As fossil fuel supplies globally continue to dwindle, there is a drive to use more fuel-efficient vehicles. When an automobile’s weight is reduced by 10%, fuel efficiency is improved by 6 to 8%, and greenhouse gas emissions are also reduced. By using lightweight structural materials, weight reduction is possible.
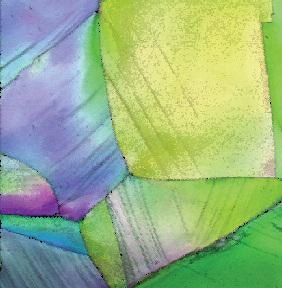
Figure 1. Orientation map of TWIP steel showing twin boundaries introduced during deformation
Vehicle designers face the challenge of developing manufacturing processes and materials that not only reduce weight but also have the required strength to meet crash safety tests. Furthermore, this must be done without increasing the vehicle cost beyond a specified level.
Comparison with Existing Solutions
Key microstructural parameters need to be measured in order to use and develop lightweight structural materials and optimize production and manufacturing processes. Existing solutions include the following:
- Grain size is measured using optical microscopy requiring alloy-specific chemical etching. All of the grain boundaries may not be visible upon etching. Also, chemicals are employed having special handling and disposal requirements.
- Phase distribution is determined using electron or optical microscopy. These measurements infer phases by measured grayscale level instead of offering a direct composition and structure measurement. In order to reveal all phases present, multiple chemical etching treatments may be needed.
- The traditional measurement of crystal orientation on an individual grain is done by transmission electron microscopy (TEM). TEM analysis needs expert sample preparation techniques, tools, and expertise. Orientation measurements are normally done manually limiting the number of measurements that can be collected.
- Texture, desired orientations in a sample, is determined by X-ray diffraction (XRD). Texture measurements with XRD do not offer spatially specific orientation measurement but rather a collective sample’s orientation with the measurement volume.
- Plastic strain, the orientation change within grains due to an applied load, is conventionally measured using TEM. The area of analysis of TEM is restricted. TEM samples are normally 3mm diameter and the sample portion thin enough for TEM analysis smaller than this. Data collection is further limited by a lack of automated measurements.
In contrast, Electron Backscatter Diffraction (EBSD) offers a quick and automated solution to determine the lightweight material microstructure. EBSD benefits include:
- Directly measuring grain size using discrete orientation measurements to eliminate ambiguous grain boundary determination errors.
- It is also possible to detect specific grain boundary types such as phase transformation orientation relationships or twin boundaries to help understand heat-treating or deformation processes.
- Direct measurement of phase distribution is possible by determining crystallographic structure using EBSD and chemical composition using Energy Dispersive Spectroscopy (EDS). ChI-ScanTM, the combined use of EBSD and EDS for phase mapping, provides accurate phase distributions even for complex lightweight materials such as advanced steels and Al-Si castings.
- Direct measurement of crystal orientation and texture. Automated measurements with speeds of up to 1,400 points per second on alloys enable rapid collection of a statistically significant data set. It is easy to obtain maps for visualizing the spatial distribution of orientations. Simultaneously texture information is obtained eliminating the need for additional analysis time.
- It is possible to obtain a direct measurement of plastic strain with orientation precision values below 0.1°. Orientation precision data enables better optimization and understanding of the deformation processes active during forming and fabrication processes used to integrate lightweight materials into automotive designs. The automated analysis of areas more than 1x1 cm enables visualization of deformation over large areas and cross-sections to understand how deformation and plastic strain is distributed within a material.
Microanalysis Results
The key structural materials which can help to reduce automotive weight are aluminum, steel, and magnesium alloys. While steel density is the highest of the three alloys, its formability and mechanical properties make it desirable for crash protection. Using continuous annealing and microalloying, or other thermo-mechanical processing methods, advanced high strength steels have been developed with lower densities.
The resulting materials show increased toughness and strength both for weight reduction and ensuring safety. Twinning induced plasticity (TWIP) steel is an example of advanced engineered steel. TWIP steels are developed for absorbing more energy in a crash when compared to conventional steels while maintaining stability and strength. This is due to deformation twinning, which takes place during a crash, increasing a material’s yield strength.
As seen in Figure 1, EBSD measures the microstructure and twin boundaries present in the steel before and after deformation to improve and optimize the processing conditions.
Two-phase microstructures can be seen in dual-phase steels which offer increased strength with better formability. In order to optimize the heat treatment at the time of production, EBSD measures the phase distribution as seen in Figure 2.
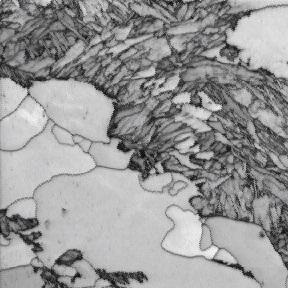
Figure 2. EBSD image quality map of Dual-Phase steel showing duplex microstructure.
Aluminum offers increased potential for weight reduction compared to steel. A major factor for consideration is formability. Stamping as a manufacturing technique is affected by the crystallographic texture of the material being processed. Texture control is possible through processing parameters in order to improve formability. Weight can be considerably reduced by the use of cast aluminum alloys for engine blocks. Developing new alloys for higher temperature applications requires the determination and measurement of the phases that develop in these alloys both at the time of casting and while in use at high underhood temperatures.
Magnesium provides an attractive combination of low density and high strength. Moreover, manufacturing challenges must be overcome in order to be useful. Normally wrought magnesium alloys have a (0001) texture creating anisotropic materials properties.
An orientation map of wrought magnesium is shown in Figure 3. Formability improvements are required. In order to understand the impact of deformation and alloying rate and temperature on formability to make magnesium a viable lightweight material, EBSD is used.
Integrating new lightweight structural materials into automotive designs requires that these be reliably joined together with conventional materials. Safety or strength must not be compromised by this joining and it should be cost-efficient. EBSD data helps in optimizing the joining process to produce high-quality joints.
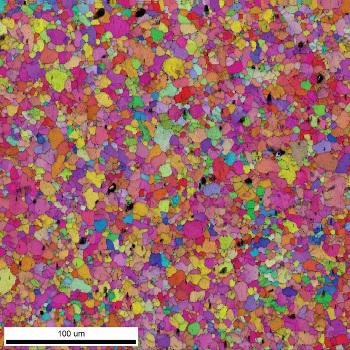
Figure 3. Orientation map of wrought magnesium exhibiting (0001) texture.
Recommended EDAX Solution
Pegasus Analysis Systems are suggested in order to help scientists and engineers develop the manufacturing processes and materials required to satisfy the challenging requirements of lightweight structural materials.
Pegasus Analysis Systems offer combined EDS and EBSD characterization with an easy to use interface for detailed analysis of material chemistry, crystallography, and phase distribution.

This information has been sourced, reviewed and adapted from materials provided by Gatan Inc.
For more information on this source, please visit Gatan Inc.