When SilcoGuard® 1000 is applied on the internal surfaces of vacuum systems it significantly decreases outgassing rates, and provides a productivity advantage to process chambers, which need faster and efficient evacuations. SilcoGuard 1000 layer greatly reduces outgassing by steel parts in ultra high vacuum (UHV) systems.
The SilcoGuard 1000 layer can be applied to and combined into the steel surface, so that the layer acts as a barrier, isolating any materials captured on or in the steel, and blocking them from entering the UHV environment, without freeing any contamination of its own.
Advantages
SilcoGuard® 1000 offers the following advantages:
- Reduces process time by decreasing vacuum pump-down times by 2.5X
- Enhances process yields by decreasing ion contamination and moisture
- Adds value by reducing or eliminating expensive equipment burn-in or stabilization
- Easy-to-use, and it can enhance the performance of current components using SilcoTek custom coating service.
Figure 1 displays the remarkable improvement gained using SilcoGuard 1000-treated parts in a UHV assembly, in comparison to heat-cleaned parts. The SilcoGuard 1000 coated part showed a 14-fold lower outgassing rate than the heat-cleaned part after 10 hours under vacuum at 61 °C.
The SilcoGuard 1000-treated parts help to achieve and maintain a UHV environment with limited pumping capacity, and with little to no bake-out or pre-cleaning.
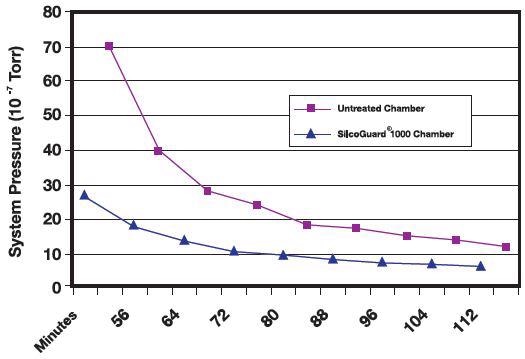
Figure 1. Compares pump-down rates for a SilcoGuard 1000 treated vs. an untreated chamber. SilcoGuard 1000 will reduce pump down times by 2.5x or more, compared to untreated chambers. (Data courtesy of Elvac Laboratories).
Speeding-Up Moisture Dry-Down Using SilcoGuard 1000
Gas transfer systems used in the semiconductor sector need low moisture content. Data for dry-down and wet-up experiments, measuring the comparative response time for moisture content change in treated electropolished stainless steel tubing and regular 316L stainless steel tubing, reveal the advantage of applying SilcoGuard 1000 treated tubing versus untreated tubing.
Figure 2 illustrates the comparison among wet-up curves for SilcoGuard 1000 treated electropolished, standard tubing, and untreated electropolished tubing.
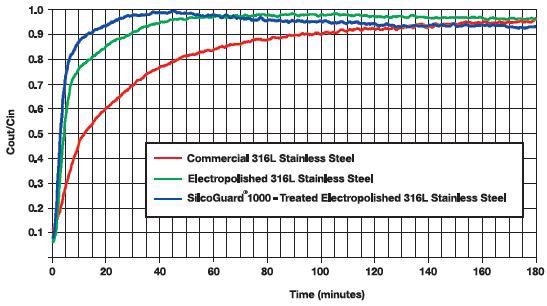
Figure 2. SilcoGuard 1000 treated electropolished tubing stabilizes at 1 ppm moisture much faster than conventional surfaces. (Data courtesy of O’Brien Corporation).
Within 30 minutes, the treated electropolished tubing reached the 98% saturation limit, compared to the 60 minutes taken by electropolished tubing. Regular tubing was able to achieve just a 96% uptake in a span of 180 minutes.
Moisture dry-down curves reveal that the SilcoGuard 1000 treated electropolished tubing accomplished dry-down in 35 minutes, while electropolished tubing needed 65 minutes, and regular tubing needed 175 minutes. In Figure 3, the dry-down performance is compared for tubing saturated with 10 ppm of moisture.

Figure 3. SilcoTek treated electropolished tubing dries much faster than conventional surfaces.
The SilcoGuard 1000 layer is sturdy and sufficiently long lasting to withstand the sealing prerequisites required to obtain a UHV environment. Figure 4 illustrates the knife-edge of a SilcoGuard 1000-treated Conflat® sealing surface.
The knife edge enters and seals in the copper O-ring installed within the Conflat® surface. Even after numerous cycles of this sealing process, the SilcoGuard 1000 layer stays intact.
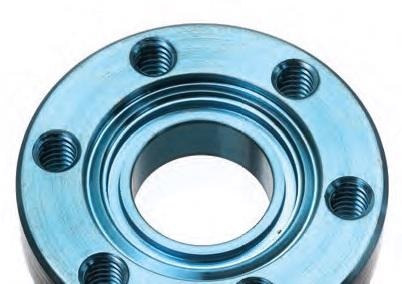
Figure 4. The durable SilcoGuard 1000 layer will withstand the sealing requirements of UHV, maintaining knife-edge integrity.
Conclusion
SilcoGuard 1000 is a high-purity silicon chemical vapor deposition (CVD) surface treatment, which can be used on exisiting UHV systems. SilcoGuard 1000 significantly minimizes outgassing in stainless steel UHV systems.
The system’s hydrophobic nature allows for rapid, effective pumping of moisture and other general surface contaminants from UHV systems.
Better process yields, enhanced process equipment productivity, and excellent process efficiency are the results of reducing contamination.
Download the brochure for more about SilcoGuard surface treatment from SilcoTek.
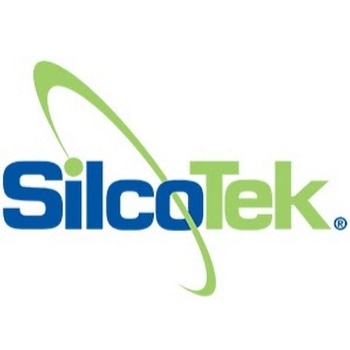
This information has been sourced, reviewed and adapted from materials provided by SilcoTek.
For more information on this source, please visit SilcoTek.