Tungsten alloys are best suited for applications where there is a requirement for a large weight concentrated in the minimum possible space. They are also an ideal material for high-vacuum technology that needs very high temperatures.
Machining pure tungsten is a challenge as it is moderately brittle; however, when chemical elements such as copper, nickel, and iron are added, tungsten alloys are created which possess exceptionally useful properties. They are more than 50% heavier than lead and twice as heavy as steel. Tungsten alloys have thus become a vital material for a wide range of applications.
Using powder metallurgy methods, these alloys can be economically manufactured. They can be routinely machined by traditional techniques. Tungsten alloy products can be delivered to customers as finished products based on drawing specifications or as semi-finished products requiring further processing by the customer. Both types of product are lead-free and comply with legal requirements and proposals to protect the environment.
Oil and Gas Drilling Applications
H.C. Starck Solutions’ flat rolled MP35N products are used in several applications:
- Oil sector, chemical and marine equipment – valve components, springs, high pressure door dogs
- High pulse magnet research
- Orthodontic and prosthetic devices
- Aircraft and aerospace parts – springs, leading edge strips
The radiation shielding properties of tungsten alloys make them exceptional for use in manufacturing products to surround data logging instrumentation and isotopes, vital to locating oil and gas deposits. Shielding the instrumentation from radiation significantly enhances the performance of the data logging, as well as enhancing operational safety for personnel.
As well as radiation shielding, tungsten alloys are also advantageous for sinker bar applications. These high density weights or series of weights are fixed to the down-hole logging tool assemblies so as to add the extra weight to help the tool to properly descend through the heavy borehole fluids.
H.C. Starck Solutions supplies the long established Kulite® tungsten alloys from the U.S. (Table 1) and HPM tungsten alloys from Germany (Table 2).
Table 1. Kulite® tungsten alloys (K1700 thru K1850)
Alloy Designation |
Unit |
K1700 |
K1701 |
K1750 |
K1800 |
K1801 |
K1850 |
Tungsten content |
(%) |
90 |
90 |
92.5 |
95 |
95 |
97 |
Density |
(g/cm3) |
17 |
17 |
17.5 |
18 |
18 |
18.5 |
Density |
(lb/in3) |
0.61 |
0.61 |
0.63 |
0.65 |
0.65 |
0.67 |
Hardness |
(Rc) |
23 |
22 |
24 |
25 |
24 |
26 |
Ultimate Tensile Strength |
(psi) |
125,000 |
110,000 |
125,000 |
125,000 |
110,000 |
120,000 |
Ultimate Tensile Strength |
(N/mm2) |
860 |
760 |
860 |
860 |
760 |
830 |
Yield Strength |
(psi) |
85,000 |
80,000 |
90,000 |
90,000 |
85,000 |
95,000 |
Yield Strength |
(N/mm2) |
590 |
550 |
620 |
620 |
590 |
660 |
Elongation |
(%) |
12 |
4 |
10 |
8 |
2 |
6 |
Modulus of Elasticity |
(psi x 106) |
45 |
40 |
46 |
48 |
45 |
50 |
Modulus of Elasticity |
(kN/mm2) |
310 |
280 |
320 |
330 |
310 |
345 |
Magnetic Properties |
|
slight |
none |
slight |
slight |
none |
slight |
Magnetic Permeability |
(µ) |
>1.05 |
<1.05 |
>1.05 |
>1.05 |
<1.05 |
>1.05 |
Thermal Expansion Coefficient |
(x10-6/K)(20°C-500°C) |
5.1 |
5.4 |
4.9 |
4.8 |
5.0 |
4.8 |
Thermal Conductivity |
(cgs) |
.20 |
.23 |
.24 |
.27 |
.32 |
0.26 |
Electrical Conductivity |
(% IACS) |
11 |
14 |
12 |
15 |
16 |
16 |
MIL-T-21014(D) |
class |
1 |
1 |
2 |
3 |
3 |
4 |
ASTM B777 |
class |
1 |
1 |
2 |
3 |
3 |
4 |
Table 2. HPM tungsten alloys
Inspection criterion |
Unit |
HPM 1700 |
HPM 1710 |
HPM 1701 |
HPM 1705 |
HPM 1750 |
HPM 1750 sheet |
Tungsten content |
% |
90.0 |
90.0 |
90.0 |
90.0 |
92.5 |
92.5 |
Balance |
|
NI, Fe |
Ni, Fe |
Ni, Cu |
Ni, Fe; Mo |
Ni, Fe |
Ni, Fe |
Density |
g/cm³ |
17.0 ± 0.2 |
17.0 ± 0.2 |
17.0 ± 0.2 |
17.3 ± 0.2 |
17.5 ± 0.2 |
17.6 ± 0.2 |
Hardness |
HV 30 |
≤ 320 |
≤ 320 |
≤ 320 |
≤ 360 |
≤ 325 |
≤ 460 |
Tensile strength (typical value) |
MPa |
850 |
850 |
670 |
900 |
840 |
870 |
Minimal yield strength |
MPa |
520 |
520 |
520 |
520 |
520 |
520 |
Elongation (typical value) |
% |
12 |
12 |
3 |
8 |
14 |
16 |
Young’s modulus (average value) |
GPa |
320 |
320 |
300 |
330 |
340 |
340 |
Median coefficient of linear thermal expansion
20 – 100 °C |
10-6/K |
6.1 |
6.3 |
6.0 |
4.5 |
5.5 |
5.5 |
20 – 300 °C |
10-6/K |
6.2 |
6.5 |
6.2 |
5.1 |
5.7 |
5.7 |
20 – 450 °C |
10-6/K |
6.3 |
6.6 |
6.4 |
5.3 |
5.8 |
5.8 |
Thermal conductivity |
W/mK |
≥ 70 |
≥ 70 |
≥ 90 |
≥ 70 |
≥ 75 |
≥ 75 |
Electrical conductivity (average value) |
%IACS
MS/m |
11
6.4 |
11
6.4 |
14
8.1 |
13
7.5 |
12
6.9 |
12
6.9 |
Specific electrical resistance (average value) |
µΩm |
0.16 |
0.16 |
0.12 |
0.13 |
0.15 |
0.15 |
Permeability, µ |
|
> 1.05 |
> 1.05 |
< 1.05 |
> 1.05 |
> 1.05 |
> 1.05 |
Table 3. Inspection criterion
Inspection criterion |
Unit |
HPM 1751 |
HPM 1760 |
HPM 1800 |
HPM 1810 |
HPM 1801 |
HPM 1850 |
HPM 1850W |
Tungsten content |
% |
92.5 |
92.5 |
95.0 |
95.0 |
95.0 |
97.0 |
97.0 |
Balance |
|
Ni, Cu |
Ni, Fe |
Ni, Fe |
Ni, Fe |
Ni, Cu |
Ni, Fe |
Ni, Fe |
Density |
g/cm³ |
17.5 ± 0.2 |
17.6 ± 0.2 |
18.0 ± 0.2 |
18.0 ± 0.2 |
18.0 ± 0.2 |
18.5 ± 0.2 |
18.5 ± 0.2 |
Hardness |
HV 30 |
≤ 325 |
≤ 325 |
≤ 332 |
≤ 332 |
≤ 332 |
≤ 340 |
≤ 340 |
Tensile strength (typical value) |
MPa |
690 |
870 |
830 |
830 |
700 |
830 |
890 |
Minimal yield strength |
MPa |
520 |
520 |
520 |
520 |
520 |
520 |
520 |
Elongation (typical value) |
% |
3 |
16 |
14 |
14 |
2 |
12 |
12 |
Young’s modulus (average value) |
GPa |
330 |
340 |
370 |
370 |
330 |
380 |
380 |
Median coefficient of linear thermal expansion
20 – 100 °C |
10-6/K |
5.7 |
5.5 |
4.9 |
5.2 |
5.4 |
5.1 |
4.8 |
20 – 300 °C |
10-6/K |
5.8 |
5.8 |
5.1 |
5.3 |
5.5 |
5.1 |
4.9 |
20 – 450 °C |
10-6/K |
5.9 |
5.9 |
5.2 |
5.5 |
5.6 |
5.2 |
5.0 |
Thermal conductivity |
W/mK |
≥ 85 |
≥ 75 |
≥ 80 |
≥ 80 |
≥ 85 |
≥ 75 |
≥ 80 |
Electrical conductivity (average value) |
%IACS
MS/m |
15
8.5 |
12
6.9 |
13
7.7 |
13
7.7 |
15
9.0 |
16
9.3 |
16
9.3 |
Specific electrical resistance (average value) |
µΩm |
0.12 |
0.15 |
0.14 |
0.14 |
0.11 |
0.10 |
0.10 |
Permeability, µ |
|
< 1.05 |
> 1.05 |
> 1.05 |
> 1.05 |
< 1.05 |
> 1.05 |
> 1.05 |
Fabricated Tungsten Alloys Enhance Oil and Gas Drilling
H.C. Starck Solutions’ high tech materials, technologies and development skill have been used to produce value added solutions to meet high performance demands of the oil and gas drilling sector. The company is a leader in the production of refractory metals such as niobium, molybdenum, tantalum, and tungsten.
H.C. Starck Solutions’ tungsten alloys is widely used in a number of applications such as balance weights, heat transfer, vibration absorbers, radiation protection and drilling bars. They possess the highest melting point compared to all other metals and their high density is equaled only by platinum, gold and a few other rare and expensive metals.
Tungsten’s Radiation Absorption Efficiency
The X-ray and gamma radiation absorption is in direct proportion to the shielding material’s density. Tungsten high density composites are more than 1.5 times as effective as lead and provide very efficient protection, especially where space is restricted.
Typical Properties
K1700 to K1850 materials offer a solution in numerous applications requiring concentrated weight or density in a restricted space. These lead-free components match legal requirements and recommendations to protect the environment.
Table 4. Alloy Designation
Alloy Designation |
Unit |
K1700 |
K1701 |
K1750 |
K1800 |
K1801 |
K1850 |
Tungsten content |
(%) |
90 |
90 |
92.5 |
95 |
95 |
97 |
Density |
(g/cm3) |
17 |
17 |
17.5 |
18 |
18 |
18.5 |
Density |
(lb/in3) |
0.61 |
0.61 |
0.63 |
0.65 |
0.65 |
0.67 |
Hardness |
(Rc) |
23 |
22 |
24 |
25 |
24 |
26 |
Ultimate Tensile Strength |
(psi) |
125,000 |
110,000 |
125,000 |
125,000 |
110,000 |
120,000 |
Ultimate Tensile Strength |
(N/mm2) |
860 |
760 |
860 |
860 |
760 |
830 |
Yield Strength |
(psi) |
85,000 |
80,000 |
90,000 |
90,000 |
85,000 |
95,000 |
Yield Strength |
(N/mm2) |
590 |
550 |
620 |
620 |
590 |
660 |
Elongation |
(% in 1 inch) |
12 |
4 |
10 |
8 |
2 |
6 |
Modulus of Elasticity |
(psi × 106) |
45 |
40 |
46 |
48 |
45 |
50 |
Modulus of Elasticity |
(kN/mm2) |
310 |
280 |
320 |
330 |
310 |
345 |
Magnetic Properties |
|
slight |
none |
slight |
slight |
none |
slight |
Magnetic Permeability |
|
> 1.05 |
< 1.05 |
> 1.05 |
> 1.05 |
< 1.05 |
> 1.05 |
Thermal Expansion Coefficient |
(×10-6/0 °C)(200 °C – 5000 °C) |
5.1 |
5.4 |
4.9 |
4.8 |
5.0 |
4.8 |
Thermal Conductivity |
(cgs) |
0.20 |
0.23 |
0.24 |
0.27 |
0.32 |
0.26 |
Electricial Conductivity |
(% IACS) |
11 |
14 |
12 |
15 |
16 |
16 |
AMS-T-21014 |
class |
1 |
1 |
2 |
3 |
3 |
4 |
ASTM B777 |
class |
1 |
1 |
2 |
3 |
3 |
4 |
Conclusion
Tungsten alloys surpass requirements of the following specifications:
- AMS-T-21014
- ASTM B777
- AMS 7725
H.C. Starck Solutions’ tungsten alloy materials can be designed and fabricated to customer’s specifications.
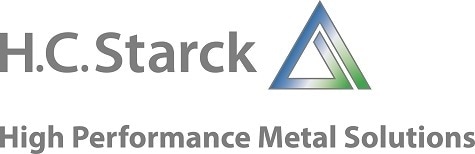
This information has been sourced, reviewed and adapted from materials provided by H.C. Starck Solutions.
For more information on this source, please visit H.C. Starck Solutions.