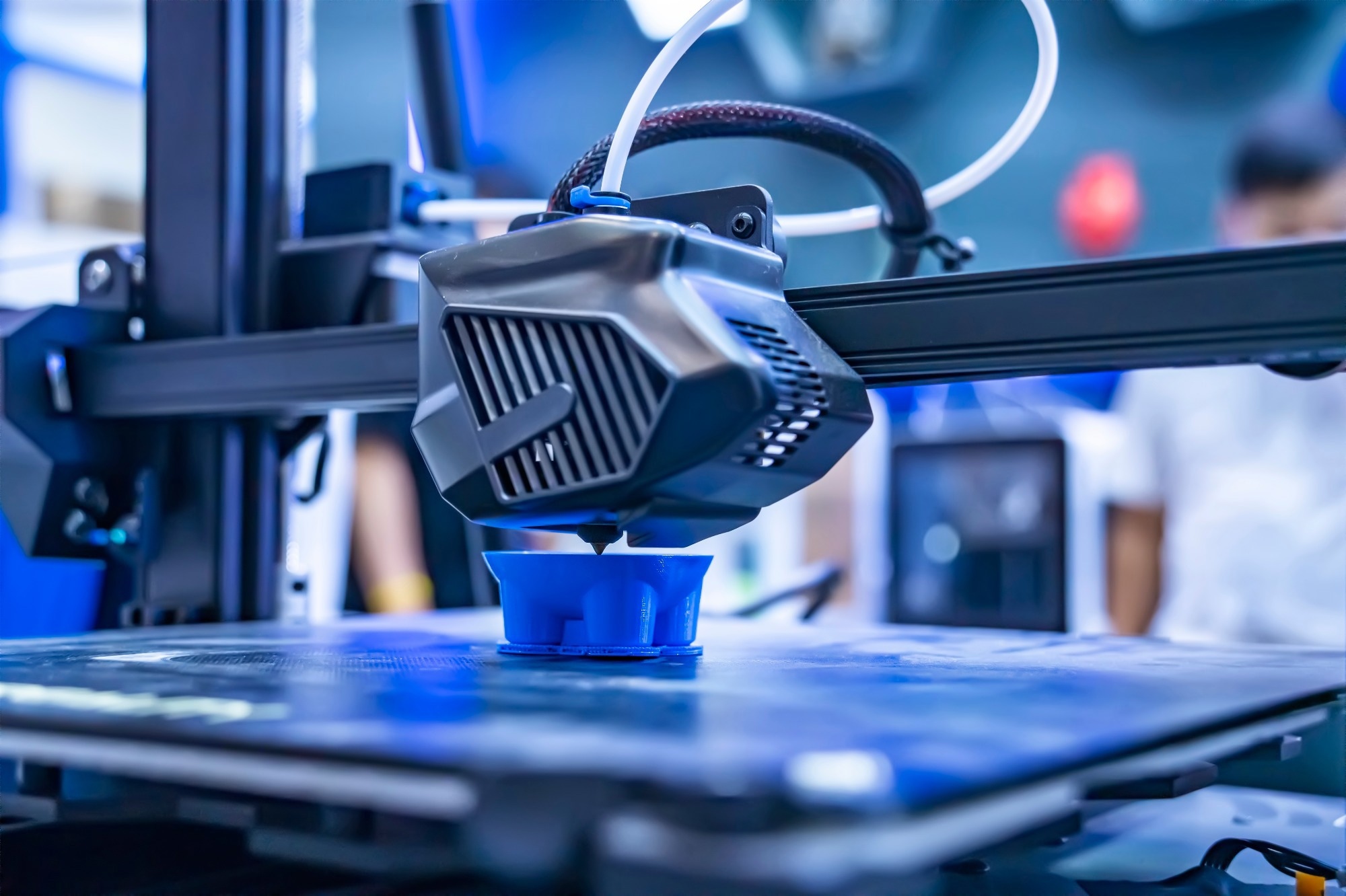
Image Credit: asharkyu/Shutterstock.com
The Process of Additive Manufacturing
The AM process begins with a digital design, usually created using computer-aided design (CAD) software, which is then sliced into thin layers. Depending on the specific AM technique, material may be deposited through a nozzle, solidified using a laser, or bonded with an adhesive. Each added layer fuses with the previous one, gradually forming the final shape.
AM can utilize various materials, including plastics, metals, ceramics, and even biological substances.1, 3
Main Techniques Used in Additive Manufacturing
Fused Deposition Modeling (FDM)
Fused Deposition Modeling is a widely used 3D printing technique that involves extruding thermoplastic material through a heated nozzle, which deposits the material in layers onto a build platform.
The material, typically a polymer, is melted in the nozzle and then precisely placed according to the digital design. As the material cools, it solidifies, bonding with the previous layers to create a 3D object.4
FDM is valued for producing functional prototypes, custom parts, and end-use products with reasonable strength and durability. This makes it popular in industries such as automotive, aerospace, and healthcare for rapid prototyping and small-scale production.
SLS, SLM, and SL
Selective laser sintering (SLS) is a type of AM that utilizes thermoplastic polymers. In this process, a laser sinters powder particles to form objects layer by layer, allowing for complex and detailed designs without additional support materials.
Selective Laser Melting (SLM) similarly employs lasers to melt metal powders, creating dense and robust parts suitable for industrial applications.3, 5
Stereolithography (SL), on the other hand, uses ultraviolet light to cure liquid resin into solid objects, offering high precision and smooth surface finishes.
Each of these methods provides unique benefits, catering to different material needs and application requirements.3, 5
Benefits of Additive Manufacturing
Compared to traditional manufacturing techniques, AM offers several advantages, particularly in customization, material efficiency, and waste reduction.
Traditional methods often involve material wastage, as excess material is removed to achieve the desired shape. In contrast, AM uses only the material necessary to build the part, layer by layer, resulting in minimal waste, reducing material costs, and supporting more sustainable manufacturing practices.1, 2
In industries like aerospace, where lightweight and complex components are essential, AM can produce strong and lightweight parts without extensive machining or assembly. AM also excels in producing customized products tailored to individual requirements without costly retooling or setup, which is particularly valuable in industries such as healthcare and fashion. Moreover, AM enables the creation of complex geometries that would be difficult to achieve with conventional manufacturing techniques.6, 7
Another significant benefit of AM is the speed at which prototypes can be produced, especially in industries like aerospace, automotive, and medical devices, allowing for rapid iteration and development cycles.6
Applications of Additive Manufacturing
AM has transformative applications across several industries. In aerospace, AM is used to produce lightweight, complex parts with high precision, reducing material waste and enhancing fuel efficiency. Components such as engine parts, brackets, and even entire aircraft wings are manufactured using AM, enabling rapid prototyping and customization.
The automotive industry also utilizes AM for rapid prototyping, which allows swift development and testing of new components. The ability of AM to create complex geometries without needing traditional tooling makes AM ideal for producing specialized parts and components, enhancing design flexibility, and reducing production lead times.6
In healthcare, AM is revolutionizing patient care with personalized medical devices, implants, prosthetics, and pharmaceutical formulations. For instance, a 2022 study explored three-dimensional printing to advance chewable pharmaceutical formulation production. This technique creates personalized dosage forms, known as Printlets™, customizable in shape, size, flavor, and drug dose.
3D printing has been particularly useful in addressing challenges associated with conventional dosage forms, such as swallowing difficulties among pediatric and geriatric patients. The technology has also led to the development of multi-drug formulations (PolyPrintlets™), which can improve medication adherence by simplifying complex dosing regimens.8
Future Prospects
AM allows the creation of complex geometries, reduces material waste, and facilitates the production of customized products on demand. It offers several advantages over traditional manufacturing processes, providing opportunities for innovation, customization, and efficiency.
As technology continues to evolve, AM is expected to enable mass customization, where complex and highly personalized products can be produced on a large scale. Integrating AI and machine learning into AM processes will further enhance precision and speed. Additionally, advances in material science will play a crucial role in developing novel materials that offer greater strength and durability to 3D-printed structures.
More from AZoM:
Unlocking the Secrets of Additive Manufacturing: Real-time Monitoring of 3D Printed Parts Using Dynamic Micro-CT
References and Further Reading
- Pereira, T., Kennedy, JV., Potgieter, J. (2019). A comparison of traditional manufacturing vs additive manufacturing, the best method for the job. Procedia Manufacturing. doi.org/10.1016/j.promfg.2019.02.003
- Attaran, M. (2017). The rise of 3-D printing: The advantages of additive manufacturing over traditional manufacturing. Business horizons. doi.org/10.1016/j.bushor.2017.05.011
- Wong, KV., Hernandez, A. (2012). A review of additive manufacturing. International scholarly research notices. doi.org/10.5402/2012/208760
- Rajan, K., Samykano, M., Kadirgama, K., Harun, WSW., Rahman, MM. (2022). Fused deposition modeling: process, materials, parameters, properties, and applications. The International Journal of Advanced Manufacturing Technology. doi.org/10.1007/s00170-022-08860-7
- Awad, A., Fina, F., Goyanes, A., Gaisford, S., Basit, AW. (2020). 3D printing: Principles and pharmaceutical applications of selective laser sintering. International Journal of Pharmaceutics. doi.org/10.1016/j.ijpharm.2020.119594
- Mohanavel, V., Ali, KA., Ranganathan, K., Jeffrey, JA., Ravikumar, MM., Rajkumar, S. (2021). The roles and applications of additive manufacturing in the aerospace and automobile sector. Materials Today: Proceedings. doi.org/10.1016/j.matpr.2021.04.596
- Abdulhameed, O., Al-Ahmari, A., Ameen, W., Mian, SH. (2019). Additive manufacturing: Challenges, trends, and applications. Advances in Mechanical Engineering. doi.org/10.1177/1687814018822880
- Rodríguez-Pombo, L., Awad, A., Basit, A. W., Alvarez-Lorenzo, C., Goyanes, A. (2022). Innovations in chewable formulations: the novelty and applications of 3D printing in drug product design. Pharmaceutics. doi.org/10.3390/pharmaceutics14081732
Disclaimer: The views expressed here are those of the author expressed in their private capacity and do not necessarily represent the views of AZoM.com Limited T/A AZoNetwork the owner and operator of this website. This disclaimer forms part of the Terms and conditions of use of this website.