Polymers are viscoelastic fluids that are either elastic or viscous, depending on how fast they flow or deformation in the process.
The viscoelastic phenomenon, as shown in Figure 1, can be easily demonstrated through the silicone putty test. When a silicone ball is subjected to rapid deformation i.e. bouncing on a table, the silicone ball behaves like an elastic body. This is the recoverable elastic deformation which stores the energy to make the ball bounce. Upon resting the silicone ball for a long period of time, the material begins to flow due to gravity, which makes it behave like a viscous fluid. The material’s behavior depends on the time scale of the deformation, or on the ratio of process time. Material time is referred to as Deborah or Weissenberg number. The material shows a viscous behavior if the material time is short with respect to the process time. The elasticity of the fluid is increased if the Weissenberg number equals one or greater.
.jpg)
Figure 1. The filled polydimethylsiloxane (PDMS) behaves predominantly elastic if deformed for a short period of time and predominantly viscous if subjected to gravity over a long time period.
The viscosity is the key parameter for most of the processes. A material which processed easily on a film blowing line twenty years ago may not work at all on current lines, which work at a much higher draw speed. The elastic behavior of the material under shorter process times has a negative effect on its processiblity. Similar behavior can also be observed for the flow in the mold during the injection molding process. During rapid cooling, increased elasticity can result in more locked in orientation.
The rheology of the material needs to be controlled within the specified range to ensure a smooth operation process. The structure– rheology relationship is critical for the polymer development during processing. The main objective of the design engineer is to tweak the material structure to ensure better processing performance without affecting the final product’s performance. Owing to its sensitivity to changes in material’s structure, rheology can also be used to control the process.
Structure–Rheology Relationship
The materials of the same grade but different batches can be processed in a different manner. The transformation process reacts to small changes in the material i.e. the rheology of the polymer melt is sensitive to small changes in the polymer structure. Due to the sensitivity of rheology of the condensed phase to structure, rheology is considered as the most convenient method to characterize polymers. Even small amounts of a high molecular weight polymer can affect the processing behavior and so does the melt rheology.
Molecular weight distribution (MWD), molecular weight (MW) and branching are the important parameter used for defining rheology of the polymer melts. While the increase in molecular weight improves the viscosity, any changes in the molecular weight distribution and branching affects the elasticity of the melt. The time dependence is affected by both. Using capillary and rotational rheometers, viscosity measurements are usually carried out. These two methods shown in Figures 2 and 3 are critical for polymer rheological characterization.
.jpg)
Figure 2. In a capillary rheometer the material is forced through a slit or round die. From the pressure drop and the volume flow rate, a steady state viscosity as a function of the applied rate (piston speed) or stress (applied pressure) is measured.
.jpg)
Figure 3. In a rotational rheometer the sample is sheared between two plates or a cone and plate geometry. The viscosity is calculated as the ratio of the applied stress and the applied deformation rate (rotation speed). The rotational rheometer, in contrast to the capillary rheometer, measures time dependent material behavior also.
The viscosity of a polymer melt is a function of the average molecular weight Mw to the power of ~3.4. The Melt Flor Rate, or MFR in polymer processing is used to characterize the polymer melt. Although the MFR shown in Figure 4 is a common measurement method, it is not a pure viscosity measurement. A material with the correct MFR can be achieved by blending the offspec material. However, the viscosity and the elasticity of the blended material can be quite different, which is evident in the processability. Despite this MFR is the key factor used in the characterization and specification of polymer grades. The online measurement of the MFR has turned out to be a major issue in polymer manufacturing while complete QA concepts have been developed around the MFR measurement as shown in Figure 5. Online rheometers have been frequently used by the polyolefin production lines to measure the MFR.
.jpg)
Figure 4. The MFR is a standardized die with a barrel to preheat the sample (ASTM D1238 and DIN 53 735). The material is forced through the die by applying a weight of 2.14 or 21.4 kg. The measured quantity is the weight of the material flowing through the die within a given time period. The MFR is not only a measurement of the viscous effects in the die, but incudes also contributions of the die inlet and exit effects.
.jpg)
Figure 5. On-line rheometers are sensors inserted into the process line to monitor key parameters in order to allow controlling product uniformity and adherence to the desired specifications. On-line rheometers operate as return to stream or return to waste sensors. Depending on the die geometry, on-line rheometers can provide a real time measurement of MFR or shear viscosity as a function of rate. Equipped with an optical window to do NIR, UV etc. measurements the on-line rheometer can measure also additive levels, degradation, color, etc.
Considering viscosity alone is not enough while developing materials with appropriate processing behavior. Elasticity and time dependence of a polymer are of equal importance while controlling the processability of a polymer melt. The dynamic mechanical analysis (DMA) of polymer melts is a method that facilitates complete rheological response of a material. The technology as shown in Figure 6 is now being widely used by the design engineers. The DMA provides information on the polymer morphology and secondary transitions in the solid state. The solid’s behavior does not depend on the polymer structure.
.jpg)
.jpg)
Figure 6. Dynamic mechanical testing involves the application of an oscillatory strain (or stress) to a material and to measure the resultant stress (or strain). The phase shift and the ratio of stress amplitude and strain amplitude allow the calculation of the dynamic moduli, the storage and loss modulus as well as the complex viscosity as a function of frequency.
The DMA measurement results to a material fingerprint which can be used for calculating elasticity, viscosity and time dependence of material at melt temperatures. While the viscosity is correlated with the weight average molecular weight Mw, the elasticity depends on the molecular weight distribution. During an oscillatory test, the material is mechanically probed at varying frequencies and the polymeric chains and chain segments respond to the external stimuli. Therefore, the dynamic mechanical analysis can also be referred as mechanical spectroscopy. Figure 7 shows a typical frequency sweep.
.jpg)
Figure 7. The frequency sweep provides a characteristic fingerprint of the material. At higher frequency, G’ shows a plateau value referred to as plateau modulus. The plateau value relates to the average molecular weight between entanglements Me. At low frequency, the loss modulus is a measure of the materials viscosity (G”/ω) and the ratio G’/ G”2 of the elasticity.
DMA is a highly sensitive method used for characterizing linear polymers with respect to MW and MWD. Commercial software packages are also available for calculating MW and MWD directly using the oscillatory data.
Using Rheology to Produce Better Final Products
For processes involving free surface deformations of the material, the elongation viscosity is more important than the shear viscosity as shown in Figure 8. Some of the applications of rheology include extrusion, film blowing, injection molding, etc.
.jpg)
Figure 8. The elongation viscosity is determined by stretching a thin polymer bar and recording the force. The extensional viscosity fixture can be used to perform elongations of a Hencky strain of 4 /5/ . The LDPE sample shows the typical strain hardening effect above eH = 3.
The strain hardening nature of polymers is necessary for the processability at the time of film blowing and fiber spinning process. The effect of strain hardening needs to be controlled to ensure film and fiber thickness tolerances thereby stabilizing the filament and the bubble during the elongation process.
Pressure sensitive adhesives (PSA) are polymer blends optimized through rheology to achieve higher viscosity levels and prevent flow under application temperatures as well as lower levels to flow into the substrate under the applied pressure as shown in Figure 9.
.jpg)
Figure 9. The DMA trace of a PSA adhesive as a function of temperature allows determining the critical application parameters. 1) The modulus at application temperature (G’=2x104 N/m2) /6/; 2) the lowest application temperature limited by the low temperature transition (T= 10°C); 3) the lowest processing temperature defined by the cross over point of G’and G” /7/.
Reactive materials are formed from a low viscosity fluid to a solid material at the time of processing. Rheology is ideal for evolution of the viscosity during cure. The existing rheometer can be programmed to simulate cure cycles and optimize the temperature and pressure profiles in the mold. Any changes in the material can be detected, and the process parameters can be adjusted for the given batch. Using dynamic mechanical data, the gel point as shown in Figure 10 can be determined.
.jpg)
Figure 10. The Gel point of a resin (epoxy resin shown here) can be measured using the DMA technique. The curing is followed in time by applying a small amplitude deformation to the sample and recording the dynamic moduli. The gel point can be defined as the time when G’ and G” cross over.
The application of rheology in solving material, processing and performance problems is illustrated in Figure 11. The rheology-polymer structure relation proves that rheology is an ideal tool for designing materials with specific processing and end-use performance. The rheology of the melt provides information on the processability, while the rheology of the solid and melt phase provides information on the end product performance. As a result of the viscoelastic nature of the melt that may lead to wanted/ unwanted anisotropy during flow, the final product depends on the processing of material.
.jpg)
Figure 11. This diagram shows how rheology can be used to correlate end-use and processing performance to the polymer structure. Rheology is a key characterization technique for developing materials with the desired physical properties and for controlling the manufacturing process in order to ensure product quality.
Conclusion
Rheology is capable of evaluating even small changes in polymer structures and hence it is suitable for polymer characterization. The rheology-structure relationship is critical for the development of new materials.
Due to the sensitivity of the process to the polymer structure, the material needs to be controlled in tight tolerances to ensure good processability. Rheology is an ideal tool for process and quality control.
The structure-rheology relationship is ambiguous for complex materials as the rheological behavior does not represent the polymer structure uniquely. In this case, additional measurements need to be combined with the rheological measurement in order to achieve contributions of different structure elements. Optical, thermal, dielectric, etc. methods are important parameters to be used along with the rheological measurement.
However, rheology is a standard technique employed in the polymer industry for the characterization of materials with an aim to develop new and improved materials having desired processing and end-use properties.
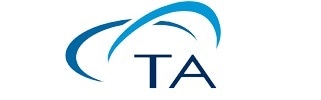
This information has been sourced, reviewed and adapted from materials provided by TA Instruments.
For more information on this source, please visit TA Instruments.