H.C. Starck Solutions provides niobium crucibles designed for use in the manufacture of synthetic diamonds, which can be used in a broad range of applications.
Block-like synthetic diamonds are required in some applications, which are manufactured by arranging a carbonaceous material in the niobium crucible and administering a combination of high pressure and high temperature (HPHT).
The niobium crucibles are fabricated from sheet material using deep drawing. The surface finish and quality of these crucibles are essential to the end quality of the synthetic diamonds. H.C. Starck Solutions’ development engineers have made major improvements to their niobium sheet in order to meet the deep draw challenges and quality requirements for synthetic diamonds.
.jpg)
Applications
The following are the key applications using synthetic diamonds:
- Machining
- Drilling
- Cutting
- Optical (Laser, IR, RF)
- Thermal management
- Detectors in high energy physics
- Magnetometry
- Waste water treatment
- Acoustics
- Ozone generators
Industries Served
Synthetic diamonds are used as an abrasive tool for non-ferrous and non-metallic materials. The following are key industries where it is applied:
- Construction - building infrastructure
- Stone - oil and gas exploration, mining, quarrying and building process
- Transportation - aviation and automotive sectors
- Machining - general industrial machining includes non-ferrous metals, plastic and other materials
- Electronics - ingot and wafer slicing includes glass, sapphire, silicon and other materials
- Woodworking - wood-based products such as furniture, flooring, and consumer products
Niobium Crucible Fabrication Process
The niobium crucible is a single-use container provided for the high pressure and high temperature (HPHT) method in fabricating synthetic diamonds. The initial step in the production of these crucibles is cold rolling and annealing techniques to create niobium sheet material. Using a punch method that utilizes one or more dies to fabricate the small crucibles, the niobium sheet is then deep drawn into crucibles.
.jpg)
Figure 1. Niobium sheet
H.C. Starck Solutions' niobium sheet can be rolled evenly, therefore preventing it from becoming thin, cracking, or failing during the deep drawing process. For the niobium sheet to be able to handle multi-axial tensile stresses without failure, it has to be very ductile and possess precise anisotropic mechanical properties to decrease wall-thinning during deep drawing.
The sheet’s anisotropy in is gauged by a number called the r-value (or Lankford coefficient), which attributes to the ratio of true strain as well as the width to true strain along the thickness during a tensile test.
Niobium Process
The niobium process involves:
- In-house skill in forging, rolling, machining, cutting and fabrication
- Skill in thermal processing
- Chemical, mechanical, and microstructure monitoring on site
- Reliable grain size and texture control
.jpg)
Figure 2. Nibium process
Avoiding Crucible Defects with Niobium Sheet
When designing a deep draw process, there are several variables to consider. An error setting on any of the steps could lead to defects in the final deep drawn part.
- Wrinkling in the wall happens when a wrinkled flange is drawn into the cup or clearances are very large
- Wrinkling in the flange happens due to low blank holding force
- Tearing happens from high tensile stresses that cause sheet thinning. Tearing also happens from high length-to-diameter (L/D) ratios, high pressure pad loads, sharp corner radii, and high punch loads
- Earring happens due to anisotropic material (i.e., directionality in properties)
- Surface scratches happen when the punch and die are not smooth or when process lubrication is insufficient
- Radial cracks in the flanges and edge of the cup due to inadequate metal ductility
- Orange peel or surface roughness happens in coarse grain metals.
A very commonly occurring defect is the “orange peel” effect caused by coarse grain sizes. A related niobium microstructure can reveal poor smoothness and flatness of the deep drawn cup as each grain tends to deform separately and non- uniformly.
Poor flatness and/or smoothness can lead to a synthetic diamond that needs extreme grinding. Similarly, a coarse grain structure tends to cause tearing of the sheet during deep draw operations.
Grain Stabilized Niobium (GSNb)
H.C. Starck Solutions’ grain stabilized niobium sheet is a single-phase micro-alloyed niobium material. It has a grain size about two ASTM numbers finer than commercial grade niobium. This decreases the “orange peel” effect during drawing and forming operations, making it highly suitable for deep draw applications where uniform deformation is needed.
GSNb is used broadly in the industrial diamond sector. Furthermore, its corrosion resistant qualities match that of commercial grade niobium for applications in the chemical process sector.
GSNb can also be used in sputtering targets for architectural glass and fiber optic applications. In nuclear reactors it has excellent corrosion resistance and low thermal neutron cross-section. It is an outstanding getter and can be used in high temperature vacuum furnaces. It is resistant to attack by the molten alkali metals found in sodium vapour lamps.
Optimizing deep drawing capabilities
The niobium sheet’s deep drawing capabilities are affected by the quantity of silicon (Si) added to the niobium composition. The Si concentration affecting the r-value or drawability in niobium sheet is studied in detail.
Thick sheets of 0.01” (254µm) with Si concentrations between 40 and 135ppm were measured in tensile testing, and it was discovered that the average r-value reduces linearly as the Si concentration increases.
When the Si concentration is greater than 85ppm, a value of less than 1.0 can be obtained. Moreover, it was found that the Si concentration has its maximum effect on r-0 degree and r-90 degree texture measurements, and it is recommended that Si atoms may be pinning grains with <100>//RD and hence impact the r-value.
For perfect deep drawing features, an optimal Si concentration of 85ppm was established to ensure that the mean r-value is higher than 1.0 at the same time, maintaining a small grain size. Good control of the Si concentration is essential to attain stable performance during deep drawing.
.jpg)
Figure 3. EBSD pole figure results for 60ppm Si annealed Nb sheet of 254µm
As the Si-concentration increases, the mean r-value decreases from greater than 1.0 to lower than 1.0, with an optimal Si concentration of 85ppm.
Corrosion resistance
GSNb’s corrosion resistance matches that of commercial grade niobium and can be used in all applications where commercial grade niobium is used. Similar to tantalum, GSNb is resistant to several types of acids except for hydrofluoric; however its resistance is not as strong as tantalum to strong acids at high temperature. It is recommended that GSNB should not be used with strong bases (alkalis).
Available forms and properties grain stabilized niobium
Material |
Thickness |
Width |
inches |
mm |
inches |
mm |
Foil |
0.001 - 0.015 |
0.025 - 0.381 |
up to 12 |
up to 304.8 |
Sheet |
0.015 - 0.1875 |
0.381 - 4.763 |
up to 36 |
up to 914.4 |
Plate |
0.1875 - 1 |
4.763 - 25.40 |
Common widths |
Several variations of thickness and width are available to meet the requirements of the application.
Physical Properties of Niobium
Physical Properties |
|
Atomic Number |
41 |
Atomic Weight |
92.91 |
Density |
8.47 gm/cc (0.31 lbs/in2) |
Melting Point |
2468 °C |
Coefficient of Expansion (20°C – 100°V) |
7.1 x 10-6/°C |
Specific Heat (27°C) |
0.065 cal/gm/°C |
Thermal Conductivity |
0.125 cal/sec-cm-°C |
Electrical Resistivity (0°C - 100°C) |
14.5 microhm-cm |
Crystal Structure |
bcc |
Mechanical Properties of GSNb (annealed)
Mechanical Properties |
|
Tensile Strength |
18,000 psi (125 MPa) minimum |
Yield Strength |
10,500 psi (73 MPa) minimum |
Elongation |
20% minimum (=> 0.010” thick)
15% minimum (< 0.010” thick) |
Hardness (Typical)* |
HV 60-100 |
Grain Size (ASTM)* |
6 or finer (45 ums) for thicknesses < 0.010” |
*Additional information not included in ASTM B363
GSNb meets the mechanical properties stipulations of ASTM B393 Type 2 Commercial Grade Niobium (UNS RO4210).
Chemistry
Element |
ppm (max) |
Element |
ppm (max) |
C |
100 |
Si |
100 |
O |
250 |
W |
500 |
N |
100 |
Ni |
50 |
H |
15 |
Mo |
200 |
Zr |
200 |
Hf |
200 |
Ta |
3000 |
Ti |
300 |
Fe |
100 |
Nb |
balance |
Other trace elements are less than 50ppm each.
The elements CONH are tested at the ingot stage and may be higher in finished material.
Fabrication of GSNb
- Machinability - GSNb is quite challenging to machine; however it can be machined using high rake angle tools, slow feeds and speeds, and water-soluble oils.
- Weldability - GSNb can be resistance welded to other metals such as titanium, tantalum, platinum, nickel, and niobium as well as to itself. It can be welded using GTAW (TIG) using proper shielding and cleanliness methods. It can also be electron beam (EB) welded.
- Heat Treatment – it has to be performed in vacuum only. GSNb will recrystallize at temperatures above about 1650°F (900°C).
General Applications of GSNb
Sheet/strip/foil GSNb are used for forming applications such as cups, crucibles, and formed parts. It is be applied in any area where commercial grade niobium can be applied but requires better forming and surface finish.
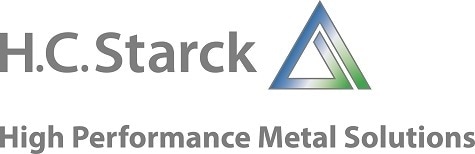
This information has been sourced, reviewed and adapted from materials provided by H.C. Starck Solutions.
For more information on this source, please visit H.C. Starck Solutions.