To take care of issues relating to corrosion and surface activity, special alloys or surface treatments are used. SilcoTek offers surface treatments to resolve issues with reactivity and corrosion over a broad range of applications.
SilcoTek® Surface Treatments
SilcoTek® surface treatment helps to enhance sampling and transfer component performance. It is simple and can be used on exisiting equipment.
It is economical with low cost corrosion resistance compared to specialty alloys. It helps achieve excellent analytical performance, facilitating the characterization of parts-per-billion level sulfurs in the lab or field. It is versatile, and can be applied in a number of environments and at high temperature ranges.
Table 1 provides a list of applications in which SilcoTek treatment reduces corrosion or prevent adsorption of active compounds.
Table 1. Applications in which SilcoTek treated sample pathway components minimize corrosion or prevent adsorption of active compounds
Sulfur compounds in:* |
automotive exhaust
diesel fuels
ethylene
liquefied petroleum gas
oil & gas exploration
refining
wines and beers
beverage grade Co2
environmental samples
gasoline
natural gas (odorants)
propylene
stack gas emissions |
Nitric oxide (NOx) compounds in:* |
automotive exhaust
stack gas emissions |
Mercury compounds in:* |
crude oil refining environmental samples
exhaust oil & gas exploration
stack gas emissions from coal fired electric power plants |
Corrosive environments:** |
hydrochloric acid hydrogen peroxide
off-shore platforms refining
seawater |
Moisture hold-up in high purity sampling lines** |
sample systems
gas delivery systems
process systems |
*SilcoNert®2000 treatment.
**Silcolloy®1000 treatment.
Accurate Feedstock or Process Sampling
Adsorption issues in sample pathways can often be linked to the fittings and tubing used to transfer the sample to the analytical instrument. In cases where active compounds are used in applications, it is recommended that treated fittings and tubing should be used.
To ensure good inertness and low surface area, SilcoTek treatments need to be applied to electropolished tubing. Figure 1 illustrates uptake and release curves for 500 ppbv of methyl mercaptan (an active sulfur compound) in a gas stream passing via a number of tubing substrates.
SilcoNert 2000 (Siltek/Sulfinert) treated tubing decreases uptake by orders of magnitude, relative to non-treated stainless steel tubing.
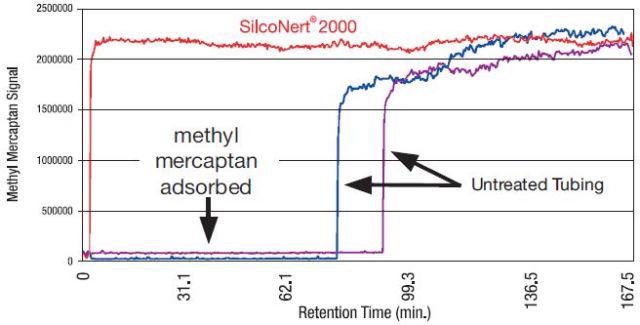
Figure 1. SilcoNert 2000 treated tubing allows for rapid detection.
Reduce Maintenance Cost, Extend Stainless Steel System Life
Silcolloy®1000 treatment is ideal for expensive alloys in corrosive environments. This treatment helps to extend the service life of a component while decreasing the frequency of preventive maintenance, ensuring process or sample stream purity.
Silcolloy 1000 enhances corrosion resistance up to 10 times over untreated 316 stainless steel (per ASTM G48 Method B, Figure 2). The cost of Silcosteel®-CR treated components is 85% less, compared to super alloys.
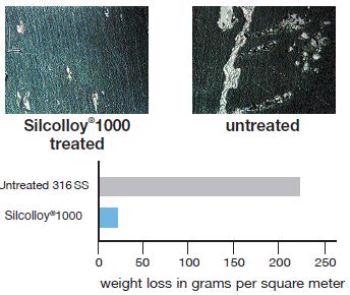
Figure 2. Silcolloy 1000 treated 316L stainless steel coupons show no crevice corrosion and only slight pitting corrosion after 72-hour exposure to ferric chloride; untreated coupons exhibit severe crevice corrosion
(per ASTM Method G48, Method B).
Figure 3 illustrates the results of a 4000-hour salt spray test on Silcolloy 1000 treated 316L stainless steel and untreated 316L stainless steel. Virtually no change was observed in the case of Silcolloy 1000 treated material.
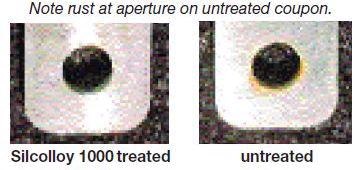
Figure 3. Silcolloy 1000 treated 316L stainless steel coupons show no sign of attack after 4000-hour salt spray exposure, per ASTM B117.
Figure 4 displays a comparison of lifetime costs in a general process system, and reveals how Silcolloy 1000 treatment can decrease the total lifetime cost of the system by hundreds of thousands of dollars.
Although the primary cost of an untreated stainless steel system is less than that of a comparable Silcolloy 1000 system, the total lifetime cost, including replacement cost due to corrosion, is almost twice that of a Silcolloy 1000 treated system. High performance alloy systems provide superlative corrosion performance, but the primary material cost can be up to six times that of a comparable stainless steel system.
Silcolloy 1000 treatment has increased the life of process systems in gas and oil production, petrochemical processing, oil refining, food and beverage processing, aerospace equipment, and laboratory testing.
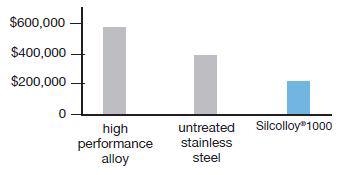
Figure 4. Silcolloy 1000 demonstrates significant cost savings, compared to untreated stainless steel or alloys (US dollars).
Treat Whole Sample Pathway for Maximum Effect
Valves, fittings, and other system parts can greatly contribute to adsorption and corrosive attack. SilcoTek treatment of the whole pathway will decrease expensive sample loss or corrosion.
Fittings
Connections can be a source of sample loss and adsorption, and there is advantage in using SilcoTek surface treatment on several of these parts. For instance, Silcolloy 1000 treatment will prolong the service life of system fittings, and tubing in corrosive environments.
Valves
The sample flow path via a valve can be difficult, extending contact between the valve components and sample stream. SilcoTek surface treatments have been used on several valve geometries to remove adsorption to stems, bodies, diaphragms, or other parts.
Filters
Frits and other filtering devices capture particles and stop them from entering the analytical tool, but they also very efficiently adsorb active parts in sample streams. Their large surface areas allow increased sample/system contact by orders of magnitude. SilcoNert 2000 (Siltek/Sulfinert) treatment of filters and frits provides an inert flowpath. SilcoTek chemical vapor deposition technology ensures that the treatment enters even the tiniest pores in sintered metal frits.
Sample Vessel Equipment
It is important to use SilcoTek treated sampling containers while transporting samples taken from a process stream to the laboratory for analysis, to avoid active parts from adsorbing to valve, vessel, or outage tube surfaces.
Probes
Sampling probes are applied in numerous applications, such as sampling natural gas, or other process streams. An untreated probe influences the active surface area in the system, so it must be considered when spotting possible adsorption sites during active stream transfer.
Heated Lines
A heated “trace line” comprises basic grade or electropolished tubing, which has been insulated and bundled with heating devices to ensure the sample is transferred at a stable temperature. The lines are used in several gas stacks and other remote sampling points at which a sample is transported via an outdoor environment. Active compounds in the sample can rapidly be adsorbed onto the tubing. SilcoTek surface treatment stops the adsorption of active compounds.
Conclusion
SilcoTek surface treatments arrest corrosion or adsorption of active compounds in process systems. These treatments should be considered, especially in applications demanding the sampling, transfer or testing of corrosive or active streams.
Download the brochure for more about Silcolloy® treatments from SilcoTek.
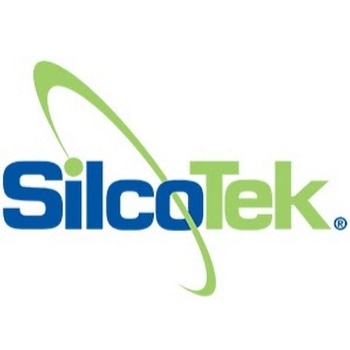
This information has been sourced, reviewed and adapted from materials provided by SilcoTek.
For more information on this source, please visit SilcoTek.