A catalyst is a substance that speeds up a chemical reaction while undergoing no permanent change at the end of the reaction. In order to understand the performance of catalysts, it is important to determine and quantify the chemical states of the elements in the catalyst samples.
Metal-based catalysts are generally utilized in redox reactions, and hence metal oxidation state should be carefully regulated so that the performance of the catalyst is not affected.
Reactions normally occur at the surface of the material and hence a method for determining the catalyst‘s surface chemistry is needed. For this type of characterization, X-ray photoelectron spectroscopy (XPS) serves as a suitable technique.
It is also a surface-sensitive technique. In this method, samples are examined under vacuum conditions and any surface changes that occur during the course of analysis are kept to a minimum.
Spectra ensue from the top 10nm of the surface, enabling XPS to focus on the critical surface area. The XPS technique is capable of identifying and quantifying the chemical states as well as the elemental compositions of the elements detected.
Thermo Scientific K-Alpha Surface Analysis System
Thermo Scientific has developed a high-performance solution called K-Alpha surface analysis system. This system allows scientists to use the XPS technique to determine the chemical states and composition of the surfaces of catalyst samples quickly and accurately.
This article shows how the K-Alpha surface analysis system was utilized to examine a γ-alumina supported Co(Ni)MoS catalyst to extract chemical state data from fresh and air-exposed samples, and also to establish the level and type of chemical change experienced by the catalyst following exposure to air.
Experimental Method
After removing the catalyst pellet from its storage under hexane condition, it is loaded onto double-sided copper tape, which in turn was fixed to the sample platter. Soon afterward, the sample block is loaded into the fast entry load-lock, where it is automatically pumped down and shifted to the analysis chamber. This pellet was examined to extract chemical and elemental data.
After completing this analysis, the sample is taken out of the system and exposed to air for a period of 3 min at atmospheric pressure. Following this, the sample is pumped down and shifted back into the analysis chamber.
The following XPS analysis was compared against the original results to ascertain the extent of oxidation of the surface of the sample after air exposure.
Results and Discussion
Figures 1 and 2 show the cobalt 2p3/2 spectra recorded on fresh and aged catalysts, respectively. With the help of the integrated peak fitting software in the Avantage data system, the different phases of Co were measured in accordance with reference 1.
Using a multi-component fit the spectrum was fitted, assuming CoMoS, Co9S8, and Co (II) oxide phases. When the sample was transferred from the container to the K-Alpha system, no major oxidation was noted.
This showed that the sample had the predicted composition. Following exposure to air, more oxidation was seen, increasing the relative amounts of Co9S8 and Co(II) oxide phases at the surface of the catalyst sample and decreasing the relative amount of CoMoS phase. Likewise, an analogous increase in oxidation was observed in the molybdenum spectra (Figures 3 and 4).
.jpg)
Figure 1. Co2p3/2 spectrum of fresh catalyst
.jpg)
Figure 2. Co2p3/2 spectrum of an aged catalyst
.jpg)
Figure 3. Mo3d spectrum of fresh catalyst
.jpg)
Figure 4. Mo3d spectrum of an aged catalyst
Similar to the cobalt spectra, more oxidation was seen following air exposure to air, increasing the relative amounts of Mo(VI) oxide and Mo(IV) oxide at the surface of the catalyst sample, and decreasing the relative amount of Mo(II) sulfide.
The comparison table of the entire chemical state quantification for both fresh and aged samples is shown in Table 1. The quantification indicates that the quantity of alumina support remains the same, while the cobalt, molybdenum, and sulfur have become more oxidized. These increased levels of oxidation allow the analyst to measure the quality of the catalyst surface.
Table 1. Full chemical state quantification for both the fresh and aged sample
XPS Peak |
Chemical State |
Fresh Sample (At. %) |
Aged Sample (At. %) |
Al2p |
Al2O3 |
23.97 |
24.65 |
S2p3/2 |
Sulfide |
7.01 |
5.34 |
S2p3/2 |
Oxysulfide |
0.30 |
0.90 |
Mo3d5/2 |
Mo(II) Sulfide |
2.62 |
1.43 |
Mo3d5/2 |
Mo(IV) oxide |
0.14 |
0.86 |
Mo3d5/2 |
Mo(VI) oxide |
0.24 |
0.74 |
C1s |
C-C/C-O/C=O |
22.79 |
17.81 |
O1s |
O-C/O-metal |
40.77 |
46.14 |
Ni2p |
Ni(II) sulphide |
1.64 |
2.13 |
Co2p3/2 |
Co9S8 |
0.07 |
0.10 |
Co2p3/2 |
CoMoS |
0.33 |
0.22 |
Co2p3/2 |
Co(II) oxide |
0.13 |
0.20 |
Conclusion
The Thermo Scientific K-Alpha XPS system can be effectively utilized to detect and measure the chemical states of the elements found in catalyst samples.
In this analysis, the K-Alpha system was utilized to study the surface chemical change between a γ-alumina supported Co(Ni)MoS hydrodesulfurization catalyst and the same catalyst following exposure to air.
The XPS technique made it possible to identify and quantify the chemical variations between the two samples.
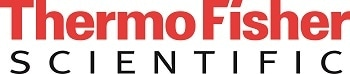
This information has been sourced, reviewed and adapted from materials provided by Thermo Fisher Scientific – X-Ray Photoelectron Spectroscopy (XPS).
For more information on this source, please visit Thermo Fisher Scientific – X-Ray Photoelectron Spectroscopy (XPS).