Harper is an established leader in thermochemical processing systems. The company is also a key partner in carbon fiber scale up and manufacturing.
.jpg)
Figure 1. Cascading system with multiple atmospheres.
Image Credit: Harper
The key technical focus is on novel, challenging and advanced material processing at temperatures between 200°C to 3000°C. Batch and continuous processing, highly accurate atmospheric controls, complex gas-solid interactions and high-purity are required.
The article covers the process of moving from batch to continuous production in high temperature ceramics processing.
Challenges in New Material Process & Product Development
Technical Success
For technical success, handling of waste and by-products, product quality, large scale processing and continuous operation is required.
Development Costs
Development costs involve the cost of pilot scale equipment, resources for trials and analytical costs.
Objectives in Thermal Processing Scale Up
The objectives in thermal processing scale-up include the following:
- Measure the feasibility under industrial conditions
- Minimize the development risk and the related cost
- Generate scale-up data
- Design a safe technique that will satisfy environmental regulations
Scale Up Success -Test Facilities
The equipment must be small enough to allow testing without the use of large raw material quantities.
It must be large enough to allow adequate product for sampling and also for generating enough data sufficient for commercial scale-up.
The size must also be large enough to use readily available gas regulators, feeders, and collection set up.
Scale Up Success -Starting Status
The Gram scale product is a batch process, the operation is normally static, involves a low gas flow and well analyzed product.
The available data include impact of temperature and reaction time for static conditions. Unavailable data includes effect of gas flow rate, effect of bed depth and gas solid contact.
Scale Up Success -Desired Final Information
The desired final information includes a define processing window, optimum values for feed rates, residence time and gas flow, design for product removal systems and material feeding systems, effluents in the exhaust chemistry, quantity and material entrainment in gas.
.jpg)
Figure 1. Cascading system with multiple atmospheres.
Image Credit: Harper
Scale Up Success -Information Generated in the Trials
The information obtained in the trials include the following:
- Gas solid contact and methods for optimization
- Rate limiting reaction kinetics
- Techniques for suppressing entrainment, reducing contamination, preventing condensation/recycling from exhaust gases, raw material feeding and product discharge and collection
- Handling of exhaust gases
- Benefits of counter-current or co-current flow
Scale Up Success -Data Analysis and Equipment Design
The data obtained from laboratory tests will help in specifying the process window, help in the development of process flow diagrams, and offer scale-up information for commercial production.
Follow up engineering analysis includes the following:
- Equipment size scale up
- Stress and thermal modelling
- Define feed and product collection systems
- Ascertain gas handling systems
- Determine OPEX and CAPEX
Scale Up Success -Data Analysis and Equipment Design
OPEX Estimation involves 80-90% of total cost over lifetime, process cost models, economics of high production capacity with present and future technologies, analyzing ideal thermal process technology system and identifying opportunities for better product quality and cost reduction.
CAPEX Definition involves approximately 10-20% of total cost over lifetime, is founded on scale-up from trial data collected, scale up of processing equipment to satisfy required production targets, design integration for handling feeding, product handling, gas systems and effluent management and preparing a capital cost estimate.
.jpg)
Figure 2. Case Study: Molybdenum Production.
Image Credit: Harper
Ignite Program
The Ignite program is aimed at enabling customers to convert future material innovations into profitable new markets. The program uses the depth and breadth of the company’s experience in thermal processing. The program achieves the following:
- Reduce risk
- Control cost
- Parallel development
- Controlled scale-up
- Successful commercialization
Stage Gate Approach
The stages include:
- Stage 1 – Prospecting
- Stage 2 – Initial testing
- Stage 3 – Applied research
- Stage 4 – Applied Research II
- Stage 5 – Trial manufacturing
.jpg)
Image Credit: Harper
.jpg)
Image Credit: Harper
.jpg)
Image Credit: Harper
.jpg)
Image Credit: Harper
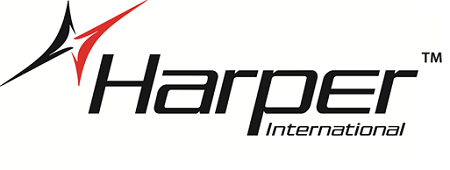
This information has been sourced, reviewed and adapted from materials provided by Harper International.
For more information on this source, please visit Harper International.