Dynamic mechanical analysis (DMA) is an analytical technique used for measuring the modulus (stiffness) and damping (energy dissipation) characteristics of materials that are deformed due to periodic (oscillatory) stress.
There are certain components that are critical to the resultant performance and design of a dynamic mechanical analyzer. These components include the drive motor that delivers the sinusoidal deformation force to the sample material, the displacement sensor for measuring sample deformation upon force application, the sample clamps, the temperature control system and the drive shaft support and guidance system which transfers drive motor force to the clamps holding the sample.
The TA Instruments DMA 2980 is based on a distinct patent pending design that adjusts the combination of critical components. The schematic diagrams of the components of DMA 2980 and a “traditional” DMA are shown in the Figures 1 and 2, respectively. The article below discusses the benefits of the DMA 2980 design.
.jpg)
Figure 1. DMA 2980 Key Design Elements
.jpg)
Figure 2. Traditional DMA Design Elements
Drive Shaft Support and Guidance System
The drive shaft in traditional DMA is supported and triggered using mechanical springs that can be flexed to provide sinusoidal force to the sample from the drive motor. The approach has two major disadvantages. The finite stiffness of the spring interferes with the measurement. The spring contribution can be calibrated and eliminated from sample modulus calculations, but it affects the precision and accuracy when materials have stiffness nearly equivalent or less than that of the spring. A similar situation may occur in low modulus materials such as elastomers and also with high modulus materials based on sample dimensions.
The mechanical spring has a limited travel range which is 1mm or less. The position of the drive shaft needs to be adjusted at the time of the experiment using a lead screw and a stepper motor to test larger samples and/or larger deformations. However, as the resultant curves are uneven and not continuous, subtle transitions are difficult to evaluate.
The DMA 2980 drive shaft, however, is supported by the drive motor and driven by eight air bearings divided into two sets of four each across the top and bottom parts of a rectangular air bearing slide. The flow of pressurized air or nitrogen via these bearings generates a thin layer of air between the bearing surface and slide surface. The slide can move freely and smoothly in a vertical direction, but lateral movement is restricted by the high compression resistance of the thin air layer. Further, the unique rectangular design of the slide prevents the chances of torquing of the slide. The DMA 2980 has a continuous vertical travel range of 25mm which ensures evaluation of even large samples or large displacements to determine linear viscoelastic region or allows fatigue testing. The inherent resistance of the air bearing to vertical movement is low such that thin films and fibers can also be tested.
The porous graphite air bearings of the DMA 2980 facilitate low susceptibility to contamination and low air consumption. They can be operated with the help of “house air” or air from an optional compact compressor.
Drive Motor
The non-contact, direct drive motor of the DMA 2980 provides the oscillatory force to deform the sample materials. The motor is built based on the high performance composites and other materials ensuring low system compliance and allow the motor to provide reproducible forces in a range of 0.0001N to 18N. The motor is thermostated to remove any amount of heat even while using large oscillation amplitudes along with high deformation forces. Furthermore, the electronics available with the motor allow adjustments of current to the motor in small increments. This ensures measurements at amplitudes as small as 0.5m.
Optical Encoder
The displacement sensor in traditional DMA’s is a linear variable differential transformer (LVDT) used for measuring small displacements with respect to the relative position of a metal core between two secondary coils. For any LVDT, displacement sensitivity can be as good as 1nm, but over a limited displacement range. In general, the resolution of LVDT is 1 part in 200,000, which means the maximum displacement range of 200m without a stepper motor and lead screw is necessary to achieve 1nm resolution. Further, LVDT’s tend to become non-linear at the extremes of travel of the core which can reduce the range. LVDT measurements can also be subjected to external interference from other sources such as the drive motor.
The DMA 2980 makes use of an optical encoder for measuring displacement. However, optical encoders can provide a greater resolution than LVDT’s based on the light diffraction patterns via gratings. The resolution of the DMA 2980 optical encoder is 1 part in 25,000,000 or 1nm over the entire displacement range. The high resolution of oscillation amplitude indicates excellent E’ and E” precision (1%) as well as tan δ ( ) sensitivity (0.0001). Even with high drive force of the DMA 2980 motor, only very small oscillation amplitudes can be measured. However, using high displacement resolution, high modulus materials can be evaluated.
Other Components of DMA 2980
The following are the other components critical for the design of a quality DMA:
- Temperature control components – The DMA 2980 is provided with a bifilar wound furnace along with a gas cooling accessory (GCA), covering a wide temperature range from -145°C to 600°C. The furnace features excellent temperature precision for transitions (±1°C) and an automated “swing-away” movement that ensures easy access to the sample area without increasing the footprint. It is provided with an automated air cooling between experiments, which ensure fast turnaround time.
- Sample clamps – The versatility of a DMA design is based on the available deformation and sample clamping modes. The DMA 2980 is provided with a wide range of deformation modes such as tension, compression, shear sandwich, 3 point bend and single/dual cantilever, and a number of clamp sizes so as to accommodate sample materials ranging from 0.57tex (5 denier) single fibers to films as thin as 1m to test bars.
The DMA 2980 clamps are provided with two important features as follows:
- Designed using “finite element analysis” providing high stiffness and low mass
- Designed for easy loading and adjustment
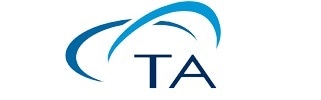
This information has been sourced, reviewed and adapted from materials provided by TA Instruments.
For more information on this source, please visit TA Instruments.