Work coils, also referred to as the inductor, are a part in an induction heating system. Their purpose is to indicate whether a work piece has been heated effectively and efficiently. There are numerous types of work coil in the market ranging in complexity.
The most simple being the helical (or solenoid) wound coil that has numerous turns of copper tube twisted over a mandrel to a coil precision machined type obtained from solid copper and then subjected to brazing.
The work coil helps to transmit the energy from the workhead and the induction heating power supply to the work piece by producing an alternating electromagnetic field. The electromagnetic field produces a current which is transmitted through the work piece as a mirror image to the current transmitted through the work coil.
As the current flows via the work piece’s resistivity, it produces heat within the work piece due to I²R losses. The other heating principle that occurs here is hysteretic heating when the work piece contains a magnetic material, such as carbon steel.
In this case, current is produced inside the work piece by the alternating magnetic field varying the magnetic polarity within the work piece. Hysteretic heating happens in the work piece up to the Curie temperature (750°C for steel) when the magnetic permeability of a material reduces to 1.
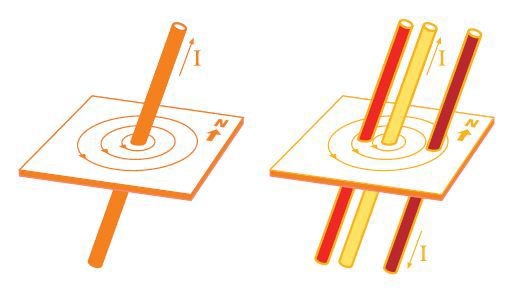
Figure 1. A current flowing in a conductor creates a magnetic field. An alternating current creates an alternating field which produces an alternating current in a second conductor (the work piece). The current in the work piece is proportional to the field strength.
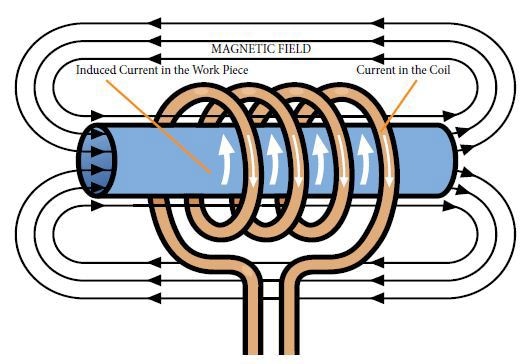
Figure 2. The transformer effect where the amount of current induced in the work piece is proportional to the number of turns on the coil and is generated as a mirror image of the work coil.
Coil Design
Coil design is important to the efficiency and effectiveness of an induction heating method. The coils designed by Ambrell take into account where the heat is required to be generated in the component to perform the method, and then the coils are constructed to realize the heating effect.
Induction coils are water-cooled copper conductors built using copper tubing that is readily formed into the shape of the coil for the induction heating method. Induction heating coils are cold and do not become hot when water flows through them. The coil has to be correctly matched to the induction power supply to ensure method efficiency. Ambrell’s frequency-agile induction units can be matched to several coils with the aid of the multi-tap output transformer in the power supply.
Multi-turn Helical Coil
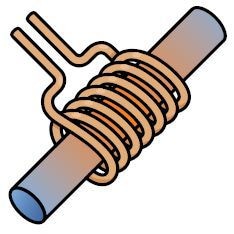
The helical (solenoid) coil is a very commonly used coil containing several turns defining the width of the heating model. In order to render a specific heating band during single shot heating, the work piece can be kept stationary in the coil or, a highly consistent heating pattern termed as scan heating can be used wherein the work piece is pushed through the coil.
Single-Turn Coil
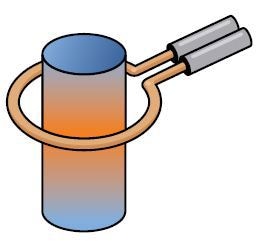
Single-turn coils are perfect for heating either a narrow portion of a work piece or the work piece tip. It is also possible to use these coils to scan the work piece along its length and is usually used for heat treating. These coils are mostly tightly fixed to the part to provide an accurate heat pattern.
Multi-Position Helical Coil
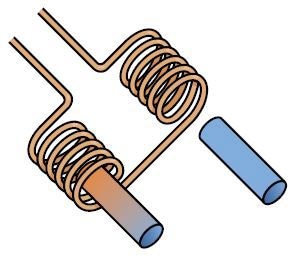
Multi-position coils are frequently used to generate more parts within a specific time while permitting the complete heating process. When a single work piece is heated at one position, another coil can be unloaded and reloaded for the subsequent heating cycle. Numerous positions are possible; however up to eight positions are realistic.
Channel Coil
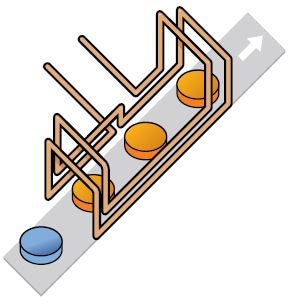
A coil can be designed in such a manner that the work piece moves via the electromagnetic field by linear transport mechanism. The work piece gets heated as it passes via the channel coil, and the coil can be constructed to heat all of the parts or only a single band.
Curved Channel Coil
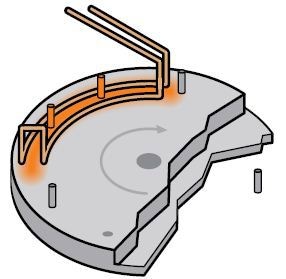
Channel coils are mostly curved to fit onto a rotary table. They are designed to occupy one of the stages in a multi-step assembly procedure.
Pancake Coil
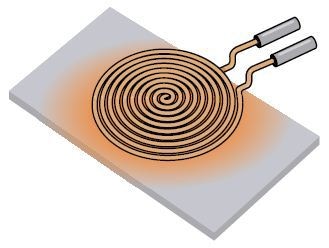
Pancake coils are used in case the work piece has to be heated from just one side or when it is not possible to surround the entire component.
Split Helical Coil
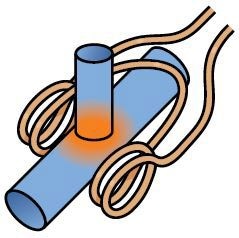
In cases where it is not possible to obtain access to the heated area using a helical coil, a single or multiple turn split helical coils are used.
Internal Coil
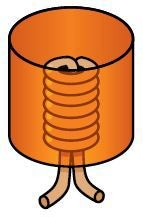
Single- or multiple-turn internal coils can be used to heat internal bores.
Concentrator Plate Coil
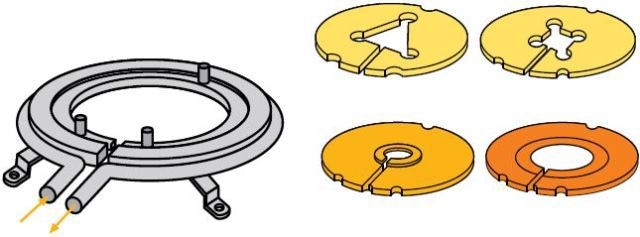
Concentrator plates are mostly used in single- or multiple-turn coils in order to focus the coil current to generate a specific heating effect in the work piece. These coils may be provided with a master coil with inserts that enable heating various shaped parts.
Coils and Conveyors
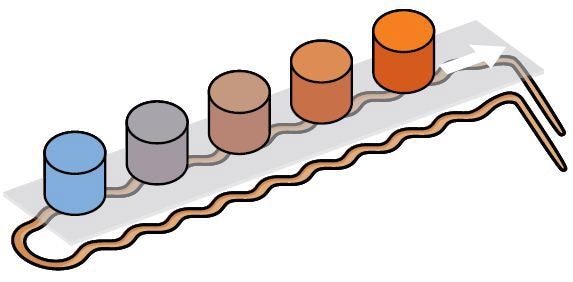
Many components are heated as they are being transported by a conveyor system. The conveyor material should not be electrically conductive to allow the magnetic field to pass via the conveyor and heat the work piece as it moves via the field.
Hair-Pin Coil
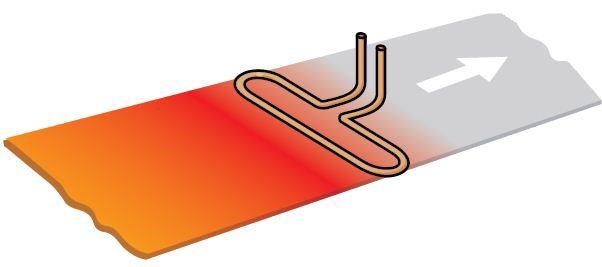
A long thin single- or multiple- turn coil can be adapted for heating a long thin zone on a part as well as for heating a moving web of thin aluminum or steel.
EASYCOIL
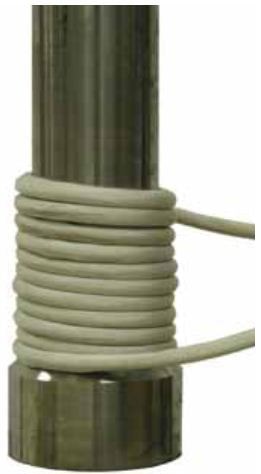
The flexible EASYCOIL is perfect for large, irregularly shaped work pieces that cannot be heated using a conventional copper coil. It is used in combination with Ambrell’s EKOHEAT and EASYHEAT induction heating systems – up to the 250kW model.
Encapsulated Coils
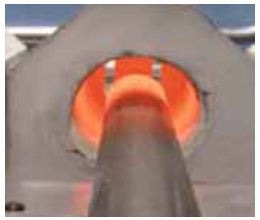
After a coil is designed, its heating pattern is analysed, then the coil is encapsulated for thermal insulation. This is to make the coil assembly sturdier in tough environments. Typical encapsulation materials are ceramics, concrete, and epoxy or thermoplastics.
Single-turn coil with ferrite concentrator is an example. Field concentrators can be applied on coils to strengthen the electromagnetic field and increase the current density in the work piece. Concentrator materials are shim steel at low frequencies and ferrites at high frequency. Another type is the multi-turn helical coil with turns fixed with plates and studs displaying quick release connection blocks.
Conclusion
Coil design is crucial to the efficiency and effectiveness of an induction heating technique. The coils designed by Ambrell are tailor-made to suit various conditions such as heat resistance. The materials used are according to customer’s requests.
About Ambrell Precision Induction Heating
Precision induction heating solutions are our specialty. We manufacture high and low power systems for a wealth of specialized applications, including nanoparticle heating.
Our approach is to listen to your unique needs and concerns. Then, we will invite you to send samples of your parts to our Applications Lab for a complimentary evaluation and system recommendation. Benefit from the advice of experienced applications engineers who have worked with parts of virtually any size and shape. Let us show you the Ambrell difference!
With a reputation for quality built on our 25 years' experience, the Ambrell companies – with offices around the world - provide you with effective precision heating solutions. Our equipment, installed in over 50 countries, is supported by our network of dedicated induction heating experts. Ambrell engineers hold over 25 technological patents and a significant percentage of revenue is reinvested into research and development to ensure you’re getting state-of-the-art solutions.
If you want to improve your heating - anywhere in your process - consult with the Ambrell team for cost-effective, high-efficiency solutions.
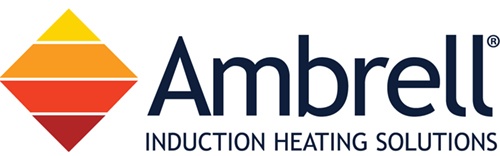
This information has been sourced, reviewed and adapted from materials provided by Ambrell Induction Heating Solutions.
For more information on this source, please visit Ambrell Induction Heating Solutions.