The semiconductor industry is currently driven as much by cost, productivity, and speed as it was previously by performance. As output is continuously increasing, manufacturers need to deliver higher volumes at faster rates, ensure the stabilization of processes with large data volumes, and maintain better purity standards.
As a result, process reliability, reuse of equipment, and faster technology deployment are becoming crucial. This article discusses a surface treatment process developed by SilcoTek for semiconductor applications.
SilcoTek’s Coatings
SilcoTek’s 3D non-line-of-sight chemical vapor deposition (CVD) processes, which have been patented, offer flexible and high purity layers, with better adhesion to the common materials used to fabricate semiconductors such as; stainless steel, aluminum, and ceramics. The layer can conform to the most intricate component geometries.
The SilcoTek® surface possesses the ability to deform with tubing surfaces to accommodate radius bends and the use of leak-free seals.
Silcolloy® 1000 Treatment Enhances Corrosion Resistance
Tests conducted at independent laboratories show that Silcolloy® 1000 treatment enhances rust resistance up to 10 times more than uncoated type 316L stainless steel (Figures 1 and 2). The Silcolloy 1000 treatment is compatible with the various chemicals employed for semiconductors.
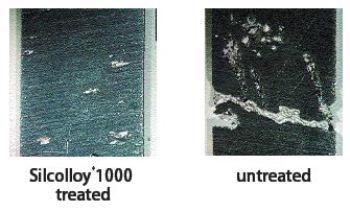
Figure 1. Type 316L stainless steel illustrates crevice corrosion whereas the same material when treated with Silcolloy® 1000 exhibits only minor pitting corrosion (ASTM G 48, Method B).
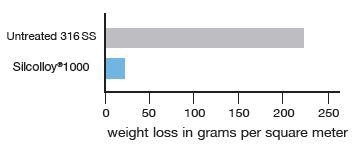
Figure 2. Silcolloy1000 treated stainless steel outperforms uncoated metal by an order of magnitude in chloride environments.
Improvement in Reliability while Cutting Down Costs
Within 5 years of installation, 316L gas delivery systems that are exposed to corrosive settings need to be replaced. Replacing 316L stainless steel with a high performance alloy can result in a five-fold increase in system cost. The substituted alloy may still undergo metal ion contamination.
Enhancing the rust resistance of 316L stainless steel 10 times, the Silcolloy1000 coating treatment reduces costly maintenance, and field failures that are caused by steel corrosion.
Figure 3 shows a comparison of the cost of Silcolloy1000 coating treatment with Hastelloy™ C22 construction for a common gas delivery system. Silcolloy1000 treatment saves lifecycle cost compared to untreated stainless steel/stainless steel alloys.
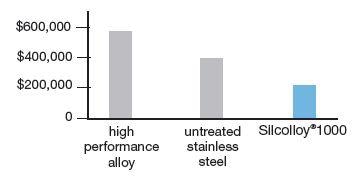
Figure 3. Silcolloy1000 lowers life cycle costs of stainless steel or stainless steel alloys (US$).
Satisfies Increasing Industry Requirements
Product performance is not the only success factor for semiconductor manufacturers. It is also necessary to make products efficiently in the required volumes, and to deliver them on time without affecting the cost targets.
As per the International Technology Roadmap for Semiconductors, Moore's Law can only be realized with consistently near-100% yield improvement, and related productivity upgrades.
SilcoTek's semiconductor treatment solutions aid in the prevention of costly maintenance and loss of production time by protecting vital deposition and etch components such as showerheads, gas delivery systems, in-chamber parts, and others.
Increase Yield, Reduce Waste, and Better Process Control with Silcolloy® and Semicon-modified Dursan®
SilcoTek's patented coating treatments are designed for semiconductor manufacture, and offer a chemically non-reactive, pure amorphous silicon surface, which resists corrosion and particle contamination.
Silcolloy® and modified Dursan® offer protection for manufacturing equipment, help to detect defects easier, ensure stabilized processes and increased output. They reduce data and output variation caused by corrosion of certain chemicals such as HCl, HBr, NF3 and others.
SilcoTek® Treatments Reduce Pump-Down Time
Vacuum chambers treated with SilcoGuard1000 can provide significant productivity improvements in semiconductor processes that require frequent pump-downs. Contaminants, such as water vapor, in process vacuum chambers can lower evacuation rates, ultimate base pressures, and process throughput.
Applying SilcoGuard1000 on the uncovered surfaces of vacuum systems reduces outgassing rates, and provides productivity benefits to process chambers that need efficient and quick evacuations. Figure 4 shows a comparison of pump-down rates for an untreated chamber and a SilcoGuard treated chamber.
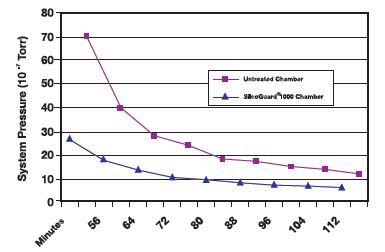
Figure 4. SilcoGuard1000 reduces pump-down times by 2.5 times and even more, for treated chambers, in comparison to untreated chambers.
Conclusion
SilcoTek enables semiconductor manufacturers to meet the productivity and cost challenges by enhancing stainless steel’s surface performance. While SilcoTek treatments can be used on existing process components, custom treatments are also available for process-specific parts and uses.
Download the brochure for more about Silcolloy® treatments from SilcoTek.
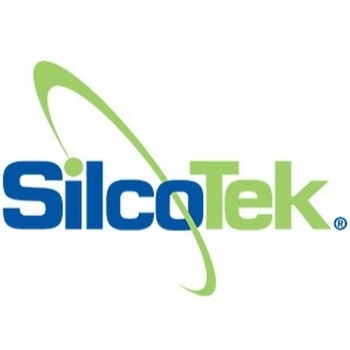
This information has been sourced, reviewed and adapted from materials provided by SilcoTek.
For more information on this source, please visit SilcoTek.