Coke formation is reduced by SilcoKlean®1000 by preventing the exposed metal surfaces from catalyzing fuel into carbon filaments. Compared to untreated 316 stainless steel surface, it is found that carbon coking or fouling is reduced by 8-fold using SilcoKlean 1000 (Figure 1).
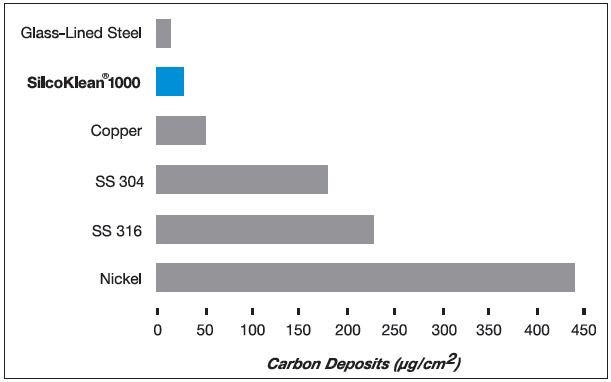
Figure 1. SilcoKlean 1000 treatment reduces coking up to 8-fold. (Data courtesy of The Pennsylvania State University.)
SilcoKlean®1000 surface treatment reduces coke formation 8-fold
In addition to preventing the buildup of filamentous coke, a SilcoKlean 1000 treated surface makes the removal of other forms of coke binding to a heated surface simple. A number of studies have demonstrated the removal of carbon deposits from a SilcoKlean 1000 treated surface by sonicating it in common solvents. This simplifies the maintenance processes and extends the maintenance cycles.
SilcoKlean 1000 treatment
SilcoKlean 1000 increases the maintenance cycles for engines, and at the same time, sustains high temperature capability, leak-free conditions, and high dimensional tolerances, making it an appropriate treatment for:
- valves
- heat exchangers
- fuel injection nozzles
- EGR systems
- turbine shafts
- pistons
- jet engine nozzles
- oil and fuel lines
Carbon deposits
The accumulation of carbon-based deposits on combustion process systems or components, known as carbon coking or fouling, is a significant contributor to high maintenance costs (Figure 2). Shortened maintenance cycles, engine failures, and unplanned repairs are caused by coking. For example, manufacturers of diesel engines have proved that coking on pistons leads to expensive rebuilds and shortened engine life. Personnel in charge of aircraft maintenance are currently discovering significant coking in nozzles, oil lines, and fuel lines.
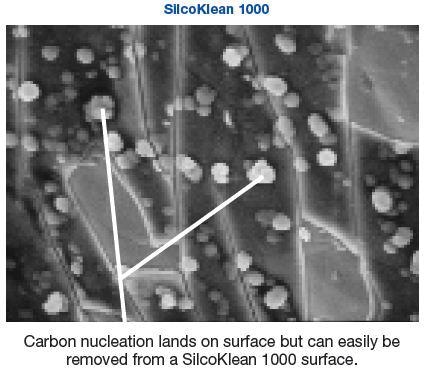
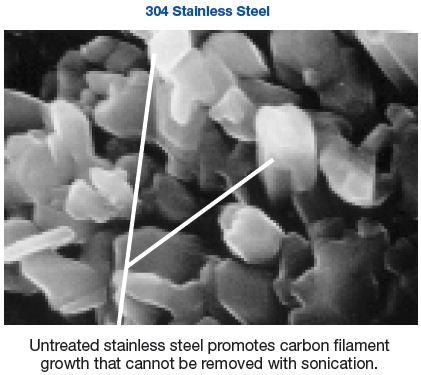
Figure 2. Carbon deposit from JP-8 fuel on various types of tubing (500°C, 500psi, 1cc/min. flow rate). (Data courtesy of The Pennsylvania State University)
According to various studies, the exposure of oils and fuels to temperature over 200°C leads to coking and there is a considerable increase in the rate of coking at temperatures over 400°C. High temperature exposure occurs due to lack of coolant flow to take away the excess amount of heat when the process or engine is shut down.
SilcoKlean 1000 treatment for components susceptible to coking
SilcoKlean 1000, a chemical vapor-deposited (CVD) layer, helps to reduce coking of specialty alloys, stainless steel, and steel. A flexible, amorphous silicon layer is formed by a novel, non-line-of-sight CVD process. This layer can be applied to even the most intricate surface by diffusing into the metal lattice without compromising the tight dimensional tolerances. SilcoKlean 1000 layer flexes with the metal surface, and creates leak-free seals even at extreme temperatures.
Conslusion
Test data highlight that catalytic coking can be reduced 8-fold with SilcoKlean 1000 treatment. Extending the maintenance cycles without considerable re-engineering is possible with the application of the SilcoKlean 1000 treatment on existing components.
Download the brochure for more about SilcoKlean® coatings from SilcoTek.
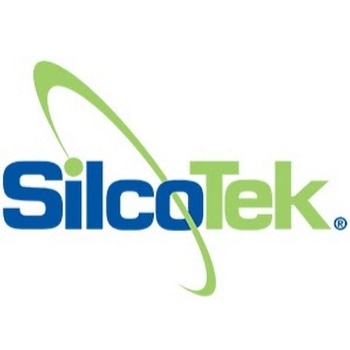
This information has been sourced, reviewed and adapted from materials provided by SilcoTek.
For more information on this source, please visit SilcoTek.